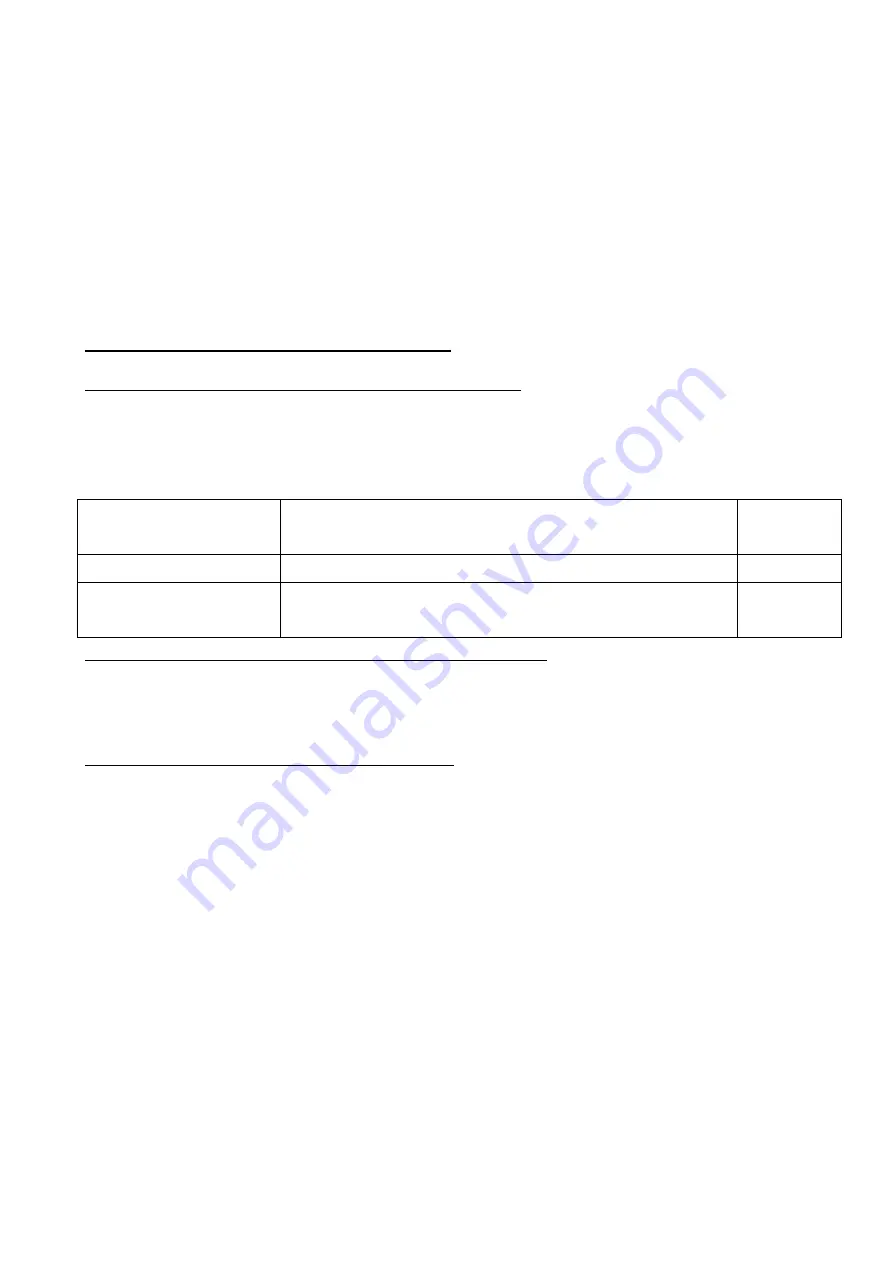
499
communication or DI/DO, the overall pulse number calculation is as follows.
Total pulse number = r (number of revolutions) x 4 pulse number (0~4194303).
If the motor has rotated 10 cycles with 50000 pulse, the total pulse number is as follows
according to the above calculation:
The total pulse value = 10 x 50000
= 41993040 (pulse)
Method of reading motor absolute position
(1)Read the absolute position with communication.
Generally, you can use parameters which is in the status monitoring communication parameter
table in section 9.4 to read the data, and it is recommended to use the "Motor Feedback Pulse
Number (before E-Gear ratio)". The following is a brief table.
Communication
address
Item
Data
length
0x0000
Motor feedback pulse number(after E-Gear ratio) [pulse]
2word
0x0024
Motor feedback pulse number(before E-Gear ratio)
[pulse]
2word
(2)Read absolute position by PLC DIO communication
Return the position through the DI/DO handshake communication between the PLC and the
drive, you can refer to the descriptions in sections 13.1 and 13.2.
(3) Returning position by parameter setting
By setting parameter PA30 with communication, the encoder status and motor absolute position
are updated. If PA30 is set to 1, the drive does not clear the error when reading the position
value. If PA30 is set to 2, the drive clears the error at the same time when reading the position
value.
The servo motor moves slightly forward and backward to correct its position even it is stopped.
To avoid the difference between the reading motor position and actual positions, you can set
PA30 to have the motor’s actual position updated to the servo drive, and clears the position
error at the same time. After encoder status and motor absolute position are updated, PA30 is
automatically reset to 0. It means the controller can access the parameter values.
When the encoder status shows “absolute position lost” or “number of revolutions overflow”, it
means the reading absolute position is invalid. In this case, the coordinate initialization or
homing must be performed again.
Summary of Contents for SDP Series
Page 33: ...20 400V series DC 24V Power supply Note terminal P N cannot be grounded ...
Page 45: ...32 4 The last step is to fasten the screw of housing ...
Page 385: ...372 ...
Page 405: ...392 ...
Page 499: ...486 SME L040 SME L075 SME L100 SME L150 ...
Page 500: ...487 SME L200 SME L300 SME M100 SME M150 ...
Page 509: ...496 When the load reaches 300 the operation time is 5 51 seconds ...
Page 555: ...542 14 5 Manual version and revision history Manual version V1 00 Release month July 2022 ...