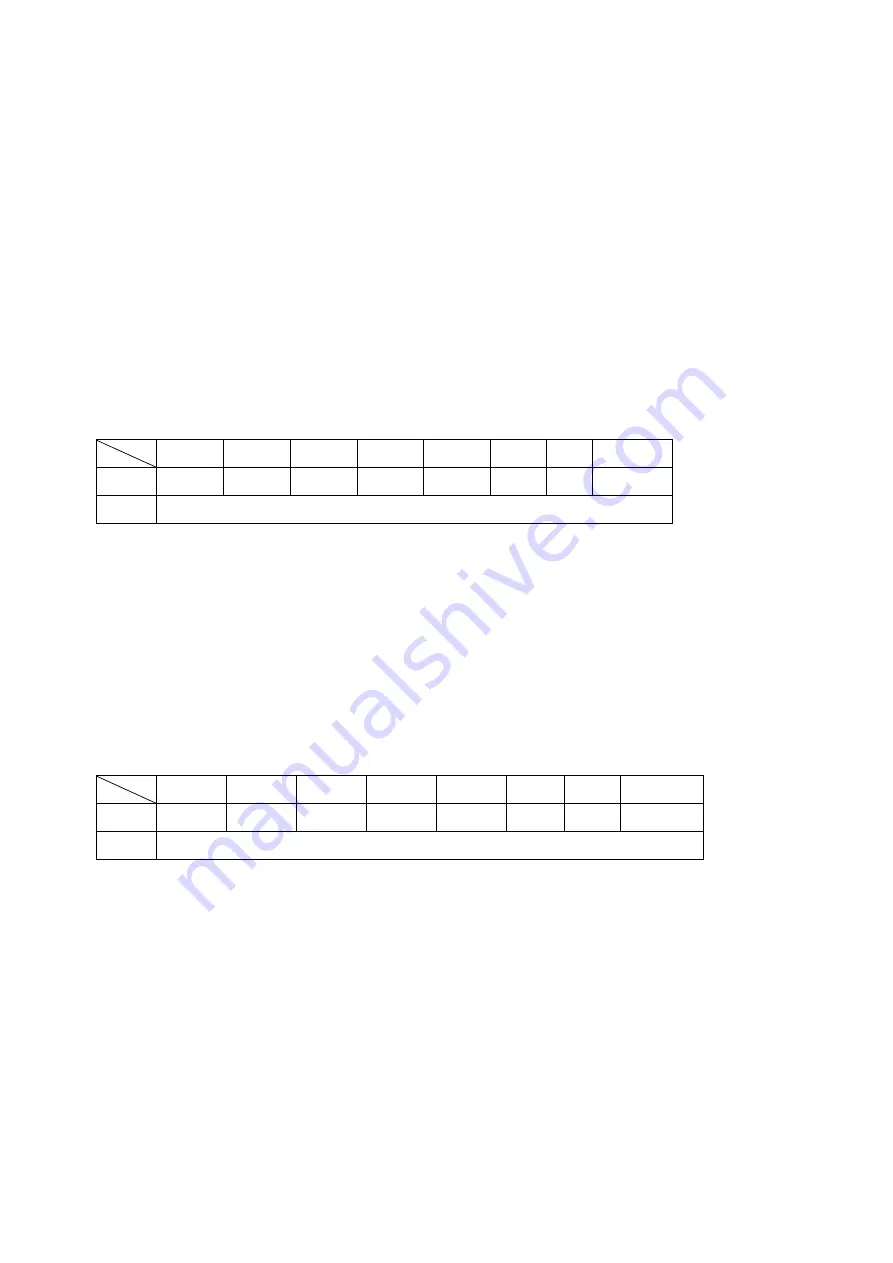
207
Definition of PR program path
There are a total of 126 parameters which is PE03~PE98 & PF01~PF30 to set 63 groups of
PR programs (PATH#01~PATH#63). PATH#01 can be set by PE03 and PE04, PATH#02 can
be set by PE05 and PE06. . . PATH#48 can be set by PE97 and PE98, PF#49 can be set by
PF01 and PF02. . . PATH#63 can be set by PF29 and PF30. Therefore, each 63 groups of PR
program has two parameters to set its functions. The following introduces the 63 groups of PR
programs, take the parameters PE03 and PE04 of PATH#01 as example, and the setting of
the rest of the PR programs follows the same rule.
The first parameter of each PR program is the function setting parameter, the second
parameter is the data setting parameter, the definition of the function setting parameter is
shown in the following table: (take PATH#01 as an example)
31~28 27~24 23~20 19~16 15~12 11~8 7~4 3~0 BIT
PE03 −
−
−
−
−
−
−
TYPE
PE04 DATA(32bit)
In which, the TYPE determines the path form and function, its definition is as follows:
TYPE=1 is speed control, TYPE=2 is positioning control, TYPE=3 is auto positioning control,
TYPE=7 is program jump, TYPE=8 is parameter writing, TYPE=A is indexing positioning
control, and TYPE=2 or 3 are both positioning control, the difference is that TYPE=3 can
automatically execute the next program, so there are five different control types including
speed control, positioning control, program jump, parameter writing and index positioning.
Speed control(TYPE=1): its parameter definition shows in below table:(take PATH#01 for
example)
31~28 27~24 23~20 19~16 15~12 11~8 7~4 3~0 BIT
PE03 x
x
DLY
x
DEC
ACC OPT 1
PE04 DATA(32bit): target speed(UNIT is determined by the OPT setting.)
※
When this command is executed, the motor starts to accelerate (or decelerate) at current
speed (not necessarily as 0), once the target speed is reached, the command is completed.
After completion, the command continues to output at this speed without stopping.
The definition of OPT option is as follows:
Summary of Contents for SDP Series
Page 33: ...20 400V series DC 24V Power supply Note terminal P N cannot be grounded ...
Page 45: ...32 4 The last step is to fasten the screw of housing ...
Page 385: ...372 ...
Page 405: ...392 ...
Page 499: ...486 SME L040 SME L075 SME L100 SME L150 ...
Page 500: ...487 SME L200 SME L300 SME M100 SME M150 ...
Page 509: ...496 When the load reaches 300 the operation time is 5 51 seconds ...
Page 555: ...542 14 5 Manual version and revision history Manual version V1 00 Release month July 2022 ...