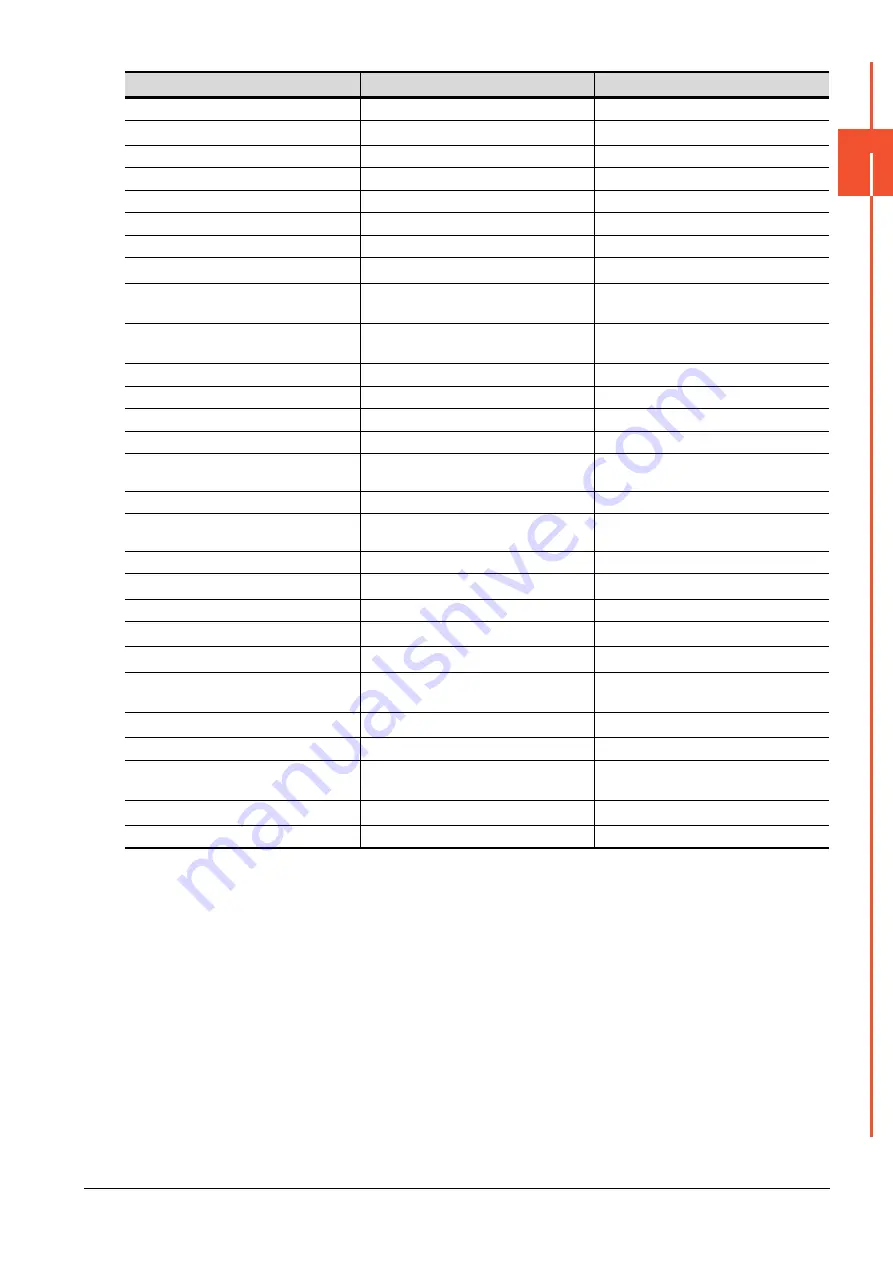
2.1 MELSEC iQ-R, RnMT/NC/RT, CR800-D (GT27, GT25 only)
2 - 25
2
DE
VICE RANGE THA
T
CAN BE SE
T
• Extension setting No.3 parameter
*1
For the parameters prefixed by an asterisk (*), setting becomes effective when the power is turned off once and back on after
setting the parameter data.
*2
Compatible with only R-J4-
□
B(-RJ).
*3
Compatible with only R-J4-
□
GF(-RJ).
*4
Compatible with MR-JE-
□
BF and MR-J4-GF(-RJ).
Device name
Item
Symbol
*1
PF1, PF1001
For manufacturer setting
-
PF2, PF1002
Function selection F-2
*2
*FOP2
PF3 to PF5, PF1003 to PF1005
For manufacturer setting
-
PF6, PF1006
Function selection F-5
*FOP5
PF7 to PF11, PF1007 to PF1011
For manufacturer setting
-
PF12, PF1012
Electronic dynamic brake operating time
DBT
PF13 to PF17, PF1013 to PF1017
For manufacturer setting
-
PF18, PF1018
STO diagnosis error detection time
*4
*STOD
PF19, PF1019
Friction trouble prediction compen. coefficient
1
*3
TSL
PF20, PF1020
Friction trouble prediction compen. coefficient
2
*3
TIC
PF21, PF1021
Drive recorder switching time setting
DRT
PF22, PF1022
For manufacturer setting
-
PF23, PF1023
Vibration tough drive - Oscillation detection level
OSCL1
PF24, PF1024
Vibration tough drive function selection
*OSCL2
PF25, PF1025
SEMI-F47 function - Instantaneous power
failure detection time
CVAT
PF26 to PF30, PF1026 to PF1030
For manufacturer setting
-
PF31, PF1031
Machine diagnosis function - Friction judgement
speed
FRIC
PF32 to PF33, PF1032 to PF1033
For manufacturer setting
-
PF34, PF1034
Machine diagnosis function selection
*3
*MFP
PF35 to PF39, PF1035 to PF1039
For manufacturer setting
-
PF40, PF1040
Machine trouble prediction parameter
*3
MFPP
PF41, PF1041
Trouble prediction motor total move distance
*3
FPMT
PF42, PF1042
Friction trouble prediction average
characteristic
*3
PAV
PF43, PF1043
Friction trouble prediction standard deviation
*3
PSD
PF44, PF1044
For manufacturer setting
-
PF45, PF1045
Vibration trouble prediction average
characteristic
*3
VAV
PF46, PF1046
Vibration trouble prediction standard deviation
*3
VSC
PF47 to PF64, PF1047 to PF1064
For manufacturer setting
-
Summary of Contents for GOT2000 Series
Page 2: ......
Page 84: ......
Page 432: ...6 58 6 6 Precautions ...
Page 578: ...9 54 9 6 Precautions ...
Page 726: ...12 84 12 5 Precautions ...
Page 756: ......
Page 822: ...14 66 14 4 Device Range that Can Be Set ...
Page 918: ...15 96 15 7 Precautions ...
Page 930: ...16 12 16 6 Precautions ...
Page 964: ......
Page 1002: ...19 38 19 7 Precautions ...
Page 1022: ...20 20 20 5 Precautions ...
Page 1023: ...MULTI CHANNEL FUNCTION 21 MULTI CHANNEL FUNCTION 21 1 ...
Page 1024: ......
Page 1054: ...21 30 21 5 Multi channel Function Check Sheet ...
Page 1055: ...FA TRANSPARENT FUNCTION 22 FA TRANSPARENT FUNCTION 22 1 ...
Page 1056: ......
Page 1223: ......