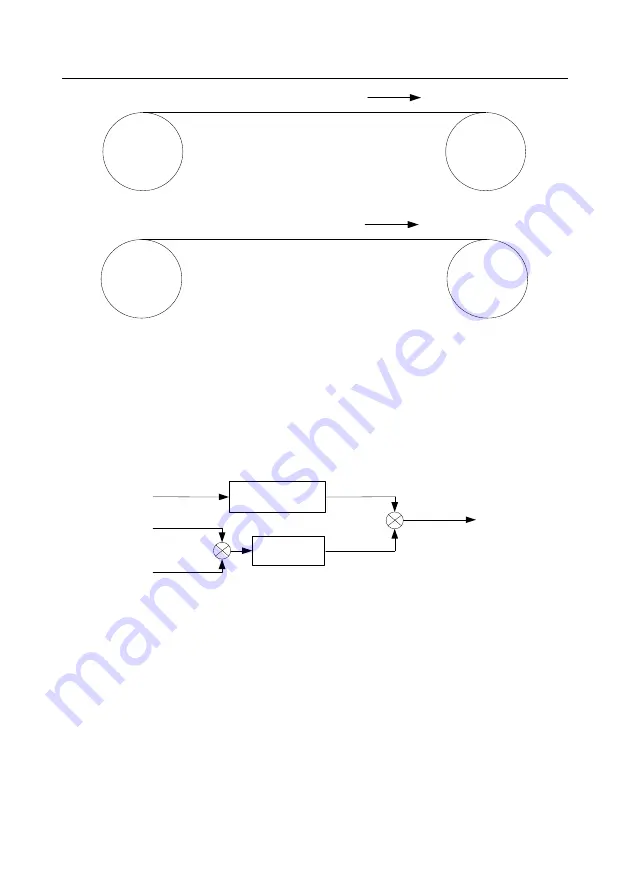
Goodrive350A series high-performance multifunction VFD
Basic operation guidelines
-135-
Unwinding in speed mode
Winding in torque mode
V
V
Unwinding in torque mode
Winding in speed mode
5.5.20.2 Speed control
The detection feedback signal is needed in the closed-loop adjustment. PID calculation is carried out
according to the feedback signal for the motor speed regulation, linear speed and stable tension
control. If the tension rocker or floating roller is used for feedback, changing the set value (PID
reference) may change the actual tension, and at the same time, changing the mechanical
configuration such as the tension rocker or floating roller weight can also change the tension.
The control principle is as follows.
Calculate the frequency
according to the linear
speed
PID regulation
+
+
Linear speed
Tension reference
Tension feedback
Basic reference frequency
Inching
frequency
Motor reference
frequency
+
-
Related modules:
(1) Linear speed input module: It is important for the calculation of the basic setting frequency
according to the linear speed and the calculation of roll diameter according to the linear speed.
(2) Real-time roll diameter calculation module: The calculation accuracy of roll diameter determines
the control performance. The roll diameter can be calculated according to the VFD output frequency
and the linear speed. In addition, it can also be calculated through the thickness or sensor. The linear
speed is widely used for the calculation. If the set linear speed is used for the calculation, you you
choose whether to enable the function of roll diameter change limiting.
(3) PID regulation module: There are two groups of PID parameters in P09. The linear speed
synchronization and stable tension can be kept through PID regulation. PID parameters can be
modified based on site commissioning. The two groups of PID parameters can be switched for PID