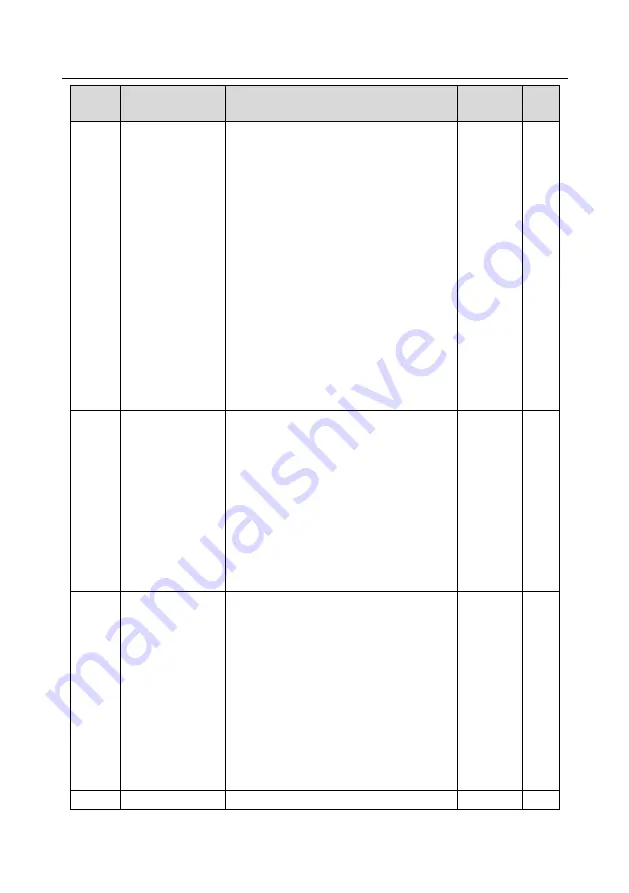
Goodrive350A series high-performance multifunction VFD
Function parameter list
-201-
Function
code
Name
Description
Default
Modify
source
0: AI1
1: AI2
2: AI3
3: HDIA
4: Modbus/Modbus TCP communication
5: PROFIBUS/CANopen/DevicneNET
communication
6: Ethernet communication
7: HDIB
8: EtherCAT/PROFINET/EtherNet IP
communication
9: Programmable card
10: Reserved
Note:
The reference channel and feedback
channel cannot be duplicate. Otherwise,
effective PID control cannot be achieved.
P09.03
PID output
characteristics
selection
0: PID output is positive. When the feedback
signal is greater than the PID reference value,
the output frequency of the VFD will decrease
to balance the PID. Example: PID control on
strain during unwinding.
1: PID output is negative. When the feedback
signal is greater than the PID reference value,
the output frequency of the VFD will increase
to balance the PID. Example: PID control on
strain during unwinding.
0
○
P09.04
Proportional gain
(Kp)
The function is applied to the proportional
gain P of PID input.
P determines the strength of the whole PID
adjuster. The value 100 indicates that when
the difference between the PID feedback
value and given value is 100%, the range
within which the PID regulator can regulate
the output frequency command is the max.
frequency (ignoring integral function and
differential function).
Setting range: 0.00
–100.00
1.80
○
P09.05
Integral time (Ti)
It determines the speed of integral regulation
0.90s
○