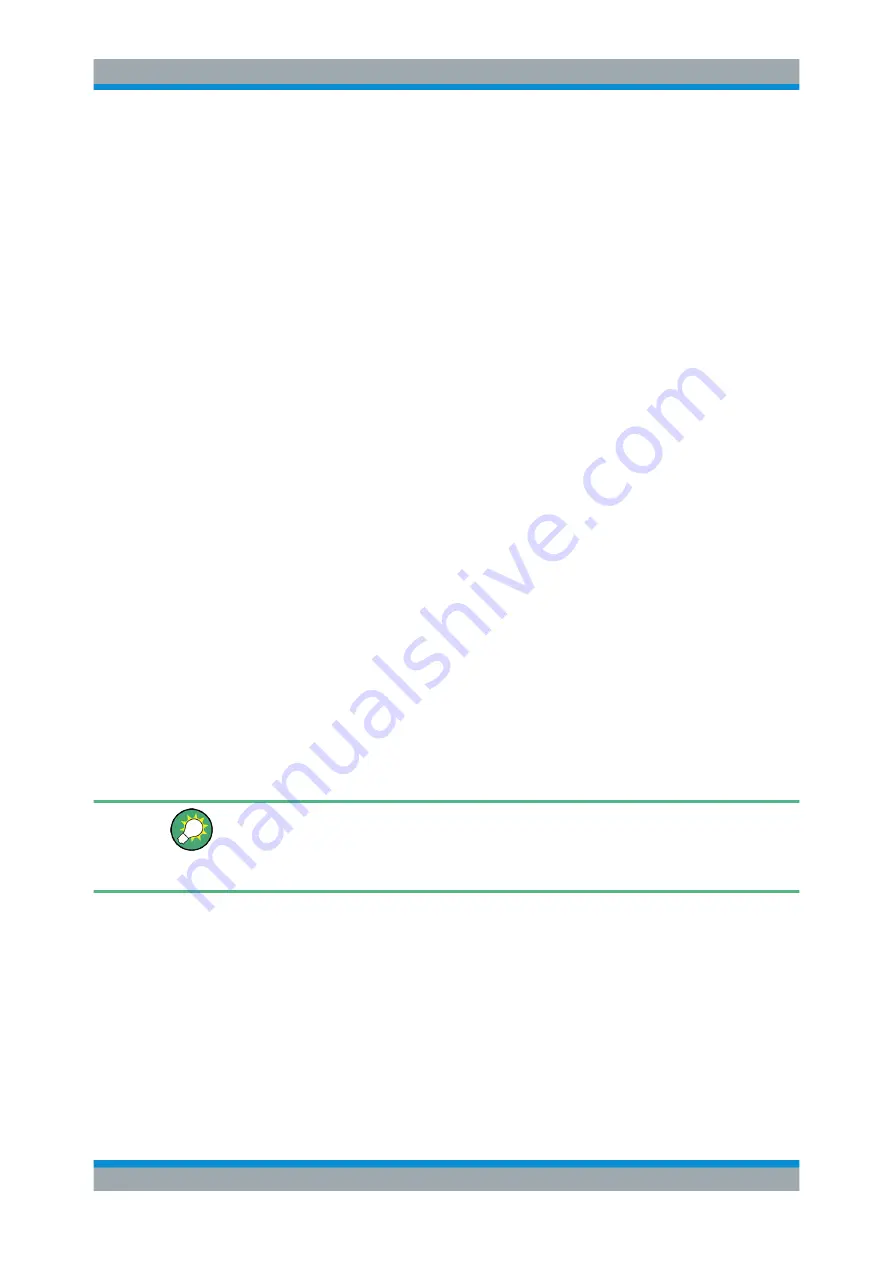
Concepts and Features
R&S
®
ZNB/ZNBT
148
User Manual 1173.9163.02 ─ 53
5.5
Calibration
Calibration or system error correction is the process of eliminating systematic, reprodu-
cible errors from the measurement results (S-parameters and derived quantities; see
on page 90). The process involves the following stages:
1. A set of calibration standards is selected and measured over the required sweep
range.
For many calibration types, the magnitude and phase response of each calibration
standard (i.e. its S-parameters if no system errors occur) must be known within the
entire sweep range. In some calibration procedures (TRL, TNA, TRM), part of the
characteristics of the standards can be auto-determined due to implicit redundancy
(self-calibration).
2. The analyzer compares the measurement data of the standards with their known,
ideal response. The difference is used to calculate the system errors using a partic-
ular error model (calibration type) and derive a set of system error correction data.
3. The system error correction data is used to correct the measurement results of a
DUT that is measured instead of the standards.
Calibration is always channel-specific because it depends on the hardware settings, in
particular on the sweep range. This means that a system error correction data set is
stored with the calibrated channel.
The analyzer provides a wide range of sophisticated calibration methods for all types of
measurements. Which calibration method is selected depends on the expected system
errors, the accuracy requirements of the measurement, on the test setup and on the
types of calibration standards available.
Due to the analyzer's calibration wizard, calibration is a straightforward, menu-guided
process. Moreover, it is possible to perform the entire calibration process automatically
using a Calibration Unit (e.g. R&S
ZN-Z5x or R&S
ZN-Z15x).
The system error correction data determined in a calibration procedure are stored on
the analyzer. You can read these correction data using the remote control command
[SENSe<Ch>:]CORRection:CDATa
. You can also replace the correction data of the
analyzer by your own correction data sets.
Calibration