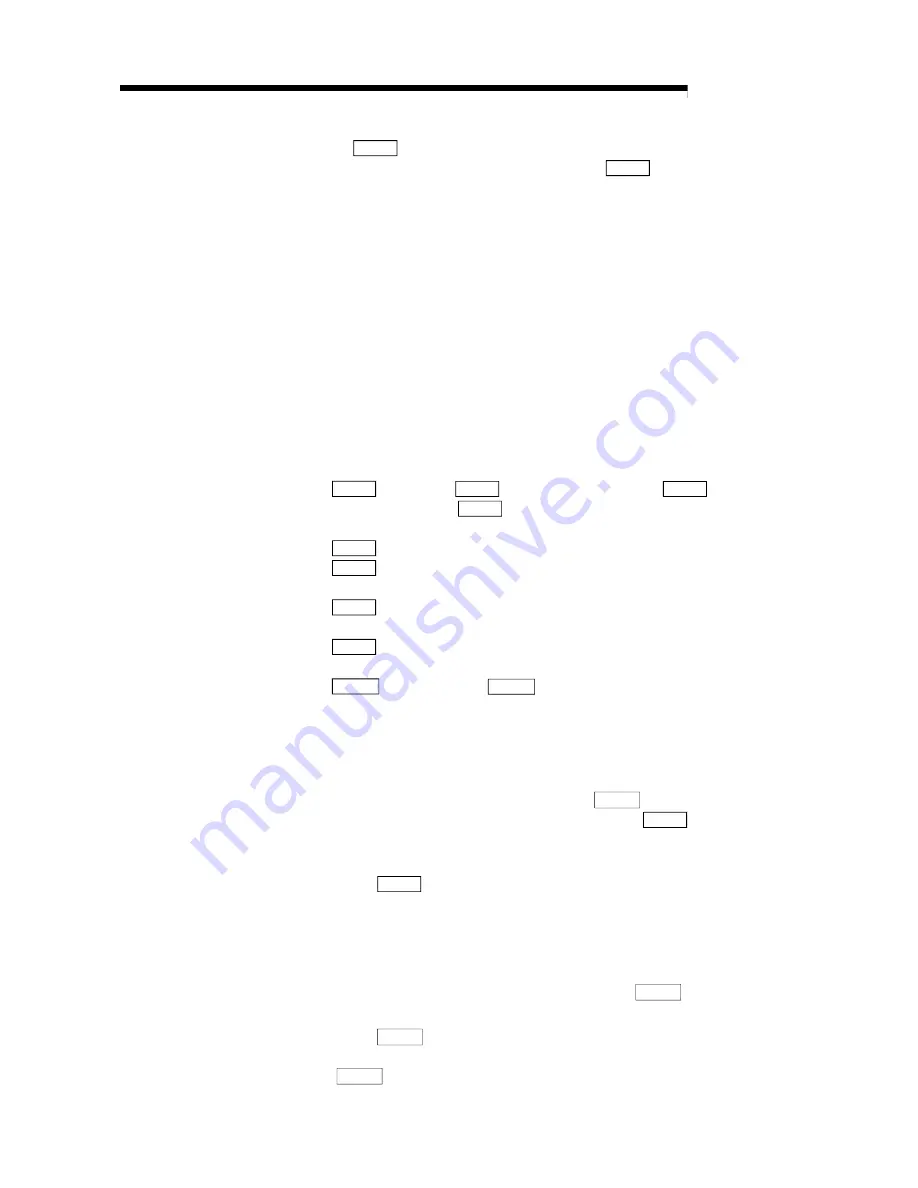
12 - 68
MELSEC-A
12 CONTROL AUXILIARY FUNCTIONS
(6) When "
Da.2
Control method" "0D
H
: Speed control (forward run)" or "0E
H
:
Speed control (reverse run)" is to be executed, "
Pr.22
Current feed value
during speed control" must be set to "1: Update current feed value". If either of
the above control methods is executed at the setting of other than "1", an error
"control method setting error" (error code: 524) occurs.
(7) If the servomotor shaft has rotated more than 15000 turns without the AD75
and servo amplifier making communication, e.g. at power-off, absolute position
restoration may not be made normally at the next power-on.
If external force, etc. may cause the servomotor shaft to rotate more than
15000 turns, use the servomotor equipped with brake, for example, to secure
the servomotor shaft.
(8) When any of the following parameters has been changed from the setting at
execution of a machine zero point return, always make a machine zero point
return. If a machine zero point return is not executed, normal absolute position
restoration cannot be performed.
(a) Basic parameters 1
Pr.1
Unit setting,
Pr.2
No. of pulses per rotation,
Pr.3
Movement
amount per rotation,
Pr.4
Unit magnification
(b) Detailed parameters 1
Pr.13
Software stroke limit upper limit value,
Pr.14
Software stroke limit lower limit value
(c) Zero point return basic parameters
Pr.47
Zero point address
(d) Zero point return detailed parameters
Pr.59
Absolute position restoration selection
(e) Servo basic parameters*
Pr.101
Amplifier setting,
Pr.107
Rotation direction
*: When the servo basic parameters in above (e) are changed after the AD75
and servo amplifier has started communication, power the AD75 or servo
amplifier OFF, then ON and make communication between the AD75 or servo
amplifier.
(9) If either of the following settings is made with " Md.121 Absolute position
restoration mode" set to "1: infinite length mode" and "
Pr.59
Absolute
position restoration selection" set to "1: infinite length mode", an error occurs
when the PLC READY signal (Y1D) turns from OFF to ON.
(a) When "
Pr.1
Unit setting" is set to other than "2: degree"
Error "outside unit setting range" (error code: 900)
(b) When the software stroke limit function (refer to section 12.4.3) is set valid
Error "software stroke limit upper limit" (error code: 921), error "software
stroke limit lower limit" (error code: 922)
(10)Every time a machine zero point return is executed, "Md.120 FeRAM access
count" increases as described below.
(a) When "Md.121 Absolute position restoration mode" is switched between the
"standard mode" and "infinite length mode"
"Md.120 FeRAM access count" increases by "4".
Summary of Contents for A1SD75M1
Page 2: ......
Page 20: ...A 18 MEMO...
Page 22: ...MEMO...
Page 27: ...1 5 MELSEC A 1 PRODUCT OUTLINE MEMO...
Page 42: ...1 20 MELSEC A 1 PRODUCT OUTLINE MEMO...
Page 52: ...2 10 MELSEC A 2 SYSTEM CONFIGURATION MEMO...
Page 111: ...5 21 MELSEC A 5 DATA USED FOR POSITIONING CONTROL MEMO...
Page 115: ...5 25 MELSEC A 5 DATA USED FOR POSITIONING CONTROL MEMO...
Page 123: ...5 33 MELSEC A 5 DATA USED FOR POSITIONING CONTROL MEMO...
Page 127: ...5 37 MELSEC A 5 DATA USED FOR POSITIONING CONTROL MEMO...
Page 167: ...5 77 MELSEC A 5 DATA USED FOR POSITIONING CONTROL MEMO...
Page 193: ...5 103 MELSEC A 5 DATA USED FOR POSITIONING CONTROL MEMO...
Page 276: ...5 186 MELSEC A 5 DATA USED FOR POSITIONING CONTROL MEMO...
Page 332: ...7 18 MELSEC A 7 MEMORY CONFIGURATION AND DATA PROCESS MEMO...
Page 334: ...MEMO...
Page 422: ...9 64 MELSEC A 9 MAIN POSITIONING CONTROL MEMO...
Page 446: ...10 24 MELSEC A 10 ADVANCED POSITIONING CONTROL MEMO...
Page 472: ...11 26 MELSEC A 11 MANUAL CONTROL MEMO...
Page 576: ...12 104 MELSEC A 12 CONTROL AUXILIARY FUNCTIONS MEMO...
Page 745: ......