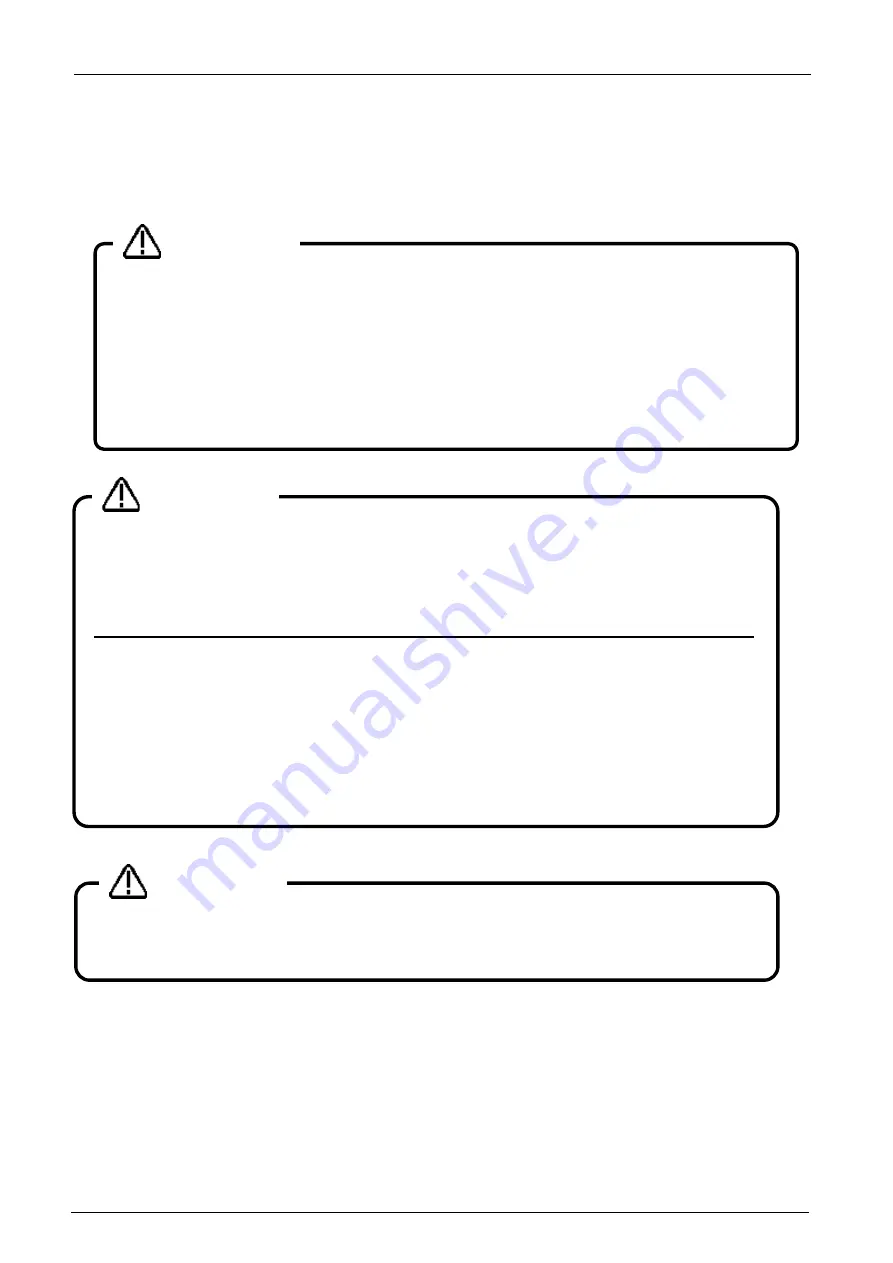
20-490
20-490
20.3. Tact Time Calculation
You can calculate the tact time and axis load level of the operation command section of programs created by
using the simulation function.
RV-F and RH-F series robots can calculate the axis load level.
20.3.1. Conditions for tact time calculation
Note that the following restrictions are applied to calculation of the tact time.
Tact time calculation
The calculated tact time varies with the performance and load status of the computer used and will
not completely match the actual robot operating time (tact time).
Use this function as a rough yardstick for tact time study.
Under correct conditions, the results of tact time calculation with this software have an error of
about ±3% compared to the actual robot operating time (tact time).
For details on tact time deviation, see
"20.3.3 Causes of tact time deviation".
Caution
Be aware that tact time may not be calculated correctly when measuring
tact time with the XYZ position variables, layout parts, or Robot information
displayed in the 3D monitor.
Caution
Axis load level calculation
The axis load level numerically expresses the motor load.
The robot will generate an overload error and stops protecting the motor when the axis load level
exceeds 100%.The calculated axis load level assumes multiple iterations of the same operation.
However, be aware that stop will not occur in simulation even if the load level exceeds 100%.
There is a possibility that continuous operation will not be possible in an actual robot when the
calculated axis load level is high. You should lower the operation frequency with the Dly command,
and lower operation speed and the acceleration with the Accel and the Ovrd commands, etc.
Changing the operation point may lower the operation point.
Complete agreement with the calculated axis load level cannot be guaranteed because the axis
load level of an actual robot is influenced in robot individual differences, the ambient temperature, the
condition of the robot, etc. Use this function as a rough yardstick for studying robot movement.
Caution
Summary of Contents for 3F-14C-WINE
Page 84: ...8 84 8 84 Figure 8 21 Parameter transfer procedure 1 2 2 ...
Page 393: ...18 393 18 393 Figure 18 1 Starting the Oscillograph ...
Page 413: ...18 413 18 413 Figure 18 24 Output to Robot program Selection ...
Page 464: ...18 464 18 464 Figure 18 72 Starting the Tool automatic calculation ...
Page 545: ...21 545 21 545 Figure 21 55 Hide display of user mechanism ...
Page 624: ...24 624 24 624 Figure 24 4 Document output example ...