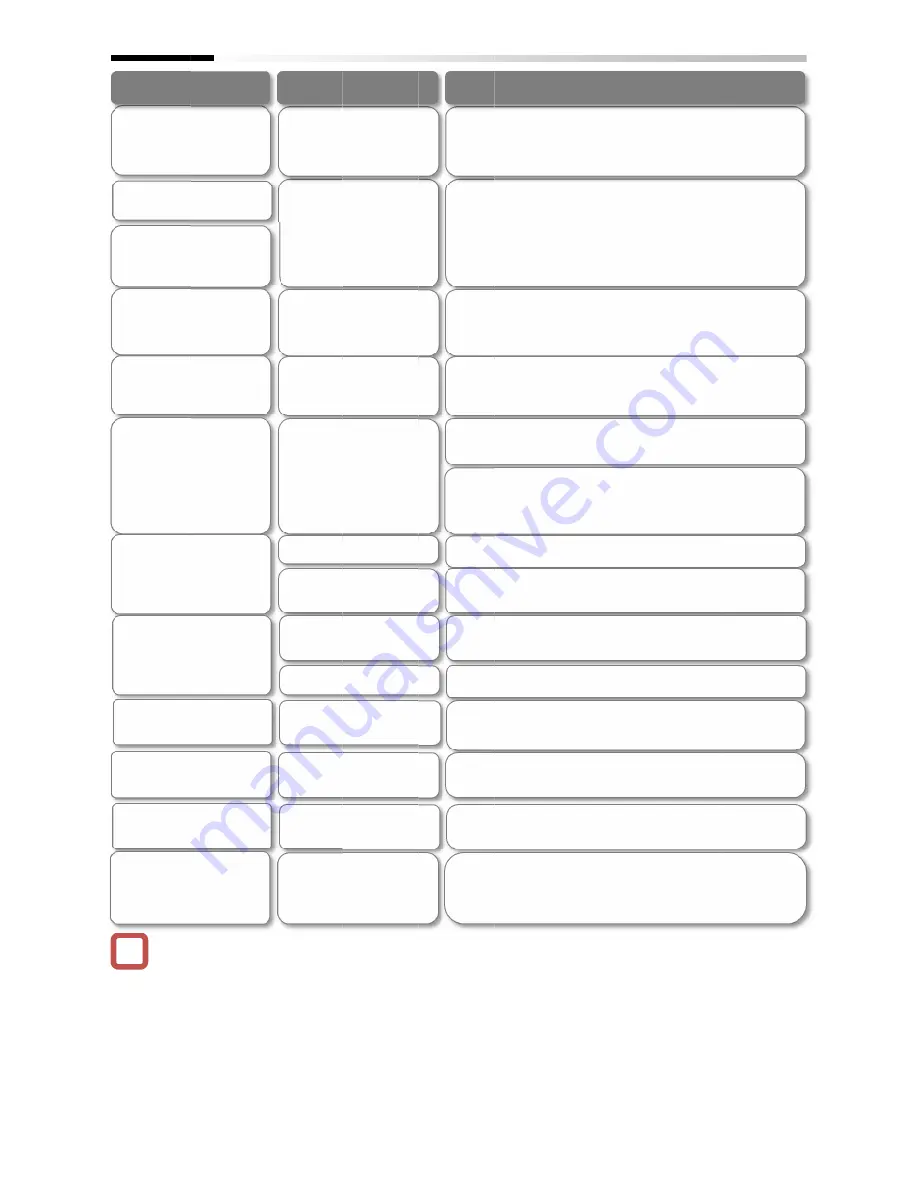
Chapter 12
•
Over current occurs at the start
At the start, the motor loses
synchronization and no
acceleration is observed.
A long starting time is
requi
Fluctuating r
at low speeds
frequency(switch)
lower)
Hunting occurs at low speeds
(at the lowest
freque
lower)
Shock or over current occurs
at about the lowest frequency
(switch).
Hunting occurs at higher
speeds (at the lowest
frequency (switch) or higher).
A long initial position estimation
time is requir
A movement in the opposite
direction occurs while the initial
position est
While the initial position
estimation is being used, over
current errors may occur.
Frequency
re
At the start, rotating
temporarily in the opposite
direction to the intended one.
Chapter 12
• When the revolution of the motor is hindered by
breaking or the motor lock caused by
objects may cause over current or the like. When
no such adjustment as ones mentioned above
improves the state, checking the portion around the
motor may sometimes improves it.
!
Over current occurs at the start
At the start, the motor loses
synchronization and no
acceleration is observed.
A long starting time is
required.
Fluctuating revolutions occur
at low speeds (at the lowest
frequency(switch)
lower)
Hunting occurs at low speeds
(at the lowest
frequency(switch)
lower)
Shock or over current occurs
at about the lowest frequency
(switch).
Hunting occurs at higher
speeds (at the lowest
frequency (switch) or higher).
A long initial position estimation
time is required.
A movement in the opposite
direction occurs while the initial
position estimation is being used.
While the initial position
estimation is being used, over
current errors may occur.
Frequency-synchronized
re-start may cause errors.
At the start, rotating
temporarily in the opposite
direction to the intended one.
Phenomenon
Chapter 12
When the revolution of the motor is hindered by
breaking or the motor lock caused by
objects may cause over current or the like. When
no such adjustment as ones mentioned above
improves the state, checking the portion around the
motor may sometimes improves it.
Over current occurs at the start
At the start, the motor loses
synchronization and no
acceleration is observed.
A long starting time is
evolutions occur
(at the lowest
frequency(switch) or even
Hunting occurs at low speeds
ncy(switch) or even
Shock or over current occurs
at about the lowest frequency
Hunting occurs at higher
speeds (at the lowest
frequency (switch) or higher).
A long initial position estimation
ed.
A movement in the opposite
direction occurs while the initial
imation is being used.
While the initial position
estimation is being used, over
current errors may occur.
synchronized
start may cause errors.
At the start, rotating
temporarily in the opposite
direction to the intended one.
Phenomenon
When the revolution of the motor is hindered by
breaking or the motor lock caused by
objects may cause over current or the like. When
no such adjustment as ones mentioned above
improves the state, checking the portion around the
motor may sometimes improves it.
Over current occurs at the start
• Insufficient starting torque
• Misalignment of the output
phases and the motor's
magnetic-
• A long
phase-synchronization time
is required.
• Insufficient starting torque
• There is a motor constant
error.
•
The speed response is too low.
• Load fluctuation occurs at
around the switch.
• Unsynchronized speed
response.
• Distorted wave form of the radio
wave.
A long initial position estimation • Set value for the estimation
is too large.
• The estimation is improperly
conducted.
• Voltage gain is too high.
• Too high revolution speeds
and too large offset of the
phases.
• Misalignment of the output
phases and the motor's
magnetic-
Estimated cause(s)
When the revolution of the motor is hindered by
breaking or the motor lock caused by foreign
objects may cause over current or the like. When
no such adjustment as ones mentioned above
improves the state, checking the portion around the
icient starting torque
Misalignment of the output
phases and the motor's
-pole positions
synchronization time
is required.
Insufficient starting torque
There is a motor constant
The speed response is too low.
Load fluctuation occurs at
around the switch.
Unsynchronized speed
response.
Distorted wave form of the radio
Set value for the estimation
is too large.
The estimation is improperly
conducted.
Voltage gain is too high.
Too high revolution speeds
large offset of the
Misalignment of the output
phases and the motor's
-pole positions
Estimated cause(s)
12-9-21
When the revolution of the motor is hindered by
objects may cause over current or the like. When
improves the state, checking the portion around the
• If an applica
change in the inverter's output frequency monitor
[dA
change the frequencies for the overload limiting
function, the momentary
the over voltage suppr
depending upon the settings of the functions. For
details, see "Chap. 18: Troubleshooting."
icient starting torque
Misalignment of the output
• Enable the initial
• Set the DC braking at the start [AF101] = 01, and after the start, the
time needed for the m
In addition, make an adjustment by incrementing the braking force at
the start [AF108] by 5% each time.
synchronization time
• When the magnetic
braking at the starting, enable the initial
instead of the DC braking at the start. [Hd132]=01
Insufficient starting torque
• Make an adjustment by incrementing the braking force at the start
[AF108] by 5% each time.
There is a motor constant
• Decrement the motor constant R [Hd110] little by little until it reaches
a value = set value × 0.7.
• Increment little by little each of the motor constant Ld [Hd112] and
the motor constant
values = set values × 1.4. Note, however that Ld
The speed response is too low.
• Make an adjustment by incrementing the speed res
5% each time.
• Adjust the lowest frequency (switch) [Hd130].
Load fluctuation occurs at
• Make an adj
response [HA115] by 5% each time.
• Make an adjustment by incrementing the no
5% each time.
Distorted wave form of the radio
Set value for the estimation
• Lower the values [Hd133] to [Hd135] by the same ratio.
* Too low a value may result in an operation in the opposite
direction.
The estimation is improperly
• Raise the values [Hd133] to [Hd135] by the same ratio, or raise the
voltage gain [Hd136] by 5
• Decrement the voltage gain [Hd136] by 5
Too high revolution speeds
large offset of the
• Make an adjustment by incrementing the speed response [HA115]
by 5% each time. Waiting a longer time for the re
the situation.
Misalignment of the output
• Enable the
In the cases of a slight opposite
initial-position estimation function, make an adjustment by
incrementing [Hd137] by 5° at a time.
21
If an application of load results in a great amount of
change in the inverter's output frequency monitor
[dA-01], functions wich change
change the frequencies for the overload limiting
function, the momentary
the over voltage suppr
depending upon the settings of the functions. For
details, see "Chap. 18: Troubleshooting."
Enable the initial-position estimation function. [Hd132]=01
Set the DC braking at the start [AF101] = 01, and after the start, the
time needed for the m
In addition, make an adjustment by incrementing the braking force at
the start [AF108] by 5% each time.
When the magnetic-pole positions are synchronized in the DC
braking at the starting, enable the initial
instead of the DC braking at the start. [Hd132]=01
Make an adjustment by incrementing the braking force at the start
[AF108] by 5% each time.
Decrement the motor constant R [Hd110] little by little until it reaches
a value = set value × 0.7.
Increment little by little each of the motor constant Ld [Hd112] and
the motor constant Lq [Hd112] until they reach their respective
values = set values × 1.4. Note, however that Ld
Make an adjustment by incrementing the speed res
5% each time.
Adjust the lowest frequency (switch) [Hd130].
Make an adjustment by incrementing/decrementing the speed
response [HA115] by 5% each time.
Make an adjustment by incrementing the no
5% each time.
Lower the values [Hd133] to [Hd135] by the same ratio.
* Too low a value may result in an operation in the opposite
direction.
Raise the values [Hd133] to [Hd135] by the same ratio, or raise the
voltage gain [Hd136] by 5
Decrement the voltage gain [Hd136] by 5
Make an adjustment by incrementing the speed response [HA115]
by 5% each time. Waiting a longer time for the re
the situation.
Enable the initial-position estimation function. [Hd132]=01
In the cases of a slight opposite
position estimation function, make an adjustment by
incrementing [Hd137] by 5° at a time.
Exemplar measures to be taken
tion of load results in a great amount of
change in the inverter's output frequency monitor
functions wich change
change the frequencies for the overload limiting
function, the momentary-stop non
the over voltage suppression function may work
depending upon the settings of the functions. For
details, see "Chap. 18: Troubleshooting."
position estimation function. [Hd132]=01
Set the DC braking at the start [AF101] = 01, and after the start, the
time needed for the motor to be stabilized is set in [AF109].
In addition, make an adjustment by incrementing the braking force at
the start [AF108] by 5% each time.
pole positions are synchronized in the DC
braking at the starting, enable the initial
instead of the DC braking at the start. [Hd132]=01
Make an adjustment by incrementing the braking force at the start
[AF108] by 5% each time.
Decrement the motor constant R [Hd110] little by little until it reaches
a value = set value × 0.7.
Increment little by little each of the motor constant Ld [Hd112] and
Lq [Hd112] until they reach their respective
values = set values × 1.4. Note, however that Ld
Make an adjustment by incrementing the speed res
Adjust the lowest frequency (switch) [Hd130].
ustment by incrementing/decrementing the speed
response [HA115] by 5% each time.
Make an adjustment by incrementing the no
Lower the values [Hd133] to [Hd135] by the same ratio.
* Too low a value may result in an operation in the opposite
Raise the values [Hd133] to [Hd135] by the same ratio, or raise the
voltage gain [Hd136] by 5% each time.
Decrement the voltage gain [Hd136] by 5
Make an adjustment by incrementing the speed response [HA115]
by 5% each time. Waiting a longer time for the re
position estimation function. [Hd132]=01
In the cases of a slight opposite-direction movement even in the
position estimation function, make an adjustment by
incrementing [Hd137] by 5° at a time.
Exemplar measures to be taken
Inverter Function
tion of load results in a great amount of
change in the inverter's output frequency monitor
functions wich change automatically
change the frequencies for the overload limiting
stop non-stop function,
ession function may work
depending upon the settings of the functions. For
details, see "Chap. 18: Troubleshooting."
position estimation function. [Hd132]=01
Set the DC braking at the start [AF101] = 01, and after the start, the
otor to be stabilized is set in [AF109].
In addition, make an adjustment by incrementing the braking force at
pole positions are synchronized in the DC
braking at the starting, enable the initial-position estimation function
instead of the DC braking at the start. [Hd132]=01
Make an adjustment by incrementing the braking force at the start
Decrement the motor constant R [Hd110] little by little until it reaches
Increment little by little each of the motor constant Ld [Hd112] and
Lq [Hd112] until they reach their respective
values = set values × 1.4. Note, however that Ld
≤
Lq.
Make an adjustment by incrementing the speed response [HA115] by
Adjust the lowest frequency (switch) [Hd130].
ustment by incrementing/decrementing the speed
Make an adjustment by incrementing the no-load current [Hd131] by
Lower the values [Hd133] to [Hd135] by the same ratio.
* Too low a value may result in an operation in the opposite
Raise the values [Hd133] to [Hd135] by the same ratio, or raise the
each time.
Decrement the voltage gain [Hd136] by 5% each time.
Make an adjustment by incrementing the speed response [HA115]
by 5% each time. Waiting a longer time for the re-start may improve
position estimation function. [Hd132]=01
direction movement even in the
position estimation function, make an adjustment by
incrementing [Hd137] by 5° at a time.
Exemplar measures to be taken
Inverter Function
tion of load results in a great amount of
change in the inverter's output frequency monitor
automatically
change the frequencies for the overload limiting
stop function,
ession function may work
depending upon the settings of the functions. For
details, see "Chap. 18: Troubleshooting."
position estimation function. [Hd132]=01
Set the DC braking at the start [AF101] = 01, and after the start, the
otor to be stabilized is set in [AF109].
In addition, make an adjustment by incrementing the braking force at
pole positions are synchronized in the DC
position estimation function
Make an adjustment by incrementing the braking force at the start
Decrement the motor constant R [Hd110] little by little until it reaches
Increment little by little each of the motor constant Ld [Hd112] and
Lq [Hd112] until they reach their respective
≤
Lq.
ponse [HA115] by
ustment by incrementing/decrementing the speed
load current [Hd131] by
Lower the values [Hd133] to [Hd135] by the same ratio.
* Too low a value may result in an operation in the opposite
Raise the values [Hd133] to [Hd135] by the same ratio, or raise the
each time.
Make an adjustment by incrementing the speed response [HA115]
start may improve
position estimation function. [Hd132]=01
direction movement even in the
position estimation function, make an adjustment by
Exemplar measures to be taken
Inverter Function
tion of load results in a great amount of
depending upon the settings of the functions. For
Set the DC braking at the start [AF101] = 01, and after the start, the
In addition, make an adjustment by incrementing the braking force at
position estimation function
Decrement the motor constant R [Hd110] little by little until it reaches
ponse [HA115] by
load current [Hd131] by
Raise the values [Hd133] to [Hd135] by the same ratio, or raise the
start may improve
Summary of Contents for SJ Series
Page 39: ...5 4 Chapter 5 Included Items Memo ...
Page 55: ...6 16 Chapter 6 Installation Memo ...
Page 91: ...7 36 Chapter 7 Wire Connection and Optional Devices Memo ...
Page 135: ...9 40 Chapter 9 Operating Instructions Memo ...
Page 145: ...10 10 Chapter 10 Test Run Memo ...
Page 159: ...12 2 6 Chapter 12 Inverter Functions Memo ...
Page 169: ...12 3 10 Chapter 12 Inverter Functions Memo ...
Page 195: ...12 5 8 Chapter 12 Inverter Functions Memo ...
Page 217: ...12 8 12 Chapter 12 Inverter Function Memo ...
Page 287: ...12 10 32 Chapter 12 Inverter Functions Memo ...
Page 303: ...12 11 16 Chapter 12 Inverter Functions Memo ...
Page 349: ...12 15 8 Chapter 12 Inverter Function Memo ...
Page 395: ...12 17 34 Chapter 12 Inverter Functions Memo ...
Page 397: ...12 18 2 Chapter 12 Inverter Functions Memo ...
Page 415: ...12 19 18 Chapter 12 Inverter Function Memo ...
Page 581: ...15 10 Chapter 15 Optional Cassettes Memo ...
Page 591: ...16 10 Chapter 16 ProDriveNext EzSQ Memo ...
Page 642: ...18 49 Chapter 18 Tips FAQ Troubleshooting Memo ...
Page 650: ...19 8 Chapter 19 Maintenance and Inspection Memo ...
Page 781: ...Appendix 1 70 Appendix 1 List of Parameters Memo ...