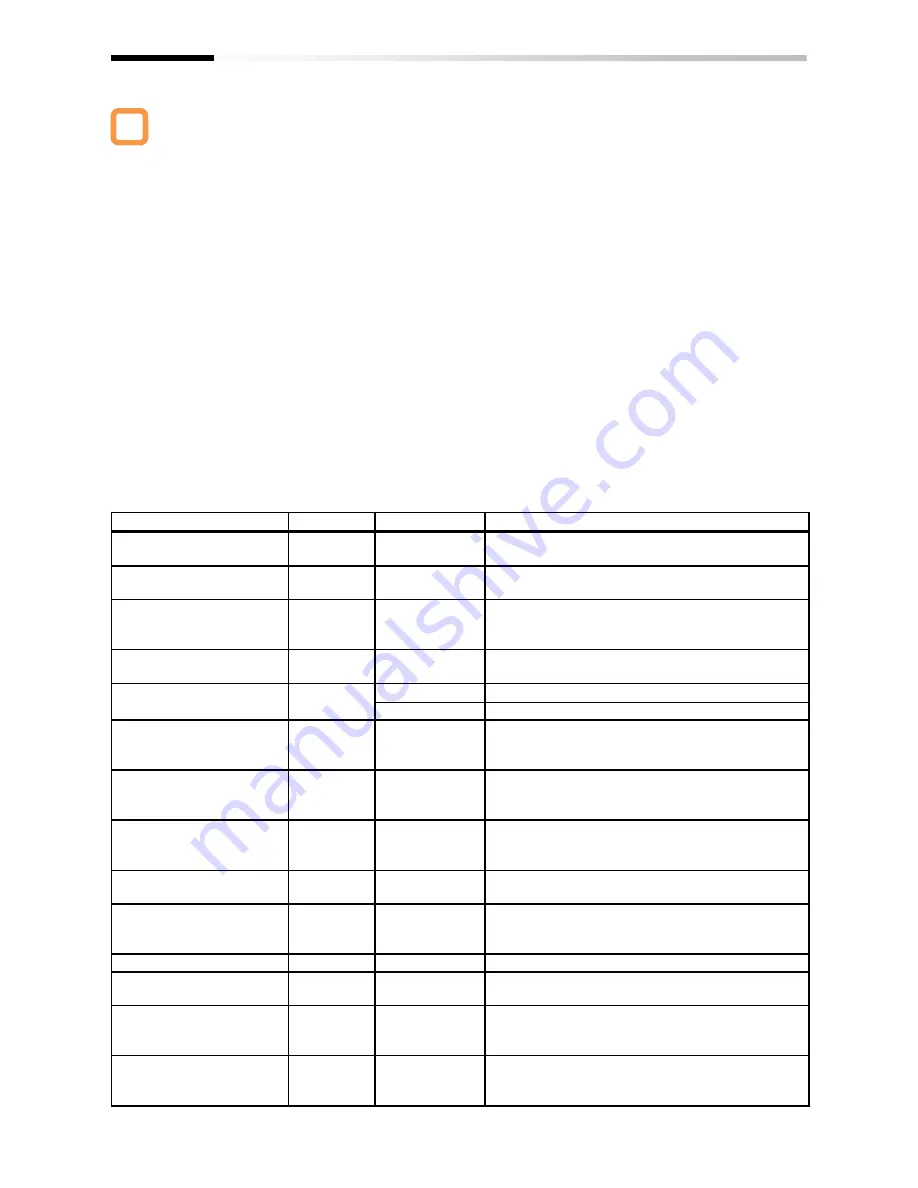
12-9-20
Chapter 12
Inverter Function
Control operation in synchronous start mode
• In this control mode, operations of magnetic-pole
position estimation, synchronous start control, and
sensorless vector control are started in this order.
• In the magnetic-pole position estimation, it is
possible to select whether the motor is started after
the motor's magnetic-pole positions are estimated by
use of the initial-position estimation function or the
magnetic-pole positions are synchronized by use of
the DC braking function.
• In the case of starting after the magnetic-pole
position estimation, estimation operation is
conducted at the start by setting the start method
[Hd132] at 01.
• In the case of the start method [Hd132] being set at
00, the motor is started as its magnetic poles are
synchronized with the output phases. In the case
where the magnetic poles and the output phases are
unsynchronized by a great amount, or in the case
that require a certain starting torque, use the
starting-time DB to synchronize the magnetic-pole
positions and the output phases before the
acceleration.
•
Use [AF108] to adjust the current during a
synchronous starting. Adjustment is possible even
when [AF101] = 00. When a larger torque is
needed than what is needed in the synchronous
starting mode, use of IVMS start mode may
improve the situation. Please contact the sales
officer of our company.
•
The frequency [Hd130] at which the synchronous
start control is switched to the sensorless vector
control is adjusted at the lowest frequency
(switching).
•
When a motor is hunting and vibrating, an
adjustment of the speed response [HA115] and/or
the no-load current [Hd131] may improve the state
of the motor.
•
When the starting-time DB function is used at the
start, see "12.14.2 Start after applying DC
braking."
Parameters for synchronous starting mode
Item
Parameter
Data
Description
Control mode
[AA121]
11
To use synchronous-start type sensorless vector
control (SM/PMM)
Speed response
[HA115]
0~1000(%)
To adjust the responsiveness of the control.
A larger value enhances the responsiveness.
SM(PMM) lowest
frequency (switch)
[Hd130]
0~50(%)
The frequency at which the sensorless vector
control is started.
Set the ratio to the base frequency [Hd104].
SM(PMM) no-load current
[Hd131]
0~100(%)
Set the ratio of the no-load current to the rated
current during the sensorless vector control.
SM(PMM) start method
[Hd132]
00
Initial position estimation is disabled.
01
Initial position estimation is enabled.
SM(PMM) initial position
estimation zero-V
stand-by times
[Hd133]
0~255
This is a stand-by adjustment value to stabilize
the reference value for the initial position
estimation detection.
SM(PMM) initial position
estimation detection
stand-by times
[Hd134]
0~255
This is an adjustment value to stabilize the
current rise of the initial position estimation
operation.
SM(PMM) initial position
estimation detection
times
[Hd135]
0~255
This is a detection-operation adjustment value of
the initial position estimation operation.
SM(PMM) initial position
estimation voltage gain
[Hd136]
0~200(%)
This is a output-voltage adjustment gain of the
initial position estimation operation.
SM(PMM) initial position
estimation magnetic-pole
position offset
[Hd137]
0~359°
To conduct corrections in a case where the initial
position estimation operation has a certain error.
DC braking selection
[AF101]
01
Internal DC braking: enabled
DC braking force at the
start
[AF108]
0~100(%)
To adjust the DC braking force. Setting of 100%
will provide maximum braking force.
DC braking time at the
start
[AF109]
0.0~60.0(s)
Enabled during the internal DC braking.
When the operation command is turned ON, DC
braking is started.
Over current detection
level
[bb160]
Inverter ND
rated current ×
(0.20 to 2.20)
To Set the level at which the over current is
detected.
A
Summary of Contents for SJ Series
Page 39: ...5 4 Chapter 5 Included Items Memo ...
Page 55: ...6 16 Chapter 6 Installation Memo ...
Page 91: ...7 36 Chapter 7 Wire Connection and Optional Devices Memo ...
Page 135: ...9 40 Chapter 9 Operating Instructions Memo ...
Page 145: ...10 10 Chapter 10 Test Run Memo ...
Page 159: ...12 2 6 Chapter 12 Inverter Functions Memo ...
Page 169: ...12 3 10 Chapter 12 Inverter Functions Memo ...
Page 195: ...12 5 8 Chapter 12 Inverter Functions Memo ...
Page 217: ...12 8 12 Chapter 12 Inverter Function Memo ...
Page 287: ...12 10 32 Chapter 12 Inverter Functions Memo ...
Page 303: ...12 11 16 Chapter 12 Inverter Functions Memo ...
Page 349: ...12 15 8 Chapter 12 Inverter Function Memo ...
Page 395: ...12 17 34 Chapter 12 Inverter Functions Memo ...
Page 397: ...12 18 2 Chapter 12 Inverter Functions Memo ...
Page 415: ...12 19 18 Chapter 12 Inverter Function Memo ...
Page 581: ...15 10 Chapter 15 Optional Cassettes Memo ...
Page 591: ...16 10 Chapter 16 ProDriveNext EzSQ Memo ...
Page 642: ...18 49 Chapter 18 Tips FAQ Troubleshooting Memo ...
Page 650: ...19 8 Chapter 19 Maintenance and Inspection Memo ...
Page 781: ...Appendix 1 70 Appendix 1 List of Parameters Memo ...