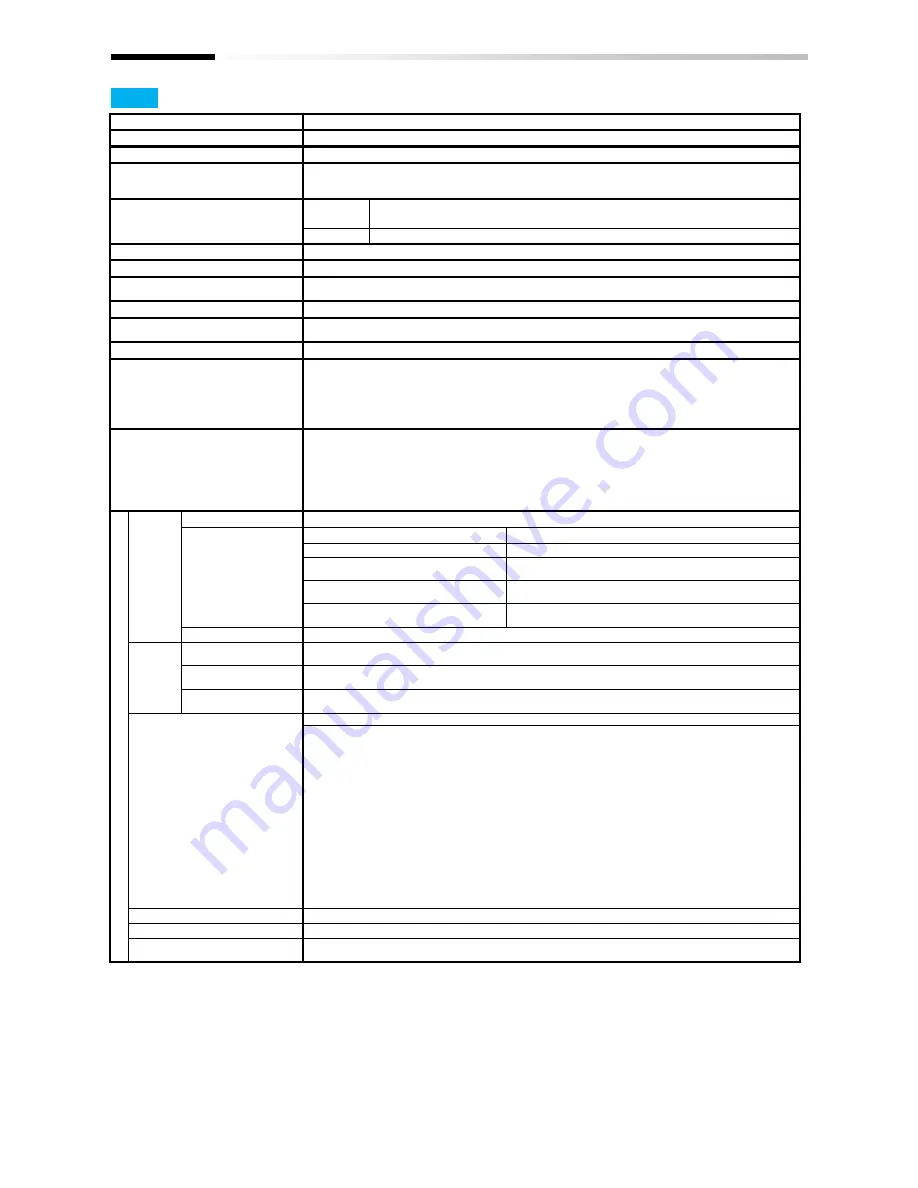
20-4
Chapter 20
Specifications
20.2.3
Common Specifications
*1)
The output frequency range depend on the control and motor used.
When running the inverter exceeding 60Hz, check the maximum
allowable frequency with the manufacturer of the motor.
*2)
When the control mode is changed, unless the motor constant is
appropriately configured, you cannot obtain the desired starting torque or
the inverter may trip.
*3)
The variable range of motor speed may vary depending on your system
or the environment where the motor is used.
Please contact us for
details.
*4)
Both the input power and output power are reference values, which are
not appropriate for use in calculation of efficiency values, etc.
To obtain
an accurate value, use an external device.
*5)
The IGBT error [E030] is generated by the protective function not only for
short circuit protection but also when IGBT is damaged. Depending on
the operating conditions of the inverter, the overcurrent error [E001] may
occur, instead of the IGBT error.
*6)
At the factory default setting, when voltage and current on Ai1/Ai2
terminal is changed using a switch, with input of voltage at 9.8V and
current at 19.8mA, the maximum frequency is commanded.
To change
characteristics, make adjustments using the analog start/end function.
Control mode (output to the motor)
Sine wave PWM control voltage output (line sine wave modulation)
Output frequency range *1)
0.00~590.00Hz
Frequency accuracy
Digital command ±0.01% and analog command ±0.2% (25±10°C) against the maximum frequency
Frequency resolution
Digital setting: 0.01Hz
Analog setting: maximum frequency/4000
(Ai1 terminal/Ai2 terminal: 12bit/0 - +10V or 0 - +20mA, Ai3 terminal 12bit/-10 - +10V)
Control mode
(frequency/voltage calculation) *2)
IM
V/f control (fixed torque/reduced torque/free), automatic boost control, cascade model sensorless
vector control, 0 Hz range sensorless vector control, vector control with sensor.
SM/PMM
Synchronous starting sensorless vector control, IVMS starting smart sensorless vector control
Speed fluctuation *3)
±0.5% (during sensorless vector control)
Acceleration or deceleration time
0.00-3600.00sec (linear, S-shaped, U-shaped, reverse U-shaped, EL-S shaped)
Display monitor
Output frequency, output current, output torque, trip history, I/O terminal status, I/O power *4), P-N voltage and
others described in "Chapter 13 Information Monitoring Functions".
Starting functions
Start after DC braking, frequency collection start, frequency entrainment start, reduced voltage start, retry start
Stopping functions
Free-run stop, DC braking after deceleration stop or terminal DC braking (braking power, operating speed
adjustment)
Stall prevention function
Overload restraining function, overcurrent suppression function, overvoltage suppression function
Protective function *5)
Overcurrent error, Motor overload error, Braking resister Overload error, Overvoltage error, Memory error,
Undervoltage error, Current detector error, CPU error, External trip error, USP error, Ground fault error,
Excessive voltage of accepted power error, Instantaneous power failure error, Temperature detector error,
Reduction of revolutions of cooling fan, Temperature error, Input phase loss error, IGBT error, Output phase loss
error, Thermistor error, Brake error, Low-speed range overload error, Inverter overload error, RS485
communication error, and others described in "Chapter 18 Tips/FAQ/Troubleshooting".
Other functions
V/f free settings (7 points), Upper/lower limit frequency limiter, Frequency jump, Curve acceleration/deceleration,
Manual torque boost, Energy-saving operation, Analog output adjustment function, Minimum frequency, Carrier
frequency adjustment, Motor electronic thermal function (free setting is also possible), Inverter electronic thermal
function, External start/end (volume/ratio), Frequency input selection, Trip retry, Restart after instantaneous stop,
Output of signals, Initialization settings, PID control, Automatic deceleration at power shut-off, Brake control
function, Auto-tuning for commercial switching function (online/offline), and others described in "Chapter 12
Inverter Functions".
In
p
u
t
Frequency
setting
Standard operator keypad Parameter setting using arrow keys
External signals *6)
Ai1/Ai2 terminal (when changing voltage)
Setting through input of 0-
10VDC voltage (input impedance: 10kΩ)
Ai1/Ai2 terminal (when changing current)
Setting through input of 0-
20mA current (input impedance: 100Ω)
Ai3 terminal
Setting through input of -10-+10VDC voltage
(input impedance: 10kΩ)
Multistage speed terminal
(use of input terminal function)
15th speed
Pulse string input
(A/B terminal, use of input terminal function)
32kHz×2 at maximum
External port
Setting via RS485 serial communication (protocol: Modbus-RTU)
Normal
rotation/
reverse
rotation
Run/stop
Standard operator keypad
Execution with the RUN /STOP key
(normal rotation/reverse rotation can be switched by setting parameters)
External signals
Normal rotation operation (FW)/reverse rotation (RV) (when an input terminal function is assigned)
3-wire input available (when an input terminal function is assigned)
External port
Setting via RS485 serial communication (protocol: Modbus-RTU (maximum: 115.2kbps)
Input terminal function
11 terminals (input of pulse string is available on terminal A and B)
FW (Normal rotation)/RV (Reverse rotation), CF1-4(Multistage speed 1-4), SF1-7 (Multistage speed bit 1-7), ADD
(Addition of frequency), SCHG (Switching of frequency command), STA (3-wire start)/STP (3-wire stop)/F_R
(3-wire normal/reverse), AHD (Retention of analog command), FUP (Increase of speed via remote operation/FDN
(Deceleration via remote operation), UDC (Deletion of data via remote operation), F-OP (Forced command
switching), SET (Second control), RS (Reset), JG (Jogging), DB (External current braking), 2CH (2-stage
acceleration/deceleration), FRS (Free-run stop), EXT (External abnormality), USP (Prevention of restart after
restoration of power), CS (Commercial switching), SFT (Soft-lock), BOK (Brake check), OLR (Overload restriction
switching), KHC (Clearance of integrated input power), OKHC (Clearance of integrated output power), PID (PID1
disabled), PIDC (PID1 integration reset), PID2 (PID2 disabled), PIDC2 (PID2 integration reset), SVC1-4 (PID1
multistage target values 1-4), PRO (PID gain switching), PIO (PID output switching), SLEP (SLEEP condition
satisfied)/WAKE (WAKE condition satisfied), TL (Torque restriction enabled), TRQ1, 2 (Switching of torque limit
1,2), PPI (Switching of P/PI control), CAS (Switching of control gain), FOC (Preparatory excitation), ATR (Torque
control enabled), TBS (Torque bias enabled), LAC (Cancellation of acceleration/deceleration), Mi1-11
(General-purpose input 1-11), PCC (Clearance of pulse counter), ECOM (Start of EzCOM), PRG (Program run),
HLD (Acceleration/deceleration stop), REN (Operation permission signal), PLA (Pulse string input A, PLB (Pulse
string input B), and others described in "12.24.1 Using the input signal function externally"
Backup power supply terminal
P+/P-: DC24V input (allowable input voltage: 24V±10%)
STO input terminal
2 terminals (simultaneous input)
Thermistor input terminal
1 terminal (possible to switch between positive temperature coefficient/negative temperature coefficient
resistance element)
Summary of Contents for SJ Series
Page 39: ...5 4 Chapter 5 Included Items Memo ...
Page 55: ...6 16 Chapter 6 Installation Memo ...
Page 91: ...7 36 Chapter 7 Wire Connection and Optional Devices Memo ...
Page 135: ...9 40 Chapter 9 Operating Instructions Memo ...
Page 145: ...10 10 Chapter 10 Test Run Memo ...
Page 159: ...12 2 6 Chapter 12 Inverter Functions Memo ...
Page 169: ...12 3 10 Chapter 12 Inverter Functions Memo ...
Page 195: ...12 5 8 Chapter 12 Inverter Functions Memo ...
Page 217: ...12 8 12 Chapter 12 Inverter Function Memo ...
Page 287: ...12 10 32 Chapter 12 Inverter Functions Memo ...
Page 303: ...12 11 16 Chapter 12 Inverter Functions Memo ...
Page 349: ...12 15 8 Chapter 12 Inverter Function Memo ...
Page 395: ...12 17 34 Chapter 12 Inverter Functions Memo ...
Page 397: ...12 18 2 Chapter 12 Inverter Functions Memo ...
Page 415: ...12 19 18 Chapter 12 Inverter Function Memo ...
Page 581: ...15 10 Chapter 15 Optional Cassettes Memo ...
Page 591: ...16 10 Chapter 16 ProDriveNext EzSQ Memo ...
Page 642: ...18 49 Chapter 18 Tips FAQ Troubleshooting Memo ...
Page 650: ...19 8 Chapter 19 Maintenance and Inspection Memo ...
Page 781: ...Appendix 1 70 Appendix 1 List of Parameters Memo ...