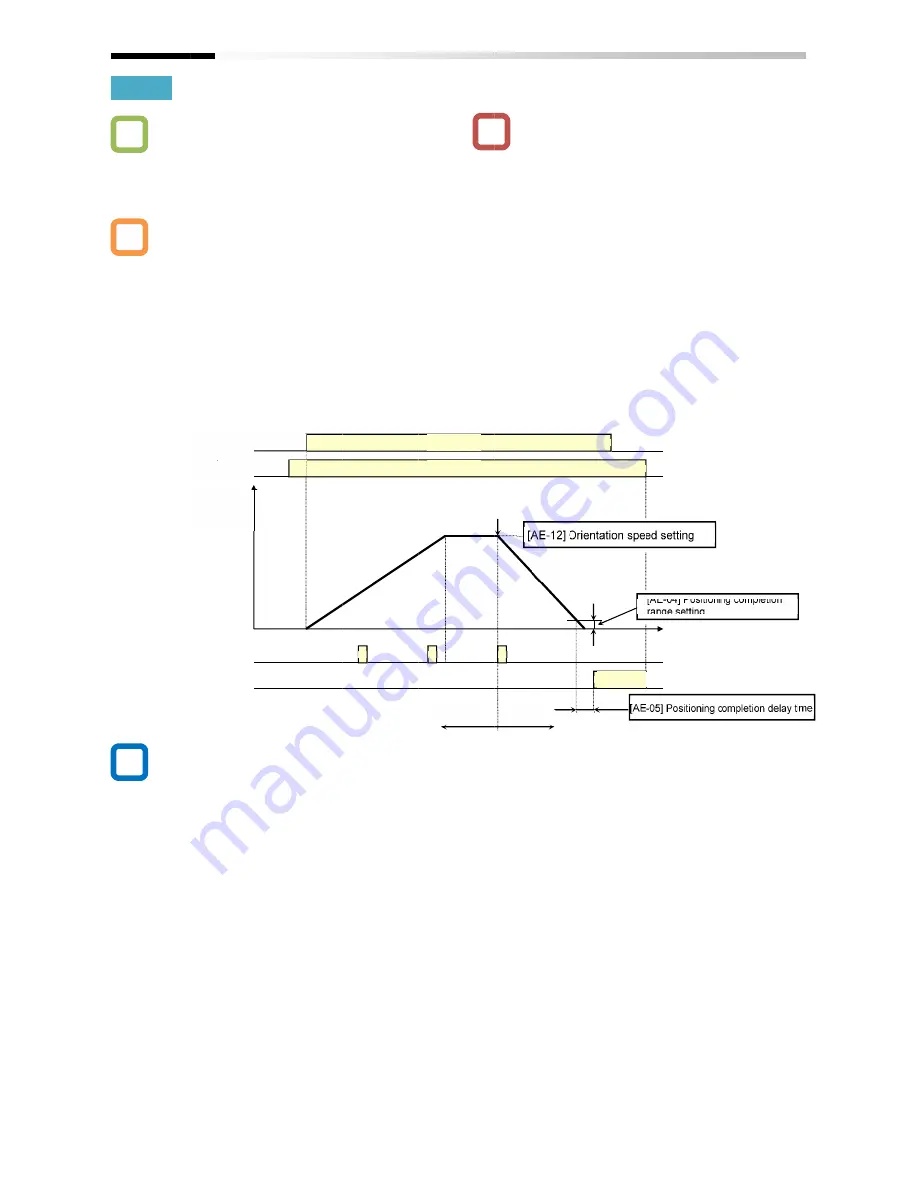
Chapter 12
12.
•
•
•
•
•
(1)
(2)
(3)
Chapter 12
12.17.8
Stopping at Designated Position
• How to stop the system at the designated position
for the maintenance of a machine tool.
• How to use the orientation function.
• The orientation control is available for the pulse
train position control.
• Used with the [AA121] control method set to 10:
vector control with sensor and
control mode set to 00: speed torque control mode
or 01: pulse train position control mode.
• This function enables you to determine the position
at any point within one rotation of the motor. This
can be used for replacing the main axis of a
machine tool, etc.
(1) When the operation command is turned on while
the [ORT] terminal is on, there is an acceleration
until the [AE
speed is entered.
(During the operation, the speed is shifted to the
orientation speed as soon as the ORT t
tuned on.)
(2) After the orientation speed is reached, there is a
shift to the position control when the first Z pulse is
detected.
(3) The position control is operated at the [AE
orientation stop po one rotation for the
forward rotation and the [AE
po two rotations for the reverse rotation as
a target value.
The larger the [AE
shorter the deceleration time becomes.
(The deceleration time setting is not followed.)
Q
A
Operation command
(FW/RV)
Z pulse terminal
Output
frequency
Chapter 12
Stopping at Designated Position
stop the system at the designated position
for the maintenance of a machine tool.
How to use the orientation function.
The orientation control is available for the pulse
train position control.
Used with the [AA121] control method set to 10:
vector control with sensor and
control mode set to 00: speed torque control mode
or 01: pulse train position control mode.
This function enables you to determine the position
at any point within one rotation of the motor. This
sed for replacing the main axis of a
machine tool, etc.
When the operation command is turned on while
the [ORT] terminal is on, there is an acceleration
until the [AE-12] orientation speed and a constant
speed is entered.
(During the operation, the speed is shifted to the
orientation speed as soon as the ORT t
tuned on.)
After the orientation speed is reached, there is a
shift to the position control when the first Z pulse is
The position control is operated at the [AE
orientation stop po one rotation for the
forward rotation and the [AE
po two rotations for the reverse rotation as
a target value.
The larger the [AE-07] position loop ga
shorter the deceleration time becomes.
(The deceleration time setting is not followed.)
Operation command
(FW/RV)
ORT terminal
Z pulse terminal
Output
frequency
POK signal
Stopping at Designated Position
stop the system at the designated position
for the maintenance of a machine tool.
How to use the orientation function.
The orientation control is available for the pulse
Used with the [AA121] control method set to 10:
vector control with sensor and the [AA123] vector
control mode set to 00: speed torque control mode
or 01: pulse train position control mode.
This function enables you to determine the position
at any point within one rotation of the motor. This
sed for replacing the main axis of a
When the operation command is turned on while
the [ORT] terminal is on, there is an acceleration
12] orientation speed and a constant
(During the operation, the speed is shifted to the
orientation speed as soon as the ORT t
After the orientation speed is reached, there is a
shift to the position control when the first Z pulse is
The position control is operated at the [AE
orientation stop po one rotation for the
forward rotation and the [AE-11] orientation stop
po two rotations for the reverse rotation as
07] position loop ga
shorter the deceleration time becomes.
(The deceleration time setting is not followed.)
Operation command
ORT terminal
Z pulse terminal
12
Stopping at Designated Position
stop the system at the designated position
for the maintenance of a machine tool.
How to use the orientation function.
The orientation control is available for the pulse
Used with the [AA121] control method set to 10:
the [AA123] vector
control mode set to 00: speed torque control mode
or 01: pulse train position control mode.
This function enables you to determine the position
at any point within one rotation of the motor. This
sed for replacing the main axis of a
When the operation command is turned on while
the [ORT] terminal is on, there is an acceleration
12] orientation speed and a constant
(During the operation, the speed is shifted to the
orientation speed as soon as the ORT terminal is
After the orientation speed is reached, there is a
shift to the position control when the first Z pulse is
The position control is operated at the [AE-11]
orientation stop po one rotation for the
11] orientation stop
po two rotations for the reverse rotation as
07] position loop gain is, the
shorter the deceleration time becomes.
(The deceleration time setting is not followed.)
Speed control
12-17-22
stop the system at the designated position
The orientation control is available for the pulse
Used with the [AA121] control method set to 10:
the [AA123] vector
control mode set to 00: speed torque control mode
This function enables you to determine the position
at any point within one rotation of the motor. This
When the operation command is turned on while
the [ORT] terminal is on, there is an acceleration
12] orientation speed and a constant
(During the operation, the speed is shifted to the
erminal is
After the orientation speed is reached, there is a
shift to the position control when the first Z pulse is
11]
orientation stop po one rotation for the
11] orientation stop
po two rotations for the reverse rotation as
in is, the
(The deceleration time setting is not followed.)
• For using this function, it is required to set the
[AA121] control method to 10: vector control with
sensor and use the encoder feedback.
• See
• The Z pulse (one rotation position signal) is used as
the reference signal for the positioning.
(1) When the encoder is connected to the P1
option:
(2) When the encoder is connected to
circuit terminal block:
(4) When the [AE
time passes after the remaining number of pulses
enters the [AE
setti
(The output continues until the ORT termin
turned off.)
After the positioning completes, the servo lock
status continues until the operation command is
turned off.
!
ON
ON
Speed control
(1)
(2)
22
For using this function, it is required to set the
[AA121] control method to 10: vector control with
sensor and use the encoder feedback.
See also "12.9.17 Using Encoder".
The Z pulse (one rotation position signal) is used as
the reference signal for the positioning.
When the encoder is connected to the P1
option:
Input the Z pulse between
When the encoder is connected to
circuit terminal block:
Assign the input terminal function 109:PLZ to any
of the input terminal
When the [AE
time passes after the remaining number of pulses
enters the [AE
setting, the [POK] signal is output.
(The output continues until the ORT termin
turned off.)
After the positioning completes, the servo lock
status continues until the operation command is
turned off.
[AE-12] Orientation speed setting
Position control
(2)
(3)
For using this function, it is required to set the
[AA121] control method to 10: vector control with
sensor and use the encoder feedback.
also "12.9.17 Using Encoder".
The Z pulse (one rotation position signal) is used as
the reference signal for the positioning.
When the encoder is connected to the P1
Input the Z pulse between
When the encoder is connected to
circuit terminal block:
Assign the input terminal function 109:PLZ to any
of the input terminal and input the Z pulse.
When the [AE-05] positioning completion delay
time passes after the remaining number of pulses
enters the [AE-04] positioning completion range
ng, the [POK] signal is output.
(The output continues until the ORT termin
After the positioning completes, the servo lock
status continues until the operation command is
12] Orientation speed setting
ON
[AE-
Position control
Inverter Functions
For using this function, it is required to set the
[AA121] control method to 10: vector control with
sensor and use the encoder feedback.
also "12.9.17 Using Encoder".
The Z pulse (one rotation position signal) is used as
the reference signal for the positioning.
When the encoder is connected to the P1
Input the Z pulse between EZP-EZN.
When the encoder is connected to the control
Assign the input terminal function 109:PLZ to any
and input the Z pulse.
05] positioning completion delay
time passes after the remaining number of pulses
04] positioning completion range
ng, the [POK] signal is output.
(The output continues until the ORT termin
After the positioning completes, the servo lock
status continues until the operation command is
12] Orientation speed setting
[AE-04] Positioning completion
range setting
[AE-05] Positioning completion delay time
(4)
Inverter Functions
For using this function, it is required to set the
[AA121] control method to 10: vector control with
sensor and use the encoder feedback.
The Z pulse (one rotation position signal) is used as
the reference signal for the positioning.
When the encoder is connected to the P1-FB
.
the control
Assign the input terminal function 109:PLZ to any
and input the Z pulse.
05] positioning completion delay
time passes after the remaining number of pulses
04] positioning completion range
(The output continues until the ORT terminal is
After the positioning completes, the servo lock
status continues until the operation command is
04] Positioning completion
05] Positioning completion delay time
Inverter Functions
The Z pulse (one rotation position signal) is used as
Assign the input terminal function 109:PLZ to any
time passes after the remaining number of pulses
05] Positioning completion delay time
Summary of Contents for SJ Series
Page 39: ...5 4 Chapter 5 Included Items Memo ...
Page 55: ...6 16 Chapter 6 Installation Memo ...
Page 91: ...7 36 Chapter 7 Wire Connection and Optional Devices Memo ...
Page 135: ...9 40 Chapter 9 Operating Instructions Memo ...
Page 145: ...10 10 Chapter 10 Test Run Memo ...
Page 159: ...12 2 6 Chapter 12 Inverter Functions Memo ...
Page 169: ...12 3 10 Chapter 12 Inverter Functions Memo ...
Page 195: ...12 5 8 Chapter 12 Inverter Functions Memo ...
Page 217: ...12 8 12 Chapter 12 Inverter Function Memo ...
Page 287: ...12 10 32 Chapter 12 Inverter Functions Memo ...
Page 303: ...12 11 16 Chapter 12 Inverter Functions Memo ...
Page 349: ...12 15 8 Chapter 12 Inverter Function Memo ...
Page 395: ...12 17 34 Chapter 12 Inverter Functions Memo ...
Page 397: ...12 18 2 Chapter 12 Inverter Functions Memo ...
Page 415: ...12 19 18 Chapter 12 Inverter Function Memo ...
Page 581: ...15 10 Chapter 15 Optional Cassettes Memo ...
Page 591: ...16 10 Chapter 16 ProDriveNext EzSQ Memo ...
Page 642: ...18 49 Chapter 18 Tips FAQ Troubleshooting Memo ...
Page 650: ...19 8 Chapter 19 Maintenance and Inspection Memo ...
Page 781: ...Appendix 1 70 Appendix 1 List of Parameters Memo ...