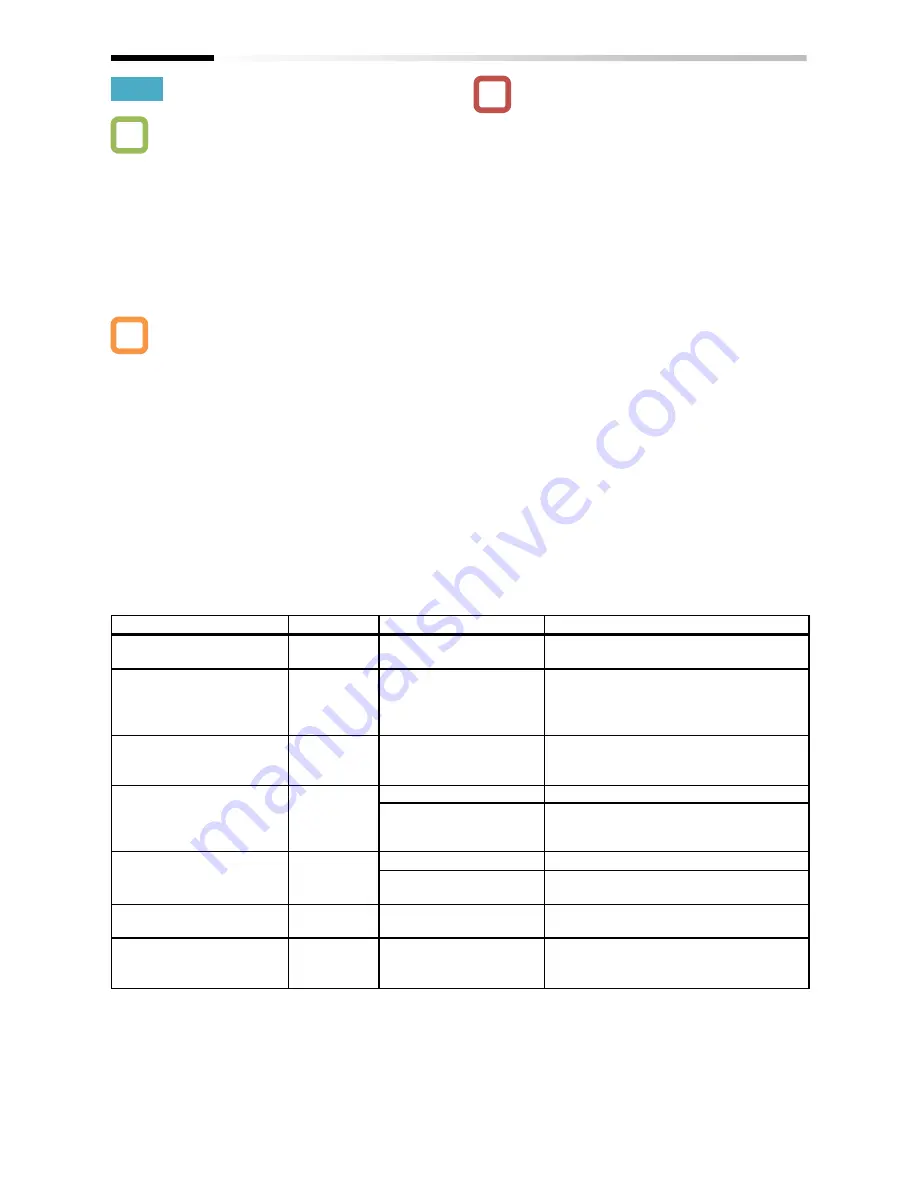
12-9-12
Chapter 12
Inverter Function
12.9.9
Use sensorless vector control
• The motor has a slow response of frequency.
• More torque is needed.
• To use in applications that require a high torque at
the start.
• To control the frequency accurately.
• A heavy load slows the motor revolution relative to
what the frequency command dictates.
• Automatically adjust the frequency and the output
voltage so as to achieve responsively a higher
torque even at slow speeds.
• In the sensorless vector control, to control the
motor, the frequency and the output voltage are
corrected and the response is adjusted with
respect to the load inertia.
• Even in the case of Hitachi's standard motors, a
large load inertia and/or a long wiring may require
the auto-tuning.
• Use of other motors than Hitachi's standard motors
requires the setting-up of the motor constant and
the load inertia by, for example conducting the
auto-tuning.
Parameter
• In the sensorless vector control, set appropriately
the motor capacity, the number of motor poles, the
base frequency, the rated voltage, and the rated
current in order to conduct motor control.
• When the motor performs below its potential
characteristics, conduct the auto-tuning and make
adjustment by referring to the next section.
• In the case of a long wiring (approximately longer
than 20 m) and in the case of controlling motors
other than out company's, the performance may be
below what are expected from the characteristics.
• As the capacity becomes farther away from the
maximum applicable motor capacity, sufficient
operation characteristics becomes more difficult to
get.
• In the sensorless vector control, adjustment of the
response is possible. The sensorless vector control
can be used in applications that require a better
follow-up performance of the frequency to the
command.
• When a motor is hunting and vibrating, an
adjustment of the speed response [HA115] may
improve the state of the motor.
• To limit the output direction by enabling the reversal
prevention function [HC114].
• To correct the slip change caused by temperature
changes by enabling the selection of the secondary
resistance correction [HC113]. Connection is
needed between a thermistor for measuring the
temperature of the motor and the TH terminal.
Item
Parameter
Data
Description
Control mode
[AA121]
08
To use the sensorless vector control
(IM).
Speed response
[HA115]
0~1000(%)
To adjust the responsiveness of the
control.
A larger value enhances the
responsiveness.
Amount of boost at the
start(sensorless vector)
[HC111]
0~50(%)
To adjust the current command at the
start when the starting torque is not
sufficient.
Selection of whether a
secondary-resistance
correction is to be
conducted.
[HC113]
00
Disabled
01
Enabled Requiring a temperature
thermistor.
Selection of reversal
prevention
[HC114]
00
Disabled
01
Enabled Limit the output to prevent the
output in the reverse direction.
Time constant for torque
current command filter
[HC120]
0~100(ms)
To adjust the filter for the torque
current.
Speed feed forward
compensation adjustment
gain
[HC121]
0~1000(%)
To adjust the feed forward control of the
speed controller.
Q
A
!
Summary of Contents for SJ Series
Page 39: ...5 4 Chapter 5 Included Items Memo ...
Page 55: ...6 16 Chapter 6 Installation Memo ...
Page 91: ...7 36 Chapter 7 Wire Connection and Optional Devices Memo ...
Page 135: ...9 40 Chapter 9 Operating Instructions Memo ...
Page 145: ...10 10 Chapter 10 Test Run Memo ...
Page 159: ...12 2 6 Chapter 12 Inverter Functions Memo ...
Page 169: ...12 3 10 Chapter 12 Inverter Functions Memo ...
Page 195: ...12 5 8 Chapter 12 Inverter Functions Memo ...
Page 217: ...12 8 12 Chapter 12 Inverter Function Memo ...
Page 287: ...12 10 32 Chapter 12 Inverter Functions Memo ...
Page 303: ...12 11 16 Chapter 12 Inverter Functions Memo ...
Page 349: ...12 15 8 Chapter 12 Inverter Function Memo ...
Page 395: ...12 17 34 Chapter 12 Inverter Functions Memo ...
Page 397: ...12 18 2 Chapter 12 Inverter Functions Memo ...
Page 415: ...12 19 18 Chapter 12 Inverter Function Memo ...
Page 581: ...15 10 Chapter 15 Optional Cassettes Memo ...
Page 591: ...16 10 Chapter 16 ProDriveNext EzSQ Memo ...
Page 642: ...18 49 Chapter 18 Tips FAQ Troubleshooting Memo ...
Page 650: ...19 8 Chapter 19 Maintenance and Inspection Memo ...
Page 781: ...Appendix 1 70 Appendix 1 List of Parameters Memo ...