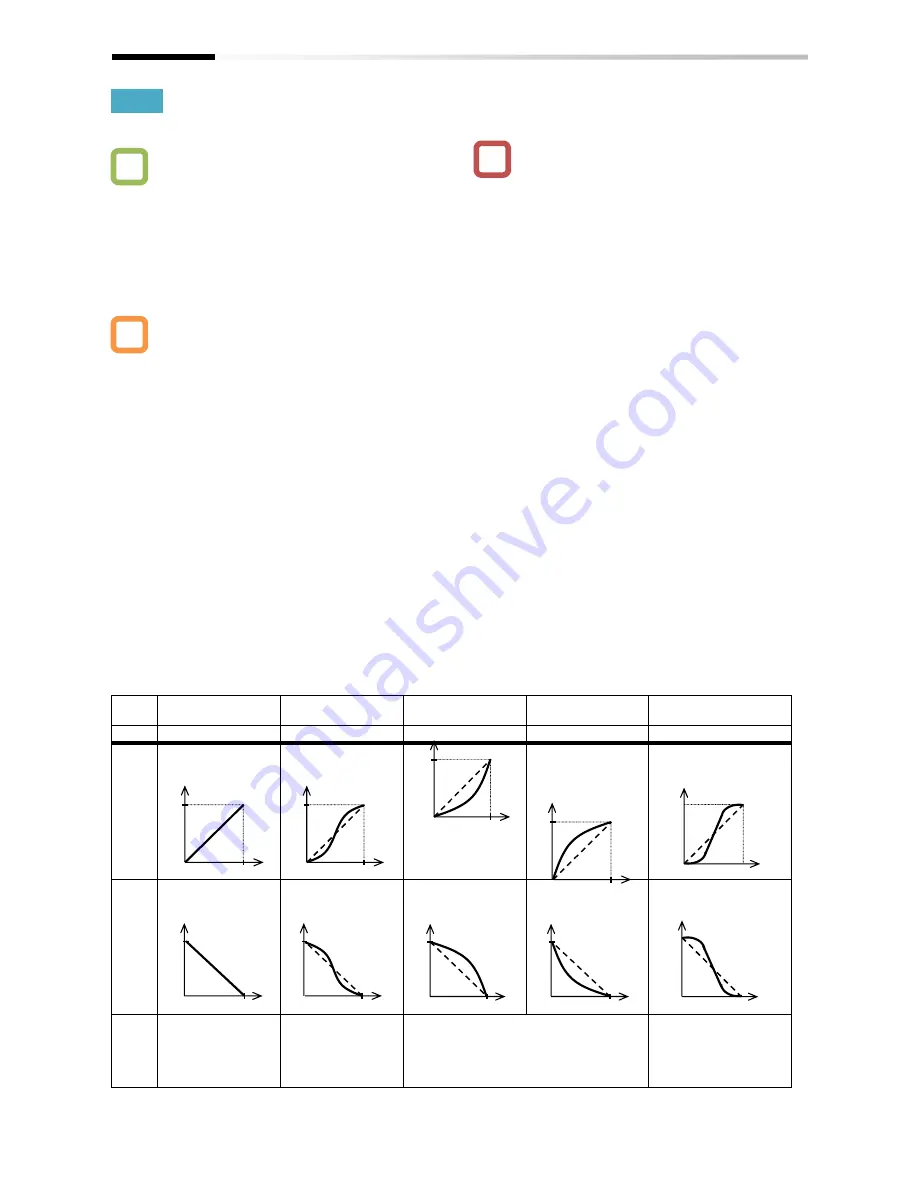
12-8-9
Chapter 12
Inverter Function
12.8.5
Change the acceleration or
deceleration pattern
• To reduce such a large shock caused by an abrupt
movement that will collapse the load being
transported in lifts or on conveyors.
• To reduce the shock when the motor starts moving
and when it is about to stop moving.
• To change the acceleration gradient in accordance
with the winding or feeding amount.
• Setting a(n) acceleration or deceleration pattern is
possible that suit each system.
• Setting the acceleration pattern selection and the
deceleration pattern selection can be done
independently of each other by means of [AC-03]
and [AC-04], respectively.
• To use a(n) acceleration or deceleration pattern
other than the linear one (00), a stable operation
can be achieved by an command that can fix the
target of the frequency command by means of the
operator-keypad command and/or the multi-speed
command.
• Even if a(n) acceleration or deceleration pattern is
set, the acceleration time should be set at the time
that it takes to rise from 0 Hz to the maximum
frequency and the deceleration time should be set
at the time it takes to fall from the maximum
frequency to 0 Hz.
• Changing the acceleration or deceleration pattern
from one to another will create a sector with a(n)
acceleration or deceleration time having a steep
gradient. If the occurrence of an over current/over
voltage is predictable, it will be prevented by
adjusting from happening, the acceleration or
deceleration time has to be adjusted to prevent
such an occurrence.
• When any other acceleration or deceleration
pattern than the linear one (00) is set, a change of
command value during the acceleration or
deceleration may cause a recalculation of the
acceleration or deceleration pattern, which may
result in a shock.
• When any other acceleration or deceleration pattern
than the linear one (00) is set, use any other
command than the analog input one. An unsteady
command value may cause a recalculation of the
acceleration or deceleration pattern, which may
prolong the actual acceleration or deceleration
time.
Pattern selection
Select a pattern for each of the acceleration and the deceleration patterns by referring to the following table.
Set
value
00
01
02
03
04
Curve
Linear
S-shaped
U-shaped
Inverse-U- shaped
EL-S-shaped
[AC-03]
(Accele
ration)
[AC-04]
(Decele
ration)
Descrip
tion
Providing a linear
acceleration up or
deceleration down to
the set frequency
value.
Effective in the
prevention of load
collapse in lifts or on
conveyors, for
example.
Effective when a winder or the like needs to
control of the tension and/or prevent the
object to be wound from being cut. Usable
for 1-shot winding/feeding.
Providing a shockless
start/stop as in the case
of the S-shaped curve,
but providing a linear
middle sector.
Q
A
!
Time
O
u
tp
u
t
fr
e
q
u
e
n
cy
Time
O
u
tp
u
t
fr
e
q
u
e
n
cy
Time
O
u
tp
u
t
fr
e
q
u
e
n
cy
Time
O
u
tp
u
t
fr
e
q
u
e
n
cy
Time
O
u
tp
u
t
fr
e
q
u
e
n
cy
Time
O
u
tp
u
t
fr
e
q
u
e
n
cy
Time
O
u
tp
u
t
fr
e
q
u
e
n
cy
Time
O
u
tp
u
t
fr
e
q
u
e
n
cy
Time
O
u
tp
u
t
fr
e
q
u
e
n
cy
O
u
tp
u
t
fr
e
q
u
e
n
cy
Time
Summary of Contents for SJ Series
Page 39: ...5 4 Chapter 5 Included Items Memo ...
Page 55: ...6 16 Chapter 6 Installation Memo ...
Page 91: ...7 36 Chapter 7 Wire Connection and Optional Devices Memo ...
Page 135: ...9 40 Chapter 9 Operating Instructions Memo ...
Page 145: ...10 10 Chapter 10 Test Run Memo ...
Page 159: ...12 2 6 Chapter 12 Inverter Functions Memo ...
Page 169: ...12 3 10 Chapter 12 Inverter Functions Memo ...
Page 195: ...12 5 8 Chapter 12 Inverter Functions Memo ...
Page 217: ...12 8 12 Chapter 12 Inverter Function Memo ...
Page 287: ...12 10 32 Chapter 12 Inverter Functions Memo ...
Page 303: ...12 11 16 Chapter 12 Inverter Functions Memo ...
Page 349: ...12 15 8 Chapter 12 Inverter Function Memo ...
Page 395: ...12 17 34 Chapter 12 Inverter Functions Memo ...
Page 397: ...12 18 2 Chapter 12 Inverter Functions Memo ...
Page 415: ...12 19 18 Chapter 12 Inverter Function Memo ...
Page 581: ...15 10 Chapter 15 Optional Cassettes Memo ...
Page 591: ...16 10 Chapter 16 ProDriveNext EzSQ Memo ...
Page 642: ...18 49 Chapter 18 Tips FAQ Troubleshooting Memo ...
Page 650: ...19 8 Chapter 19 Maintenance and Inspection Memo ...
Page 781: ...Appendix 1 70 Appendix 1 List of Parameters Memo ...