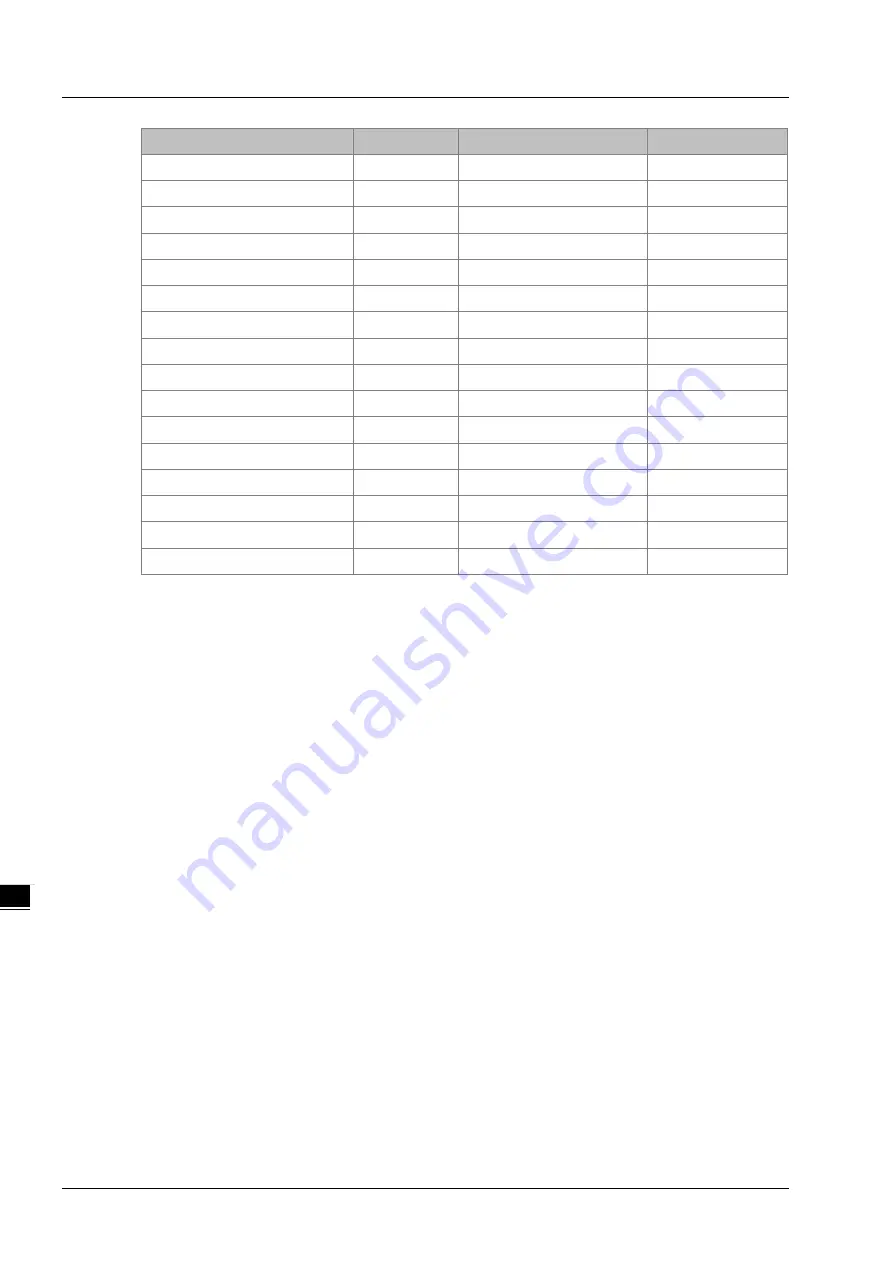
DVP-15MC Series Motion Controller Operation Manual
8-204
_8
Variable name
Address
Data type
Initial value
Config1_Done
BOOL
Config1_Err
BOOL
Config1_ErrID
WORD
ETH_Link_Manage1
ETH_Link_Manage
MA1_En
BOOL
MA1_Open
BOOL
MA1_Valid
BOOL
MA1_LinkOpen
BOOL
MA1_PhyErr
BOOL
ETH_Link_Status1
ETH_Link_Status
STA1_En
BOOL
STA1_ Valid
BOOL
STA1_ETH_Err
BOOL
STA1_ETH_ErrID
WORD
STA1_Err
BOOL
STA1_ErrID
WORD
Summary of Contents for DVP-15MC Series
Page 19: ...DVP 15MC Series Motion Controller Operation Manual 1 4 _1 MEMO...
Page 23: ...DVP 15MC Series Operation Manual 2 4 _2 MEMO...
Page 31: ...DVP 15MC Series Motion Controller Operation Manual 3 8 _3 MEMO...
Page 75: ...DVP 15MC Series Motion Controller Operation Manual 6 26 _6 MEMO...
Page 87: ...DVP 15MC Series Motion Controller Operation Manual 7 12 _7 MEMO...
Page 432: ...Chapter 8 Logic Instructions 8 345 8_ MEMO...
Page 470: ...DVP 15MC Series Motion Controller Operation Manual 10 34 10 MEMO...
Page 878: ...DVP 15MC Series Motion Controller Operation Manual 11 408 11 1 MEMO...
Page 920: ...DVP 15MC Series Motion Controller Operation Manual A 16 A MEMO...
Page 941: ...D 1 D Explanation of Homing Modes Table of Contents D 1 Explanation of Homing Modes D 2...
Page 966: ...DVP 15MC Series Motion Controller Operation Manual D 26 D MEMO...