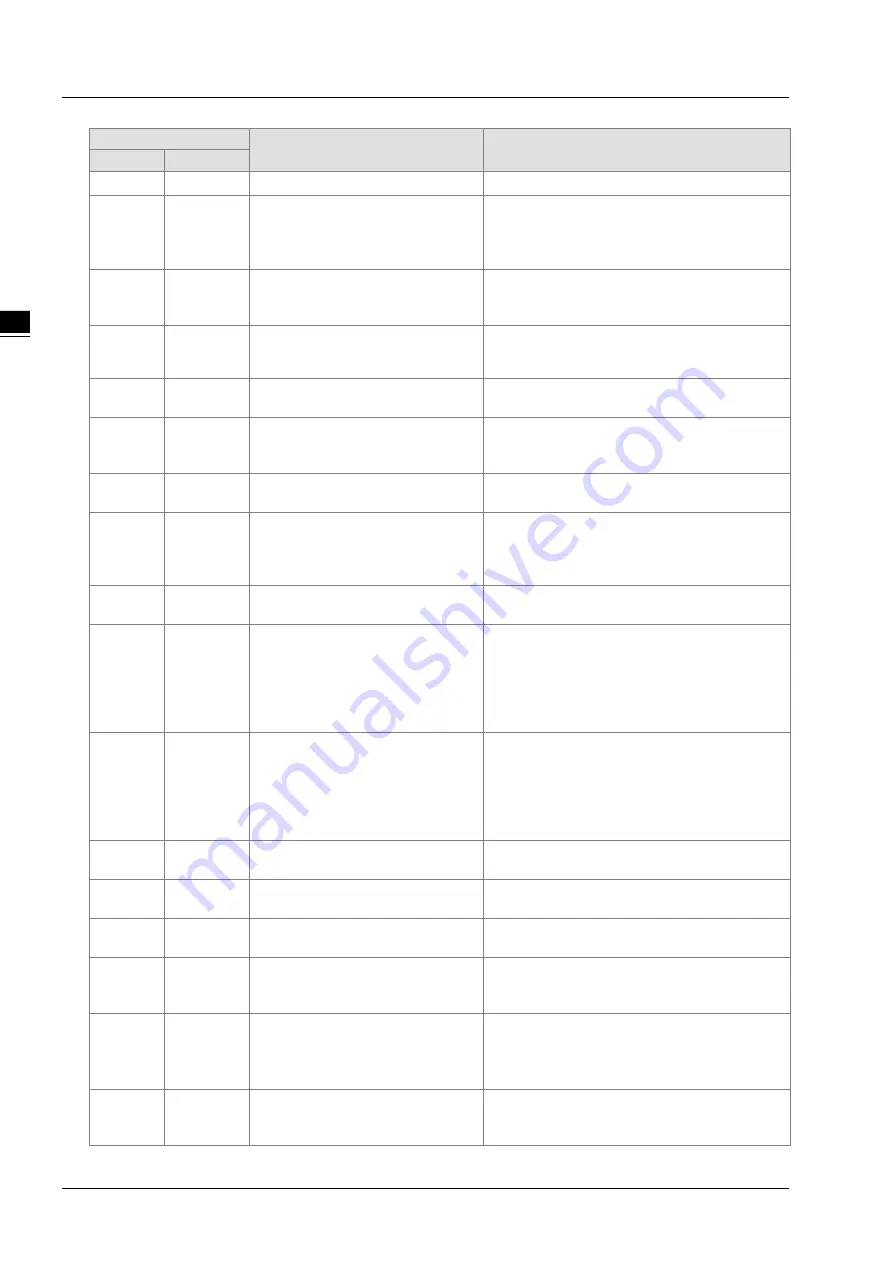
DVP-15MC Series Motion Controller Operation Manual
12-10
12
1
ErrorID
Meaning
How to deal with
Hex
Decimal
be greater than 0.
1024
4132
The value of SyncStartPos is
incorrect.
Modify the value of the input variable,
SyncStartPos
of APF_RotaryCut_Init. It
should be between 0 and the cutting length.
1025
4133
The value of SyncStopPos is
incorrect.
Modify the value of the input variable,
SyncStopPos
of APF_RotaryCut_Init. It
should be between 0 and the cutting length.
1026
4134
The settings of SyncStopPos
and SyncStartPos are incorrect.
The value of the input variable,
SyncStopPos
should be less than that of
SyncStartPos of the instruction.
1027
4135
The value of RotCutID is
incorrect.
The value of the input variable,
RotCutID
should be in the range of 1~8.
1028
4136
The value of RotaryAxisKnifeNum
is incorrect.
The value of the input variable,
RotaryAxisKnifeNum
should be in the range
of 1~16.
1029
4137
The inner state of rotary cut is
illegal.
Modify the parameter values for initializing
rotary cut.
103A
4154
Rotary cut initializing fails.
Since APF_RotaryCut_Init has not been
executed, please execute
APF_RotaryCut_Init first and then execute
APF_RotaryCut_In.
103B
4155
The axis is offline and the capture
function can not be performed
Execute the capture instruction after the axis
is connected normally.
103C
4156
The value of
MasterOffset
of
MC_CamIn is greater than the
master axis cam cycle range.
Modify the value of
MasterOffset
into that
between the negative number and positive
number of the master axis cam cycle range.
(The master axis cam cycle range=
Maximum master axis cam cycle- Mimimum
master axis cam cycle)
103D
4157
The value of
SlaveOffset
of
MC_CamIn is greater than the
slave axis cam cycle range.
Modify the value of
SlaveOffset
into that
between the negative number and positive
number of the slave axis cam cycle range.
(The slave axis cam cycle range= Maximum
slave axis cam cycle- Minimum slave axis
cam cycle)
103E
4158
The
Depth
value of the instruction
is out of the range.
Modify the value of the input
Depth
in order
not to exceed the range.
103F
4159
The
VelOverride
value range of
the instruction is illegal.
Modify the value of the input
VelOverride
in
order not to exceed the range.
1040
4160
The file code is illegal.
Modify the value of the input
NCFile
into a
proper code value.
1041
4161
DMC_SetTorque is executed
when the axis is not in Standstill
state.
Make sure that DMC_SetTorque is executed
when the axis is in Standstill state.
1042
4162
The execution of MC_Reset fails.
1. Check if the axis specified by MC_Reset
exists.
2. MC_Reset is executed after the servo
alarm is cleared.
1043
4163
The execution of an instruction
leads to the result that the axis
position exceeds the range set in
Modify the instruction to make sure that the
final position does not exceed the software
limit range.
Summary of Contents for DVP-15MC Series
Page 19: ...DVP 15MC Series Motion Controller Operation Manual 1 4 _1 MEMO...
Page 23: ...DVP 15MC Series Operation Manual 2 4 _2 MEMO...
Page 31: ...DVP 15MC Series Motion Controller Operation Manual 3 8 _3 MEMO...
Page 75: ...DVP 15MC Series Motion Controller Operation Manual 6 26 _6 MEMO...
Page 87: ...DVP 15MC Series Motion Controller Operation Manual 7 12 _7 MEMO...
Page 432: ...Chapter 8 Logic Instructions 8 345 8_ MEMO...
Page 470: ...DVP 15MC Series Motion Controller Operation Manual 10 34 10 MEMO...
Page 878: ...DVP 15MC Series Motion Controller Operation Manual 11 408 11 1 MEMO...
Page 920: ...DVP 15MC Series Motion Controller Operation Manual A 16 A MEMO...
Page 941: ...D 1 D Explanation of Homing Modes Table of Contents D 1 Explanation of Homing Modes D 2...
Page 966: ...DVP 15MC Series Motion Controller Operation Manual D 26 D MEMO...