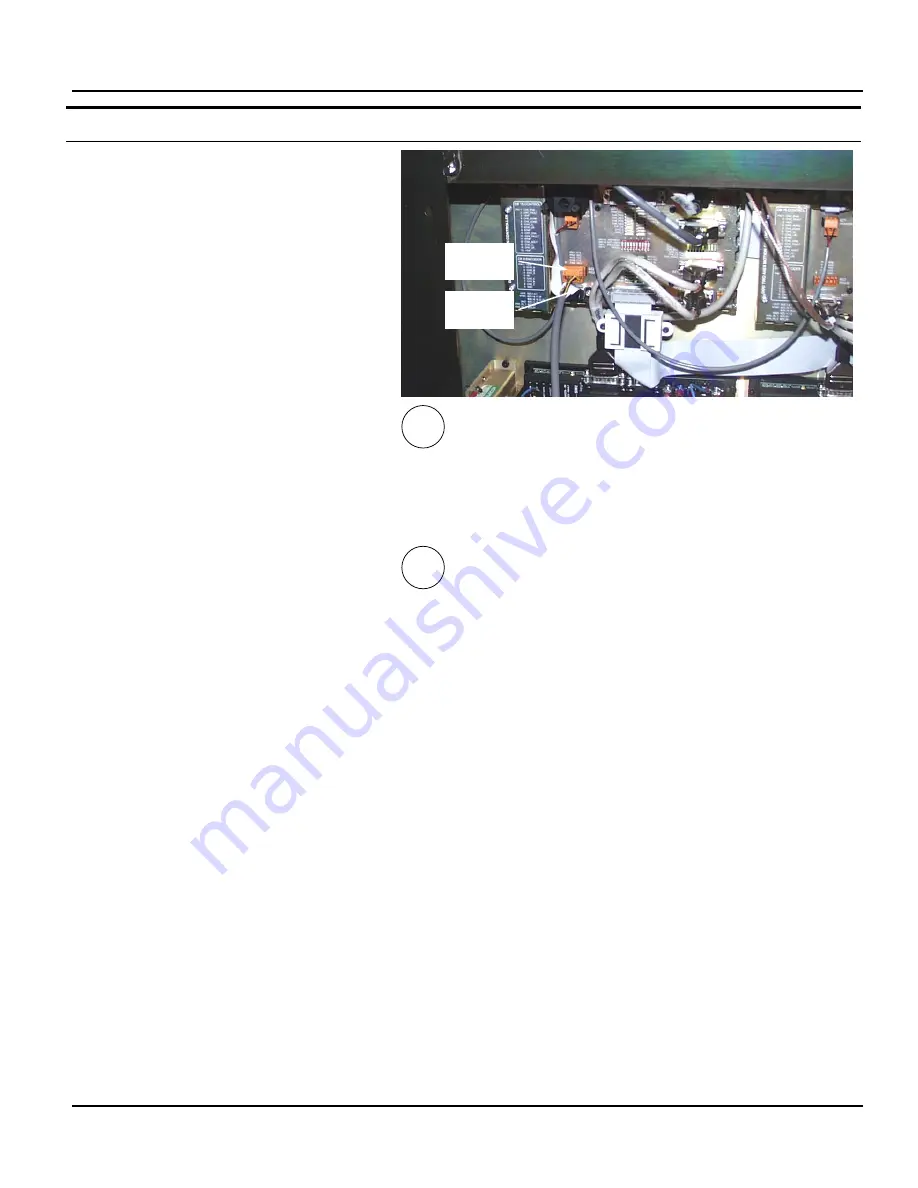
Software Update Procedures
1MAN0158-H11 04-2005 CSIP Level 1
CardioMD Service Manual
7-15
Procedure Details
3.
Connect the SW load cable to the motion
controller serial port labeled BZ2 RS232.
This does not require that any existing cables
be removed.
If you are using a laptop acquisition PC:
4.
Use the USB to RS 232 adapter to connect
the opposite end of the SW load cable to
one of the acquisition PC’s USB ports.
See section 7.2.2, page 7-2 for instructions on
determining which COM port you are using.
If you are using a tower acquisition PC:
5.
Connect the opposite end of the cable to
the acquisition PC’s COM1 serial port.
Note
. Downloading software to the motion
controller does not require the use of a NULL
modem cable.
6.
Disconnect the CANbus cable between the
two motion controllers by unplugging the
cable connected to CAN_IN on the slave
motion controller (controller to the left).
7.
Insert the software installation CD in the
CD-ROM drive.
To download software to the motion control-
ler, you must start the Flash program. Proceed
as follows:
8.
In the Windows Explorer, select the folder
MC
on the CD-ROM.
9.
In this folder, double-click the icon
flash.exe
to start the Flash program.
III
I, II
Software
load cable
CANbus
cable
Summary of Contents for CARDIOMD
Page 1: ...CARDIOMD SERVICE MANUAL 1MAN0158 H11 04 2005 CSIP Level 1 ...
Page 10: ...Introduction x CardioMD Service Manual 1MAN0158 H11 04 2005 CSIP Level 1 ...
Page 16: ...Safe Operating Practices 1 6 CardioMD Service Manual 1MAN0158 H11 04 2005 CSIP Level 1 ...
Page 164: ...Detector Calibration Files 5 60 CardioMD Service Manual 1MAN0158 H11 04 2005 CSIP Level 1 ...
Page 328: ...Installation Procedures 9 38 CardioMD Service Manual 1MAN0158 H11 04 2005 CSIP Level 1 ...
Page 348: ...Planned Maintenance Procedures 11 6 CardioMD Service Manual 1MAN0158 H11 04 2005 CSIP Level 1 ...
Page 465: ......