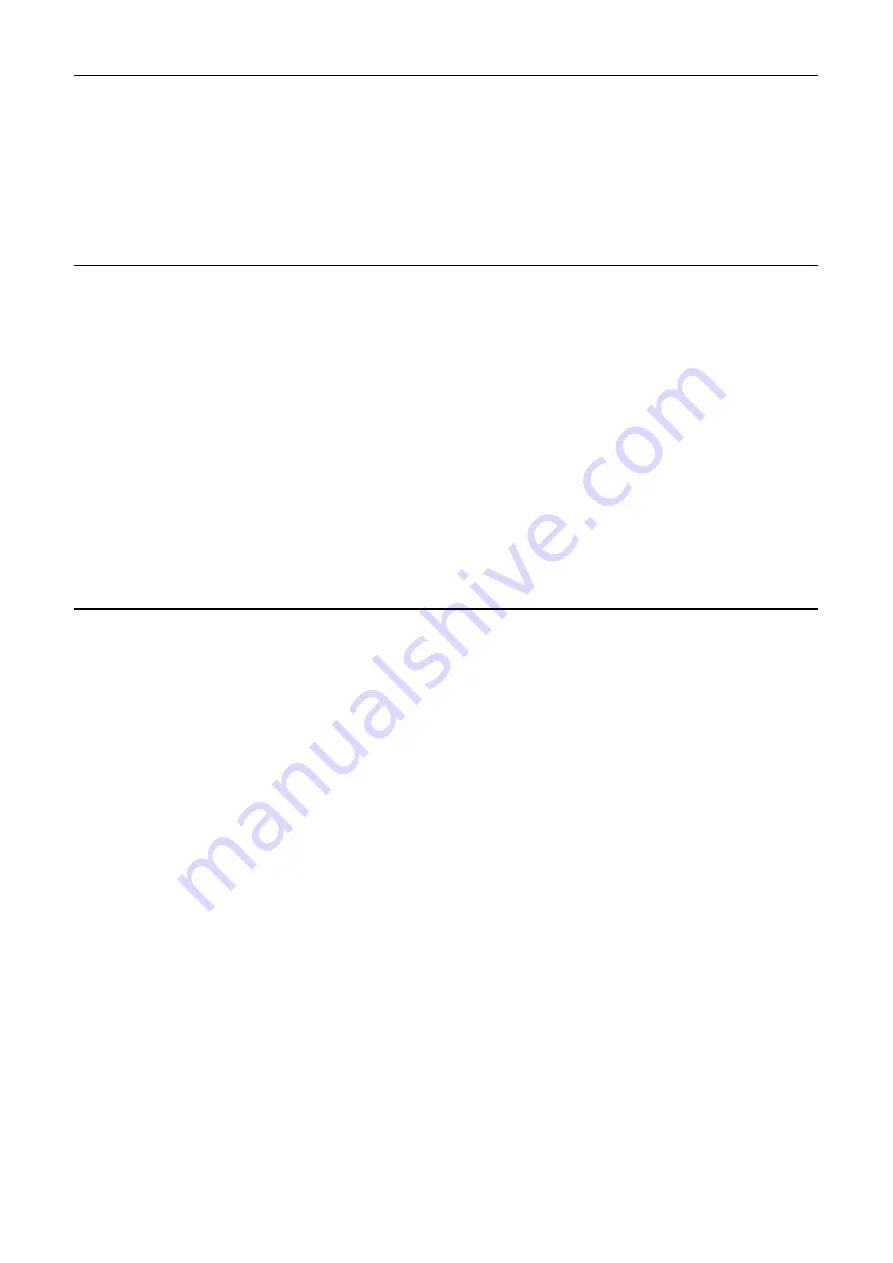
SINAMICS G120 CU250S-2 Control Units
List Manual, 09/2017, A5E33842890
587
2 Parameters
2.2 List of parameters
Notice:
This parameter is overwritten by the copy function of the safety functions integrated in the drive.
Note:
Rounding effects can occur in the last decimal place of the parameterized time.
The debounce time is rounded to whole milliseconds. It specifies the maximum duration of a fault pulse at the fail-
safe digital inputs with no reaction/influence on the selection or deselection of the Safety Basic Functions.
Example:
Debounce time = 1 ms: Fault pulses of 1 ms are filtered; only pulses longer than 2 ms are processed.
Debounce time = 3 ms: Fault pulses of 3 ms are filtered; only pulses longer than 4 ms are processed.
Description:
Sets the delay time of the pulse suppression for the "Safe Stop 1" (SS1) function on processor 2 to brake along the
OFF3 down ramp (p1135).
Recommendation:
In order that the drive can completely ramp-down along the OFF3 ramp and a motor holding brake that is possibly
available can close, then the delay time should be set as follows:
Motor holding brake parameterized: delay time >= p1135 + p1228 + p1217
Motor holding brake not parameterized: delay time >= p1135 + p1228
Dependency:
Refer to: p1135, p9652
Notice:
This parameter is overwritten by the copy function of the safety functions integrated in the drive.
Note:
For a data cross-check between p9652 and p9852, a difference of one Safety monitoring clock cycle is tolerated.
Rounding effects can occur in the last decimal place of the parameterized time.
The set time is rounded internally to an integer multiple of the monitoring clock cycle.
SS1: Safe Stop 1 (corresponds to Stop Category 1 acc. to EN60204)
Description:
Displays the supported Safety Integrated monitoring functions.
Processor 2 determines this display.
Dependency:
Refer to: r9771
Note:
SBC: Safe Brake Control
SDI: Safe Direction (safe motion direction)
SI: Safety Integrated
SS1: Safe Stop 1
STO: Safe Torque Off / SH: Safe standstill
SSM: Safe Speed Monitor (safety-relevant feedback signal from the speed monitoring)
p9852
SI Safe Stop 1 delay time (Motor Module) / SI Stop 1 t_del MM
Access level:
3
Calculated:
-
Data type:
FloatingPoint32
Can be changed:
C(95)
Scaling:
-
Dyn. index:
-
Unit group:
-
Unit selection:
-
Func. diagram:
-
Min Max
Factory
setting
0.00 [ms]
300000.00 [ms]
0.00 [ms]
r9871
SI common functions (processor 2) / SI common fct P2
Access level:
3
Calculated:
-
Data type:
Unsigned32
Can be changed:
-
Scaling:
-
Dyn. index:
-
Unit group:
-
Unit selection:
-
Func. diagram:
2804
Min Max
Factory
setting
- - -
Bit field:
Bit
Signal name
1 signal
0 signal
FP
00
STO supported via terminals
Yes
No
2804
01
SBC supported
Yes
No
2804
02
Extended Functions supported (p9501 > 0)
Yes
No
2804
03
SS1 supported
Yes
No
2804
04
Extended Functions PROFIsafe supported
Yes
No
-
05
Extended Functions integrated in drive
supported (p9601.2 = 1)
Yes
No
-
06
Basic Functions PROFIsafe supported
Yes
No
-
07
Extended Functions encoderless supported Yes
No
-
11
Extended Functions SDI supported
Yes
No
-
12
Extended Functions SSM encoderless
supported
Yes
No
-
19
Power Module STO is supported
Yes
No
-
Содержание SINAMICS G120
Страница 1: ...SINAMICS SINAMICS G120 CU250S 2 Control Units List Manual 09 2017 Edition www siemens com drives ...
Страница 2: ......
Страница 726: ...2 Parameters 2 6 Quick commissioning p0010 1 SINAMICS G120 CU250S 2 Control Units 726 List Manual 09 2017 A5E33842890 ...
Страница 990: ...3 Function diagrams 3 26 Data sets SINAMICS G120 CU250S 2 Control Units 990 List Manual 09 2017 A5E33842890 ...
Страница 1242: ...A Appendix A 2 List of abbreviations SINAMICS G120 CU250S 2 Control Units 1242 List Manual 09 2017 A5E33842890 ...
Страница 1255: ......