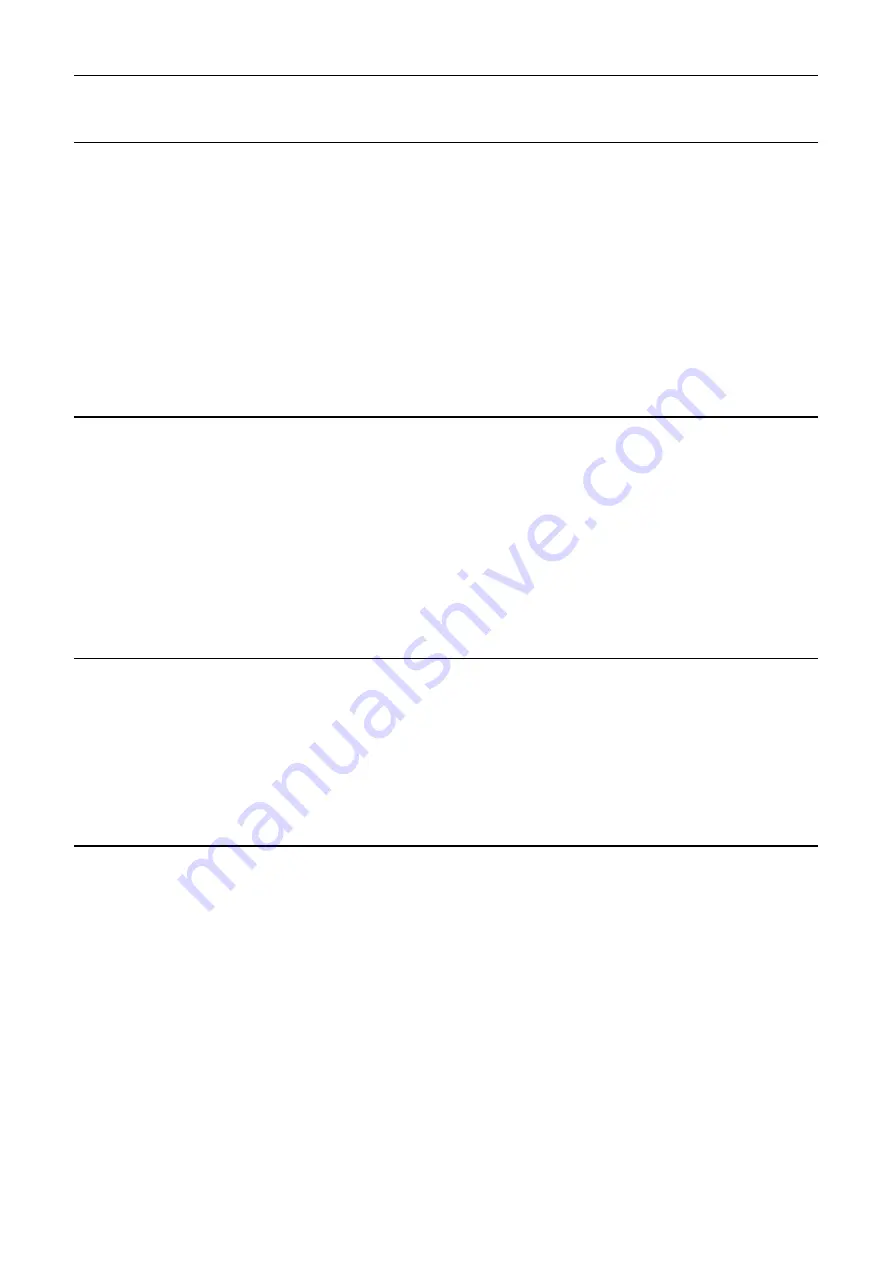
2 Parameters
2.2 List of parameters
SINAMICS G120 CU250S-2 Control Units
282
List Manual, 09/2017, A5E33842890
Description:
Sets the speed threshold value to detect a stalled motor.
If the adaptation controller output exceeds the parameterized speed difference, then in status word r1408.11 is set =
1.
Dependency:
If a stalled drive is detected (r1408.11 = 1), fault F07902 is output after the delay time set in p2178.
Not visible with application class: "Standard Drive Control" (SDC, p0096 = 1)
Refer to: p2178
Note:
Speed monitoring is only effective in operation with a speed encoder (refer to p1300).
Stalling is also identified if steps/jumps occur in the speed signal, which exceed the value in p0492.
Description:
Sets the fault threshold in order to detect a motor that has stalled.
If the error signal (r1746) exceeds the parameterized error threshold, then status signal r1408.12 is set to 1.
Dependency:
If a stalled drive is detected (r1408.12 = 1), fault F07902 is output after the delay time set in p2178.
Not visible with application class: "Standard Drive Control" (SDC, p0096 = 1)
Refer to: p2178
Note:
Monitoring is only effective in the low-speed range (below p1755 * (100% - p1756)).
Description:
Signal to initiate stall detection
Dependency:
Not visible with application class: "Standard Drive Control" (SDC, p0096 = 1)
Note:
The signal is not calculated while magnetizing and only in the low speed range (below p1755 * (100 % - p1756)).
Description:
Minimum operating frequency for rugged operation.
If the minimum value is greater than the lower changeover limit parameterized with p1755 * (1 - 2 * p1756), then the
difference is displayed using p1749 * p1755. The parameter value cannot be changed.
Dependency:
Not visible with application class: "Standard Drive Control" (SDC, p0096 = 1)
Refer to: p1752, p1755, p1756
p1744[0...n]
Motor model speed threshold stall detection / MotMod n_thr stall
Access level:
4
Calculated:
p0340 = 1,3
Data type:
FloatingPoint32
Can be changed:
U, T
Scaling:
-
Dyn. index:
DDS, p0180
Unit group:
3_1
Unit selection:
p0505
Func. diagram:
-
Min Max
Factory
setting
0.00 [rpm]
210000.00 [rpm]
100.00 [rpm]
p1745[0...n]
Motor model error threshold stall detection / MotMod ThreshStall
Access level:
3
Calculated:
p0340 = 1,3
Data type:
FloatingPoint32
Can be changed:
U, T
Scaling:
-
Dyn. index:
DDS, p0180
Unit group:
-
Unit selection:
-
Func. diagram:
-
Min Max
Factory
setting
0.0 [%]
1000.0 [%]
5.0 [%]
r1746
Motor model error signal stall detection / MotMod sig stall
Access level:
3
Calculated:
-
Data type:
FloatingPoint32
Can be changed:
-
Scaling:
-
Dyn. index:
-
Unit group:
-
Unit selection:
-
Func. diagram:
-
Min Max
Factory
setting
- [%]
- [%]
- [%]
p1749[0...n]
Motor model increase changeover speed encoderless operation / Incr n_chng no enc
Access level:
4
Calculated:
p0340 = 1,3
Data type:
FloatingPoint32
Can be changed:
U, T
Scaling:
-
Dyn. index:
DDS, p0180
Unit group:
-
Unit selection:
-
Func. diagram:
-
Min Max
Factory
setting
0.0 [%]
99.0 [%]
50.0 [%]
Содержание SINAMICS G120
Страница 1: ...SINAMICS SINAMICS G120 CU250S 2 Control Units List Manual 09 2017 Edition www siemens com drives ...
Страница 2: ......
Страница 726: ...2 Parameters 2 6 Quick commissioning p0010 1 SINAMICS G120 CU250S 2 Control Units 726 List Manual 09 2017 A5E33842890 ...
Страница 990: ...3 Function diagrams 3 26 Data sets SINAMICS G120 CU250S 2 Control Units 990 List Manual 09 2017 A5E33842890 ...
Страница 1242: ...A Appendix A 2 List of abbreviations SINAMICS G120 CU250S 2 Control Units 1242 List Manual 09 2017 A5E33842890 ...
Страница 1255: ......