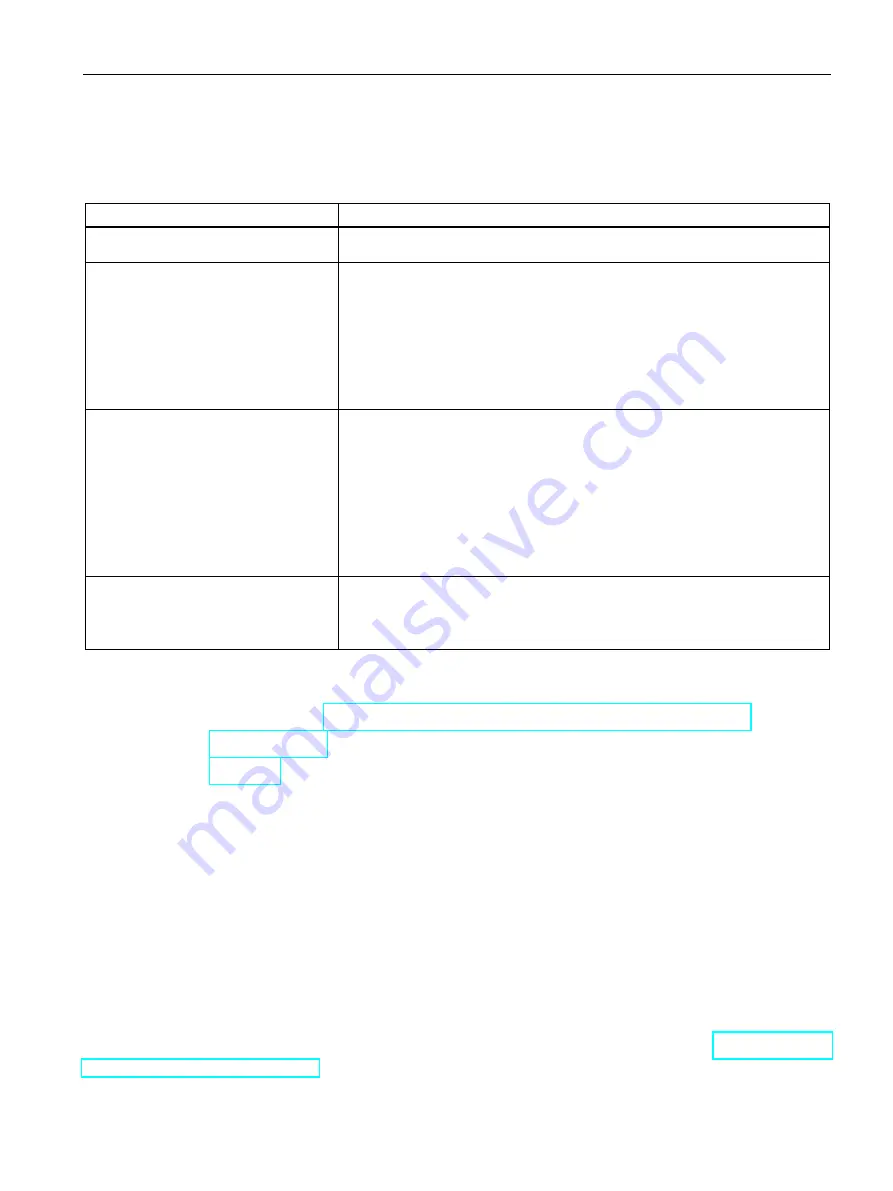
Description
2.1 Introduction to PROFINET
PROFINET with STEP 7
Function Manual, 05/2021, A5E03444486-AL
23
IO communication via PROFINET IO
Table 2- 1
IO communication via PROFINET IO
Communication between ...
Explanation
IO controllers and IO devices
The IO controller sends data cyclically to the IO devices of its PROFINET IO system
and receives data from these devices.
IO controller and I-device
A fixed quantity of data is transferred cyclically between the user programs in
CPUs of IO controllers and I-devices.
The IO controller does not access the I/O module of the I-device, but instead
accesses configured address ranges, i.e. transfer ranges, which may be located
inside our outside the process image of the CPU of the I-device. If parts of the
process image are used as transfer ranges, it is not permitted to use these for
real I/O modules.
Data transfer takes place using load- and transfer operations via the process
image or via direct access.
IO controller and IO controller (PN/PN
coupler)
A fixed quantity of data is cyclically transferred between the user programs in
CPUs of IO controllers. A PN/PN coupler is required as additional hardware.
The IO controllers mutually access configured address ranges, i.e. transfer rang-
es, which may be located inside or outside the process image of the CPU. If parts
of the process image are used as transfer ranges, it is not permitted to use these
for real I/O modules.
Data transfer takes place using load- and transfer operations via the process
image or via direct access.
I/O communication with PN/PN coupler is possible between two PROFINET IO
systems.
S7-1500-CPU and S7-1500-CPU (direct
data exchange)
In the case of direct data exchange, an S7-1500 CPU provides cyclic user data
from the I/O area to one or more partners.
The direct data exchange is based on PROFINET with IRT and isochronous mode.
The data exchange takes place via transfer areas.
See also
Communication (
http://support.automation.siemens.com/WW/view/en/59192925
Network security (Page 1)
Functions (Page 1)
2.1.2
Basic terminology of communication
PROFINET communication
PROFINET communication takes place via Industrial Ethernet. The following transmission
types are supported:
•
Acyclic transmission of engineering and diagnostics data and interrupts
•
Cyclic transmission of user data
The PROFINET-IO communication takes place in real-time.
For additional information on the real-time communication, refer to chapter Real-time
communication (Page 1).
Summary of Contents for SIMATIC ET 200AL
Page 2: ......
Page 143: ......
Page 218: ......
Page 250: ......
Page 296: ......
Page 337: ......
Page 365: ......
Page 392: ......
Page 419: ......
Page 451: ......
Page 483: ......
Page 597: ......
Page 648: ......
Page 702: ......
Page 739: ......
Page 781: ......
Page 804: ......
Page 828: ......
Page 853: ......
Page 880: ......
Page 906: ......
Page 996: ...Diagnostics ...
Page 1121: ......
Page 1565: ......