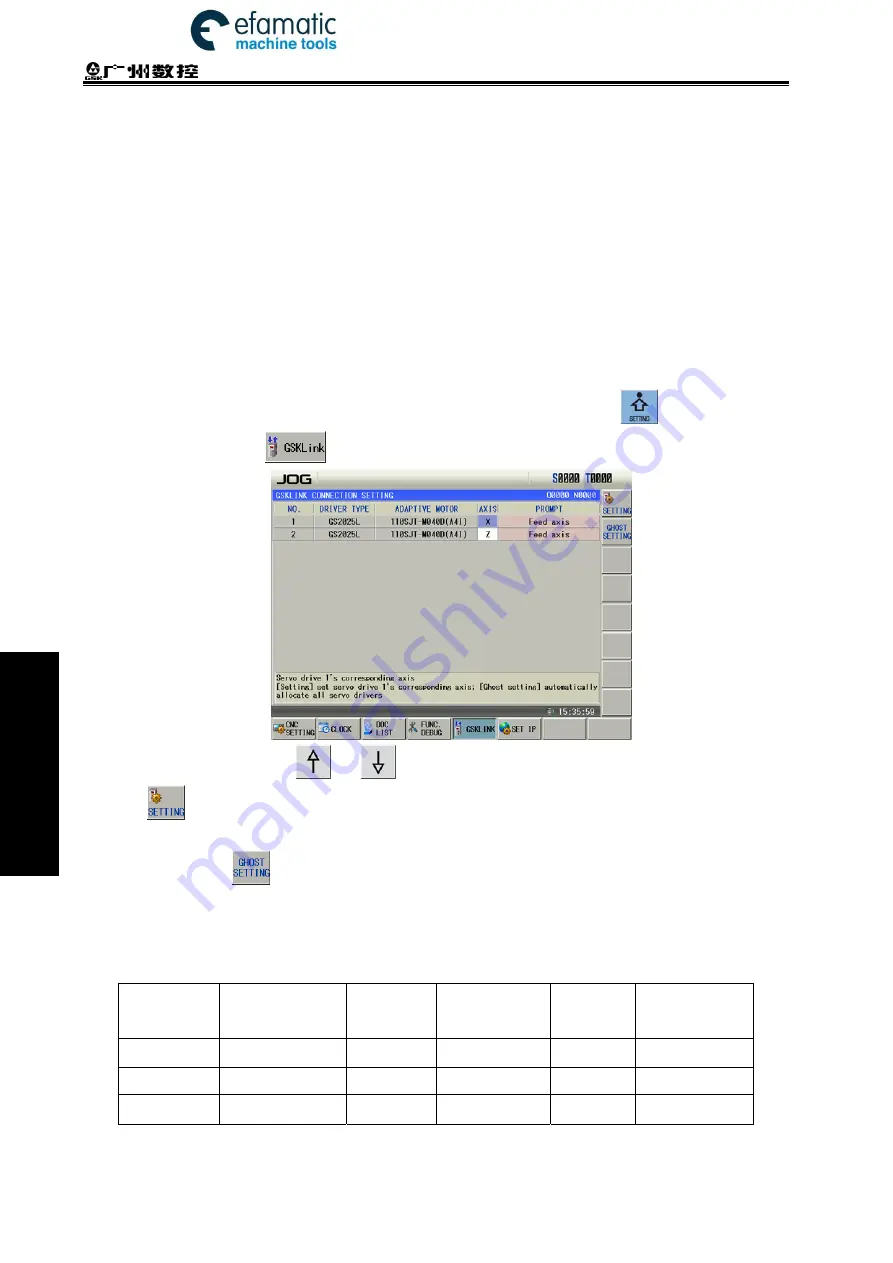
Official GSK Agents in South Africa
Tel: +27 11 626 2720, [email protected]
GSK980TDi Turning CNC System User Manual
484
Ⅲ
Connection
The Bit 7 of PLC parameter K10 equals to 1: The overtravel function along each axis is enabled;
The Bit6 of PLC parameter K10: High/Low LEVEL selection of overtravel signal
In the Manual or MPG mode, slowly move the effectiveness of the overtravel limit swith of each
axis verification or the correction of alarm display; the CNC ESP alarm may occur when pressing the
ESP button is controlled; when the overtravel alarm occurs, it will moves towards to the negative
direction; after moving out the limit position, the resetting clear alarm then can be pressed.
4.2 Drive Unit Configuration
The corresponding axis of each servo drive unit should be set based upon the valid configuration
of the system, which can be directly set on the page of “Setting->GSKLink setting” based upon the
2-level authorities.
Under the 2-level or more authorities, enter to the setting page by
, and then to the
GSKLink setting page by
, the display is shown below:
Select the servo drive by
or
button, set the selected corresponding axis of the servo
drive by
: When the connection sequence of the servo drive is: X axis, Z axis, Y axis, the 4
th
axis,
the 5
th
axis, spindle 1, spindle 2 or spindle 3 (regardless of the unavailable axis), the overall servo
drives can be set by
.
If the connection sequence of the servo axis does not correct, we would not definitely know the
corresponding servo drive of each axis on the page of the “Setting->GSKLink setting”, it can be
directly set at the side of the servo side. The corresponding setting parameter of the servo is PA156;
the comparison table of the parameter setting is shown below:
System
axis
Servo
parameter
System
axis
Servo
parameter
System
axis
Servo
parameter
X 1 Y
3
5TH
5
Z 2
4TH
4
Spindle 1
11
Spindle 2
12
Spindle 3
13
The Bit 4, Bit 3, Bit 2, Bit 1 and Bit 0 (DIR4, DIR5, DIRY, DIRZ or DIRX separately corresponds to
the 5
th
, the 4
th
, Y, Z or X axis) of the state parameter No.008 can be modified if the machine tool