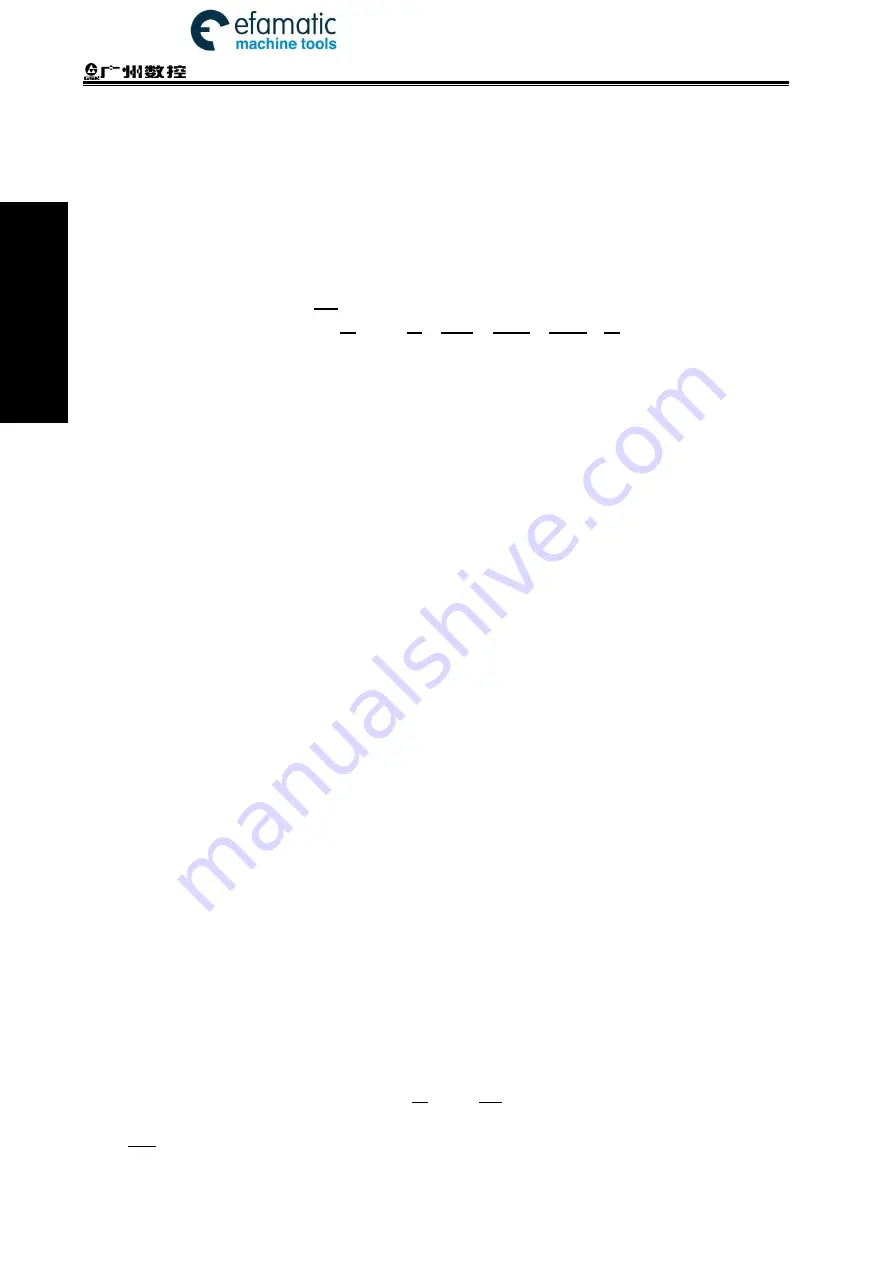
Official GSK Agents in South Africa
Tel: +27 11 626 2720, [email protected]
GSK980TDi Turning CNC System User Manual
124
Ⅰ
Programming
6. There are no the same block number in ns~nf when compound cycle commands are
executed repetitively in one program.
7. In
ns
~
nf, the program block quantity cannot exceed 100;
8. The tool retraction point should be high or low as possible to avoid crashing the
workpiece.
3.22.5 Axial Grooving Multiple Cycle G74
Command format:
G74 R(e) ;
G74 X(U) Z(W) P(
Δ
i) Q(
Δ
k) R(
Δ
d) F ;
Command function:
Axial (X axis) tool infeed cycle compounds radial discontinuous cutting
cycle: Tool infeeds from starting point in radial direction( Z), retracts, infeeds again,
and again and again, and last tool retracts in axial direction, and retracts to the Z
position in radial direction, which is called one radial cutting cycle; tool infeeds in axial
direction and execute the next radial cutting cycle; cut to end point of cutting, and
then return to starting point (starting point and end point are the same one in G74),
which is called one radial grooving compound cycle. Directions of axial tool infeed
and radial tool infeed are defined by relative position between end point X(U) Z(W)
and starting point of cutting. G75 is used for machining radial loop groove or column
surface by radial discontinuously cutting, breaking stock and stock removal.
Relevant definitions:
Starting point of axial cutting cycle:
starting position of axial tool infeed for each axial cutting
cycle, defining with A
n
(n=1,2,3……), Z coordinate of A
n
is
the same that of starting point A,
the different value of X
coordinate between A
n
and A
n-1
is
Δ
i. The starting point A
1
of the first axial cutting cycle is the same as the starting
point A, and the X coordinate of starting point (A
f
) of the
last axial cutting cycle is the same that of cutting end point.
End point of axial tool infeed:
starting position of axial tool infeed for each axial cutting cycle,
defining with B
n
(n=1,2,3……), Z coordinate of B
n
is the same
that of cutting end point,
X coordinate of B
n
is the same that of
A
n
, and the end point (B
f
) of the last axial tool infeed is the
same that of cutting end point.
End point of radius tool retraction:
end
position of radius tool infeed (travel of tool infeed is
Δ
d)
after each axial cutting cycle reaches the end point of axial
tool infeed, defining with C
n
(n=1,2,3……), Z coordinate of
C
n
is the same that of cutting end point, and the different
value of X coordinate between C
n
and A
n
is
Δ
d;
End point of axial cutting cycle:
end
position of axial tool retraction from the end point of
radius tool retraction, defining with D
n
(n=1, 2, 3……), Z
coordinate of D
n
is the same that of starting point, X
coordinate of D
n
is the same that of C
n
(the different value
of X coordinate between it and A
n
is
Δ
d);
Cutting end point:
it is defined by X(U) Z(W) , and is defined with B
f
of the last axial
tool infeed.
R(e) : it is the tool retraction clearance after each axial(Z) tool infeed, and its range is
0~99.999(IS-B)/0~99.9999(IS-C) (unit:mm,radius) without sign symbols. The specified