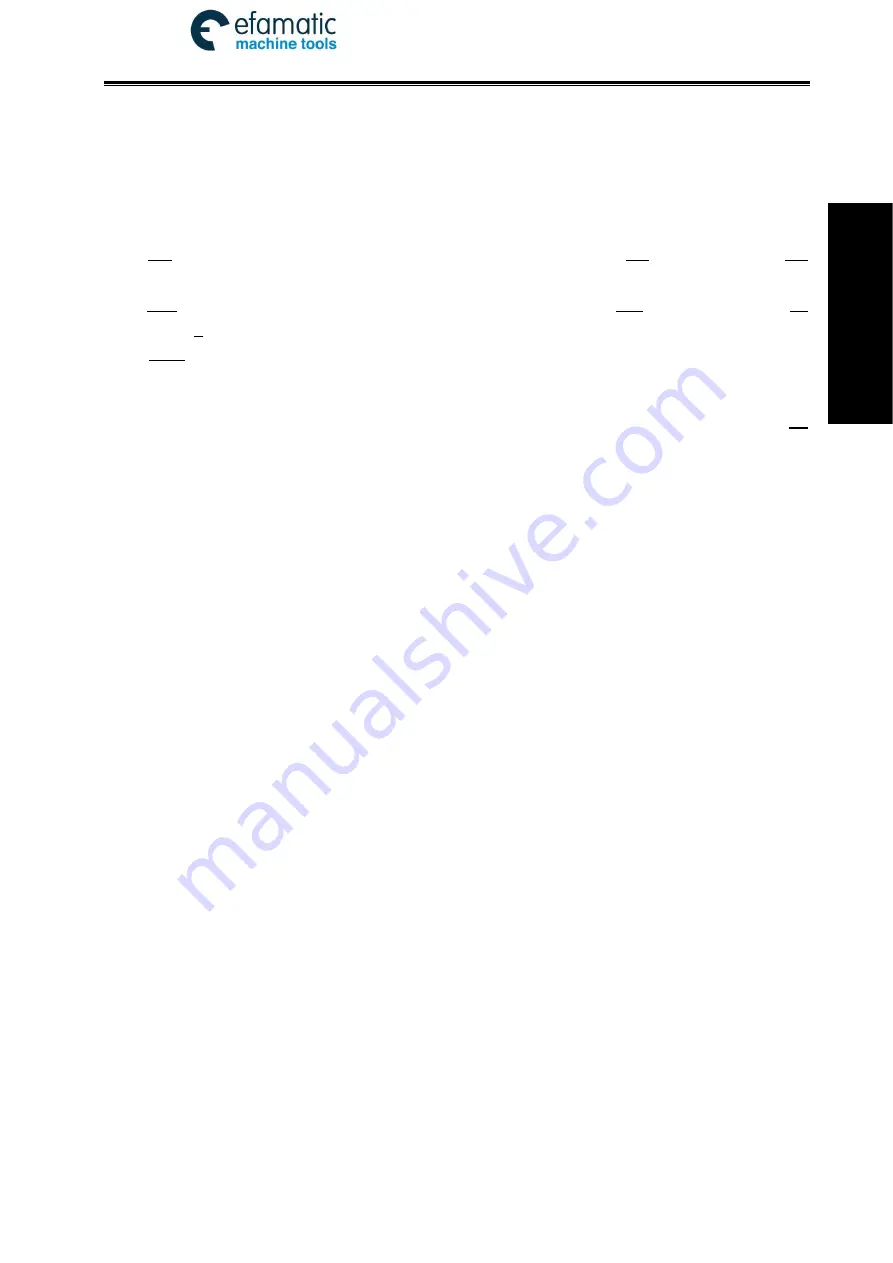
Official GSK Agents in South Africa
Tel: +27 11 626 2720, [email protected]
Chapter 3 G Commands
125
Ⅰ
Programming
value is reserved validly after R(e) is executed. The NO.056 value is regarded as the
tool retraction clearance when R(e) is not input.
X: X absolute coordinate value of cutting end point B
f
(unit: mm).
U: Different value of X absolute coordinate between cutting end point B
f
and starting point.
Z: Z absolute coordinate value of cutting end point B
f
(unit: mm).
W: Different value of Z absolute coordinates between cutting end point B
f
and starting point.
P
(
Δ
i)
:
radial(X) cutting for each axial cutting cycle , range: 0
<
Δ
i
≤
9999999(IS_B)/0
<
Δ
i
≤
99999999
(
IS_C
)
(unit: least input increment, diameter value, without sign symbol).
Q
(
Δ
k)
:
radial(Z) cutting for each axial cutting cycle, range: 0
<
Δ
k
≤
9999999(IS_B)/0
<
Δ
k
≤
99999999
(
IS_C
)
(unit: least input increment, diameter value, without sign symbol).
R(
Δ
d) : radial (X) tool retraction after cutting to end point of axial cutting, range: 0~99999999×
least input increment (unit: mm/inch, diameter value, without sign symbol).. The radial (X)
tool retraction clearance is 0 when the system defaults the axial cutting end point. The
system defaults the tool retraction is executed in positive direction when X(U) and P(
Δ
i)
are omitted.
Execution process:
(Fig. 3-79)
①
Axial (Z) cutting feed
△
k from the starting point of axial cutting cycle, feed in Z
negative direction when the coordinates of cutting end point is less than that of
starting point in Z direction, otherwise, feed in Z positive direction;
②
Axial (Z) rapid tool retraction e and its direction is opposite to the feed direction of
①
;
③
X executes the cutting feed (
Δ
k+e) again, the end point of cutting feed is still in it
between starting point A
n
of axial cutting cycle and end point of axial tool infeed, Z
executes the cutting feed (
Δ
k+e)again and execute
②
; after Z executing the cutting
feed (
Δ
k+e)again, the end point of cutting feed is on B
n
or is not on it between A
n
and
B
n
cutting feed to B
n
in Z direction and then execute
④
;
④
Radial(X) rapid tool retraction
△
d/2 to C
n
, when X coordinate of B
f
(cutting end point)
is less than that of A (starting point), retract tool in X positive, otherwise, retract tool
in X negative direction;
⑤
Axial(Z axial) rapid retract tool to Dn, No. n axial cutting cycle is completed. If the
current axial cutting cycle is not the last one, execute
⑥
; if it is the previous one
before the last axial cutting cycle, execute
⑦
;
⑥
Radial(X axial)rapid tool infeed, and it direction is opposite to
④
retract tool. If the end
point of tool infeed is still on it between A and A
f
(starting point of last axial cutting
cycle) after X executes the tool infeed (
△
d/2+
△
i/2) , i.e. D
n
→
A
n+1
and then execute
①
(start the next axial cutting cycle); if X end point of tool infeed is not on it between
D
n
and A
f
after tool infeed (
△
d/2+
△
i/2), rapidly traverse to A
f
and execute
①
to start
the first axial cutting cycle;
⑦
X rapidly traverse to return to A, and G74 is completed.