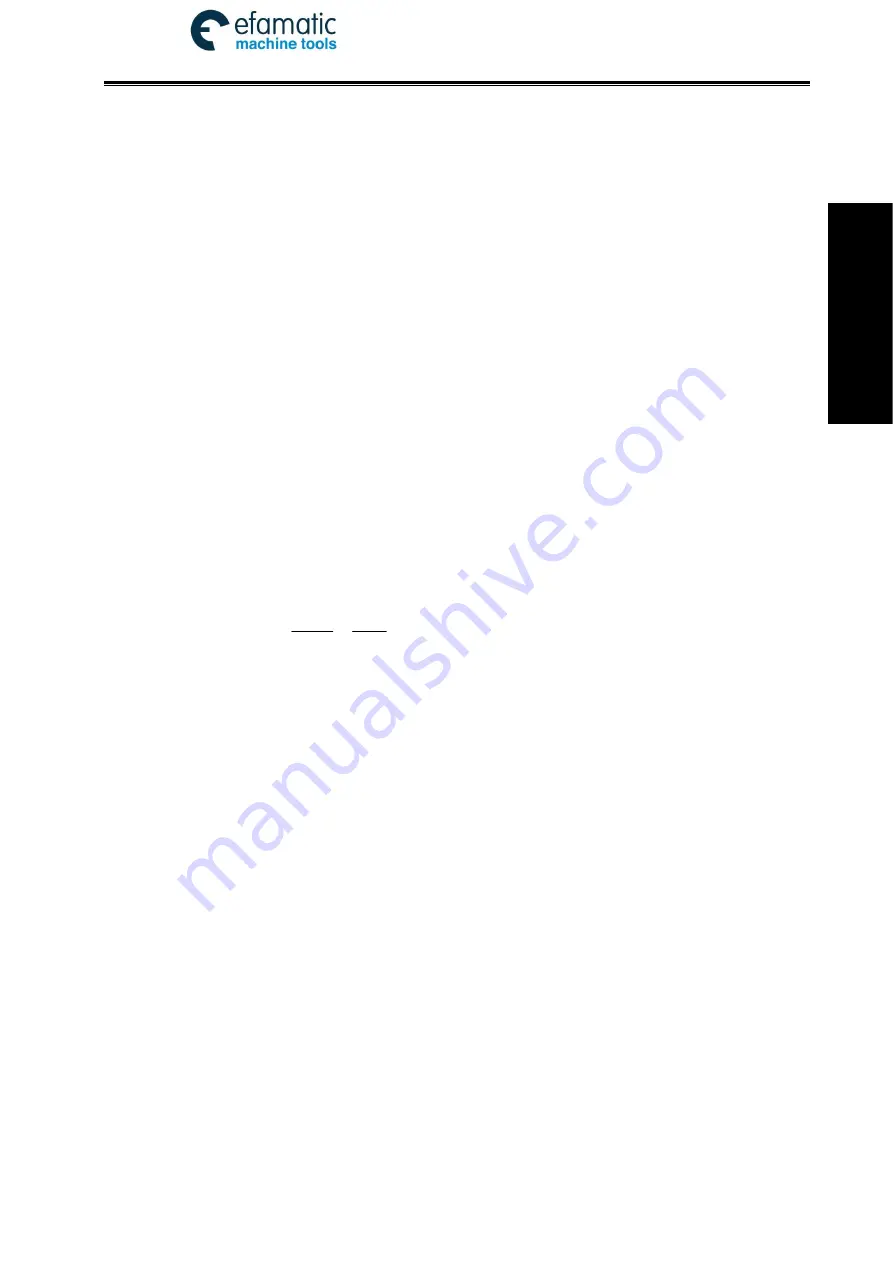
Official GSK Agents in South Africa
Tel: +27 11 626 2720, [email protected]
Chapter 3 G Commands
119
Ⅰ
Programming
Blocks for some continuous finishing path, counting the ro
⑶
ughing path without being
executed actually when executing G73.
According to the finishing allowance, the travel of tool retraction and the cutting times, the system
automatically counts the travel of roughing offset, the travel of each tool infeed and the path of
roughing, the path of each cutting is the offset travel of finishing path, the cutting path
approaches gradually the finishing one, and last cutting path is the finishing one according to the
finishing allowance. The starting point and end point of G73 are the same one, and G73 is
applied to roughing for the formed rod. G73 is non-modal and its path is shown in Fig.3-77.
Relevant definitions:
Finishing path:
The above-mentioned Part 3 of G73
(
ns
~
nf block)defines the finishing path,
and the starting point of finishing path (start point of ns block)is the same these
of starting point and end point of G73, called A point; the end point of the first
block of finishing path(ns block)is called B point; the end point of finishing
path(end point of nf block) is called C point. The finishing path is A
→
B
→
C.
Roughing path:
It is one group of offset path of finishing one, and the roughing path times are
the same that of cutting. After the coordinates offset, A, B, C of finishing path
separately corresponds to A
n
, B
n
, C
n
of roughing path(n is the cutting times,
the first cutting path is A
1
, B
1
, C
1
and the last one is A
d
, B
d
, C
d
). The
coordinates offset value of the first cutting compared to finishing path is
(
Δ
i×2+
Δ
u,
Δ
w+
Δ
k) (diameter programming) , the coordinates offset value of
the last cutting compared to finishing path is(
Δ
u,
Δ
w) , the coordinates offset
value of each cutting compared to the previous one is as follows:
)
1
,
1
2
(
−
Δ
−
−
×
Δ
−
d
k
d
i
Δ
i: It is X tool retraction clearance in roughing, and its range is ±99999999× least input
increment (radius, unit: mm/inch, with sign symbol) ,
Δ
i is equal to X coordinate offset
value (radius value) of A1 point compared to Ad point. The X total cutting travel(radius
value) is equal to |
Δ
i| in roughing, and X cutting direction is opposite to the sign of
Δ
i:
Δ
i
>
0, the system executes X negative cutting in roughing.The No.053 value is regarded
as X tool retraction clearance in roughing when U(
Δ
i) is not input.
Δ
k: It is Z tool retraction clearance in roughing, and its range is -99999.999
~
99999.999(IS_B
)
/-9999.9999
~
9999.9999(IS_C) (radius, unit: mm/inch, with sign
symbol) ,
Δ
k is equal to Z coordinate offset value (radius value) of A1 point compared to
Ad point. Z total cutting travel(radius value) is equal to |
Δ
k| in roughing, and Z cutting
direction is opposite to the sign of
Δ
k:
Δ
k
>
0, the system executes Z negative cutting in
roughing.The No.054 value is regarded as Z tool retraction clearance in roughing when
W(
Δ
k) is not input.
d: It is the cutting times 1~9999 (unit: times). R5 means the closed cutting cycle is completed
by 5 times cutting.No.055 value is regarded as the cutting times when R(d) is not input.
When the cutting times is 1, the system completes the closed cutting cycle based on 2
times cutting.
ns: Block number of the first block of finishing path.
nf: Block number of the last block of finishing path.
Δ
u: It is X finishing allowance and its range is -99999.999~99999.999(IS_B
)
/-9999.9999~9999.9999(IS_C) (diameter, unit: mm/inch, with sign symbol) and is the X
coordinate offset of roughing path compared to finishing path, i.e. the different value of