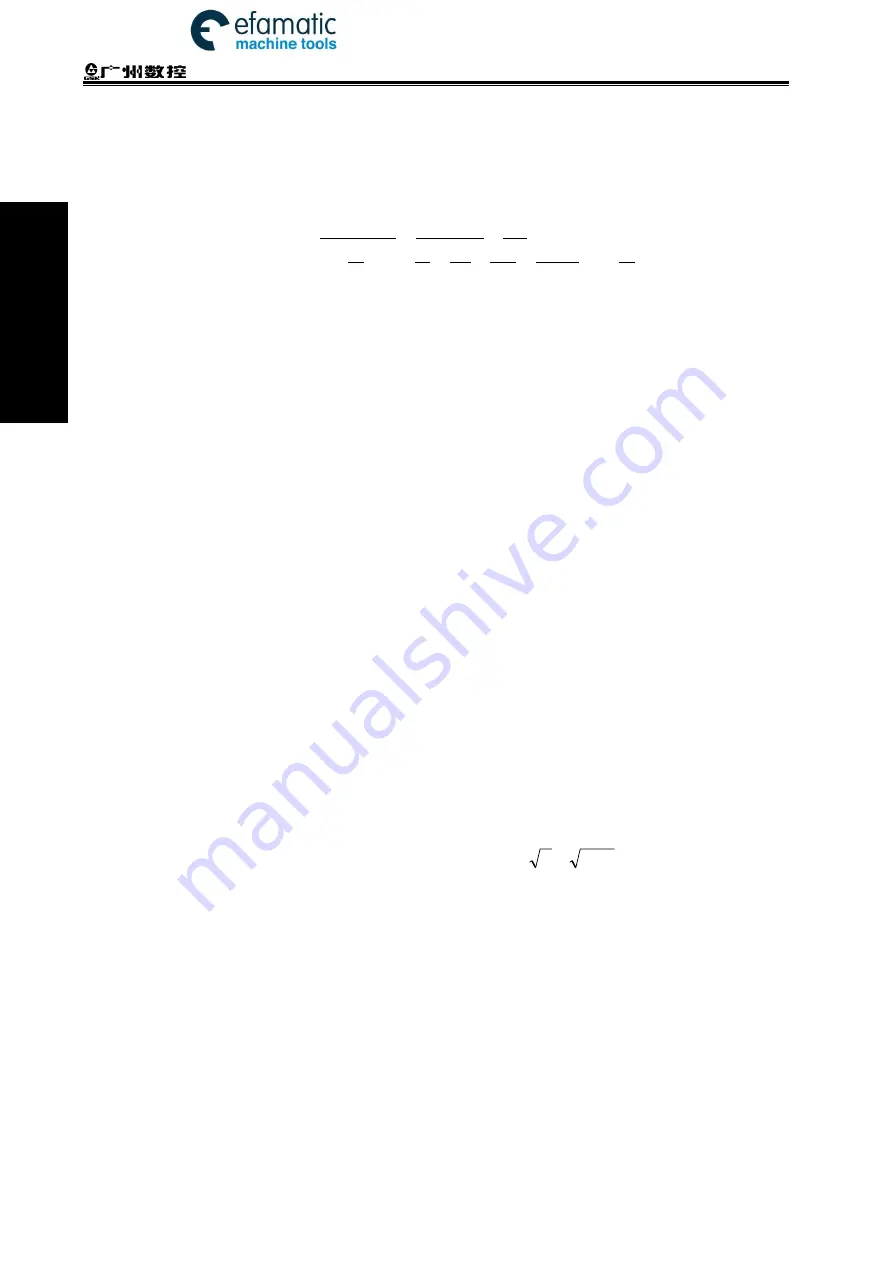
Official GSK Agents in South Africa
Tel: +27 11 626 2720, [email protected]
GSK980TDi Turning CNC System User Manual
154
Ⅰ
Programming
position where the axis operation speed of servo drive along each axis is 1m/min);
otherwise, the recovered thread may be generated an offset;
3.23.10 Multiple Thread Cutting Cycle G76
Command format:
G76 P(m) (r) (a) Q(
△
dmin) R(d) ;
G76 X(U) Z(W) R(i) P(k) Q( d)
△
F(I) ;
Command function:
Machining thread with specified depth of thread (total cutting depth) is
completed by multiple roughing and finishing, if the defined angle of
thread is not 0°, thread run-in path of roughing is from its top to bottom,
and angle of neighboring thread teeth is the defined angle of thread. G76
can be used for machining the straight and taper thread with thread
run-out path, which is contributed to thread cutting with single tool edge to
reduce the wear of tool and to improve the precision of machining thread.
But G76 cannot be used for machining the face thread. Machining path is
shown in Fig. 3-94:
Command specifications:
X:
X absolute coordinate (unit: mm) of thread end point;
U:
Different value (unit: mm) of X absolute coordinate between thread end point and starting point;
Z:
Z absolute coordinate (unit: mm) of thread end point;
W:
Different value (unit: mm) of Z absolute coordinate between thread end point and starting point;
P(m):
Times of thread finishing: 00
~
99 (unit: times). The value of system parameter
№
057 is
regarded as finishing times when m is not input. In thread finishing, every feed cutting amount is
equal to the cutting amount d in thread finishing dividing the finishing times m;
P(r):
Width of thread run-out 00
~
99(unit: 0.1×L,L is the thread pitch). The value of system parameter
№
019 is the width of thread run-out when r is not input. The thread run-out function can be applied to
thread machining without tool retraction groove and the width of thread run-out defined by system
parameter
№
019 is valid for G92, G76;
P(a):
Angles at taper of neighboring two tooth
,
range: 00
~
99
,
unit
:
deg(°). The system parameter
№
058 value is regarded as angle of thread tooth. The actual angle of thread in defined by tool ones
and so a should be the same as the tool angle;
Q( dmin):
△
△
Minimum cutting travel of thread roughing, range: 0
~
999999( IS-C)/ 0
~
99999( IS-B),(unit: least input increment, radius value). When (
1
n
n
−
−
) × d
△
<
dm
△
in, dmin
△
is regarded as the cutting travel of current roughing and the subsequent rough-machining cutting
value and the in-feed depth will not calculate based upon the formula any more. Setting dmin is to
△
avoid the too small of roughing amount and too many roughing times caused by the cutting amount
deceleration in thread roughing. When Q ( dmin) is not input, the system data parameter NO.059
△
value is taken as the least cutting amount;
R(d):
It is the cutting amount in thread finishing, range: 00
~
99.999(IS_B
)
/00
~
99.9999(IS_C) (unit:
mm/inch, radius value without sign symbols), the radius value is equal to X absolute coordinates
between cut-in point Be of thread finishing and Bf of thread roughing.. The value of system parameter
№
060 is regarded as the cutting travel of thread finishing when R(d) is not input;
R(i):
It is thread taper and is the different value of X absolute coordinate between thread starting point
and end point, rang: -99999.999~99999.999(IS_B
)
/-9999.9999~9999.9999(IS_C) (unit:
:
mm/inch,
radius value). The system defaults R(i)=0(straight thread) when R(i) is not input;