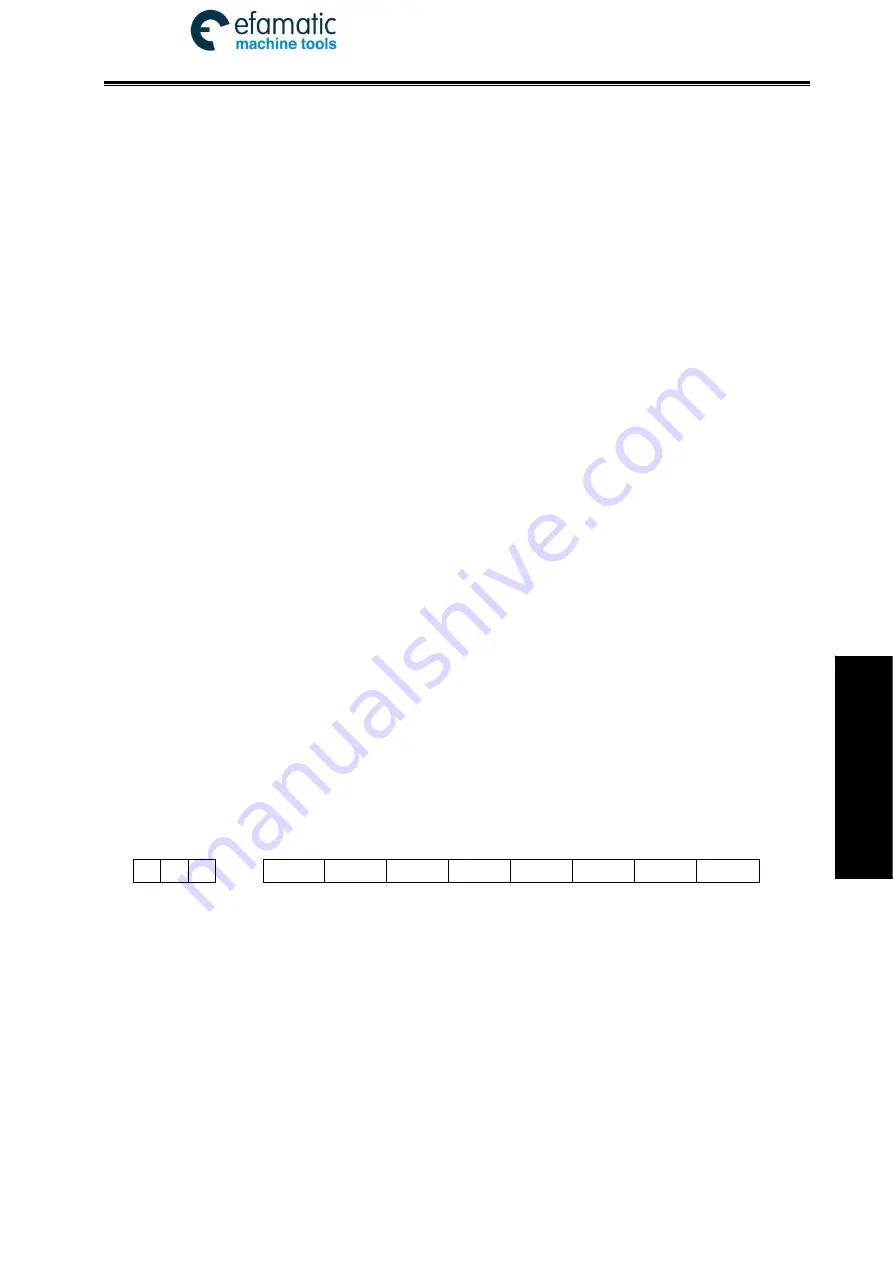
Official GSK Agents in South Africa
Tel: +27 11 626 2720, [email protected]
Chapter 2 Definition and Connection of Interface Signal
405
Ⅲ
Connection
gearing is inactive, alarm will be issued when M41
~
M44 is being executed and only one of them is
active at a time.
When spindle auto gearing is used to control automatic spindle mechanical gear switching, as
CNC executes S
□□□□
code, it calculates the analog voltage output to spindle servo or frequency
inverter based on the parameter of the current gear by M4n (M41
~
M44 to data parameters
No.037~No.040 respectively) to make the actual speed to be consistent with the S code.
When CNC is powered on, the spindle gear memorizing is set by the BIT1 of bit parameter
No.168.
If the BIT4 of bit parameter No.001 is 0, the spindle gear is not memorized at repowering after
power down, and the gear 1 will be defaulted, M41~M44 are not output. If BIT4 of bit parameter
No.001 is 1, the spindle gear is memorized at repowering after power down.
No gearing is done if the specified gear is consistent with the current gear. If not, gearing will be
performed, and the process defined by standard ladders is shown in the following:
Execute any of M41, M42, M43, M44 codes, output analog voltage to spindle servo or
①
frequency inverter according to a value set by data parameter No.067 (Unit: mV);
After a delay (gearing time 1) by the DT00, turn off the original gear output signal and o
②
utput
the new gearing signal;
If the gear is 1 or 2, and the BIT6 of the bit parameter No.164 is 1, it jumps to , or else it
③
④
jumps to ;
⑤
Check the gear in
④
-position input signal M41I, M42I, it jumps to if the gear in
⑤
-position is done;
if not, the CNC waits the gear in-position signal;
After a delay (gearing time 2) by DT01, output spindle analog voltage by the current gear
⑤
according to a value set by data parameter No.037~No.040 (gear 1~4) and finish the gearing.
Note: The output of M41
~
M44 is held on when CNC is reset or i emergency stop, which is defined by
standard PLC ladder.
2.9.7 Spindle 8-point Orientation Function
z
Command format
M51: spindle orientation command
M50 : cancel spindle orientation command
Note: When the system is matched with GS-L Spindle Servo Unit, it can realize one-point orientation.
z
Control parameter
K 1 5
SPOR
SPOR =1: The spindle eight-orientation function is valid.
=0: The spindle eight-orientation function is invalid.
z
Functional description(standard PLC program definition)
1. After the positioning function commands M51 are executed, PLC
→
CNC executes the
orientation signal.
2. CNC issues an orientation command after reciving the orientation signal; (after the system
delays 100ms, the spindle rotation(CW/CCW) is disabled, at the same time, the system starts to
check the orientation completion signal (COIN
)
.
3. Drive unit starts the orientation.
4. After the drive unit orientation is completed, Drive
→
CNC
→
PLC outputs the spindle
completion signal COIN;
5. After PLC receives the spindle orientation completion signal COIN, the spindle orientation is
completed, but the spindle orientation signal STAO keeps the output.