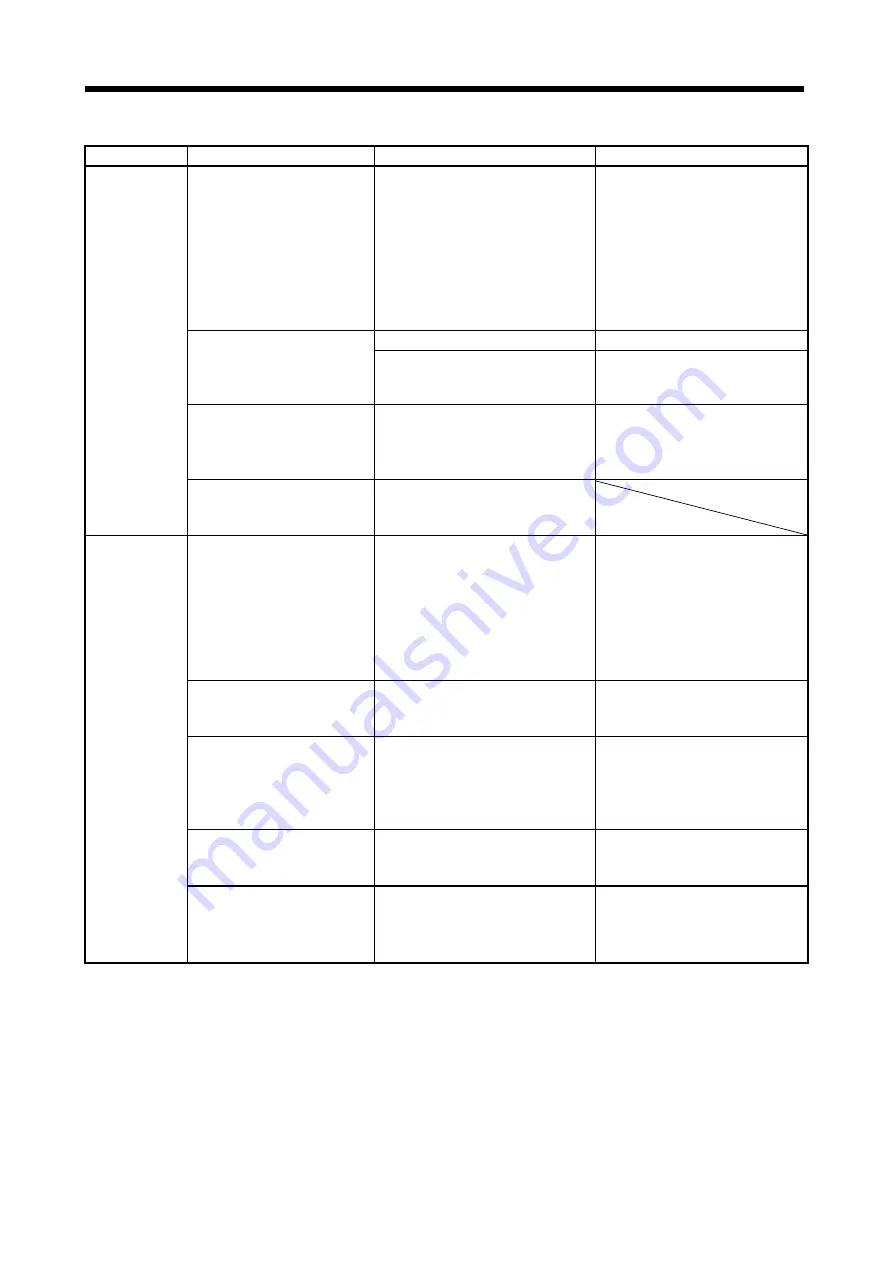
17 - 66
17. SPEED CONTROL OPERATION
Description
Check method
Possible cause
Action
An unusual
noise is
occurring at the
servo motor.
1. If the servo motor can be
driven safely, repeat
acceleration and deceleration
three or four times to
complete auto tuning.
2. Reduce the auto tuning
response (parameter
No.PA09). (Except for the
manual mode)
1. The servo gain is high.
2. The auto tuning response is high.
Decrease the auto tuning response,
and readjust the gain. (Refer to
chapter 9.)
If the servo motor can be driven
safely, remove the load, and
check for a noise only on the
servo motor.
If there is noise, the life of the bearing. Change the servo motor.
If there is no noise, increase the
backlash of the mechanical part.
Perform adjustment on the load side.
For a servo motor with an
electromagnetic brake, check
the dragging of the brake.
1. The sequence of releasing the
electromagnetic brake is incorrect.
2. Failure of power supply for the
electromagnetic brake.
1. Check the sequence of releasing
the electromagnetic brake.
2. Check the power supply for the
electromagnetic brake.
The brake rattles when using a
servo motor with an
electromagnetic brake.
The noise is due to a gap between the
connections of brake, not a fault.
The servo motor
vibrates.
1. If the servo motor can be driven
safely, repeat acceleration and
deceleration three or four times
to complete auto tuning.
2. Reduce the auto tuning
response (parameter
No.PA09). (Except for the
manual mode)
1. The servo gain is too high.
2. The auto tuning response is too high.
Decrease the auto tuning response,
and readjust the gain. (Refer to
chapter 9.)
If the servo motor can be driven
safely, execute the adaptive
tuning.
The machine is vibrating (resonating).
Adjust the machine resonance
suppression filter. (Refer to section
10.3.)
Display the cumulative feedback
pulses in "high speed monitor"
command of "monitor" menu on
MR Configurator, and check if its
numerical value is skipping.
Feedback pulses are being superposed
due to superimposed noise in the
encoder cable.
Please take countermeasures against
noise by laying the encoder cable
apart from power cables, etc.
Check if there is a backlash on
the machine part.
There is a backlash between the servo
motor and the machine (such as a gear
and coupling).
Adjust the backlash on the coupling
and the machine part.
Check the mounting part of the
servo motor.
The rigidity of the servo motor mounting
part is low.
Increase the rigidity of the mounting
part by methods, such as increasing
the board thickness and reinforcing the
part with ribs.
Summary of Contents for Melservo-J3 Series MR-J3-B
Page 19: ...10 MEMO ...
Page 55: ...1 36 1 FUNCTIONS AND CONFIGURATION MEMO ...
Page 61: ...2 6 2 INSTALLATION MEMO ...
Page 179: ...4 58 4 SIGNALS AND WIRING MEMO ...
Page 241: ...5 62 5 OPERATION MEMO ...
Page 357: ...10 16 10 SPECIAL ADJUSTMENT FUNCTIONS MEMO ...
Page 385: ...11 28 11 TROUBLESHOOTING MEMO ...
Page 397: ...12 12 12 OUTLINE DRAWINGS MEMO ...
Page 755: ...17 70 17 SPEED CONTROL OPERATION MEMO ...
Page 793: ...App 38 APPENDIX MEMO ...
Page 799: ...MEMO ...