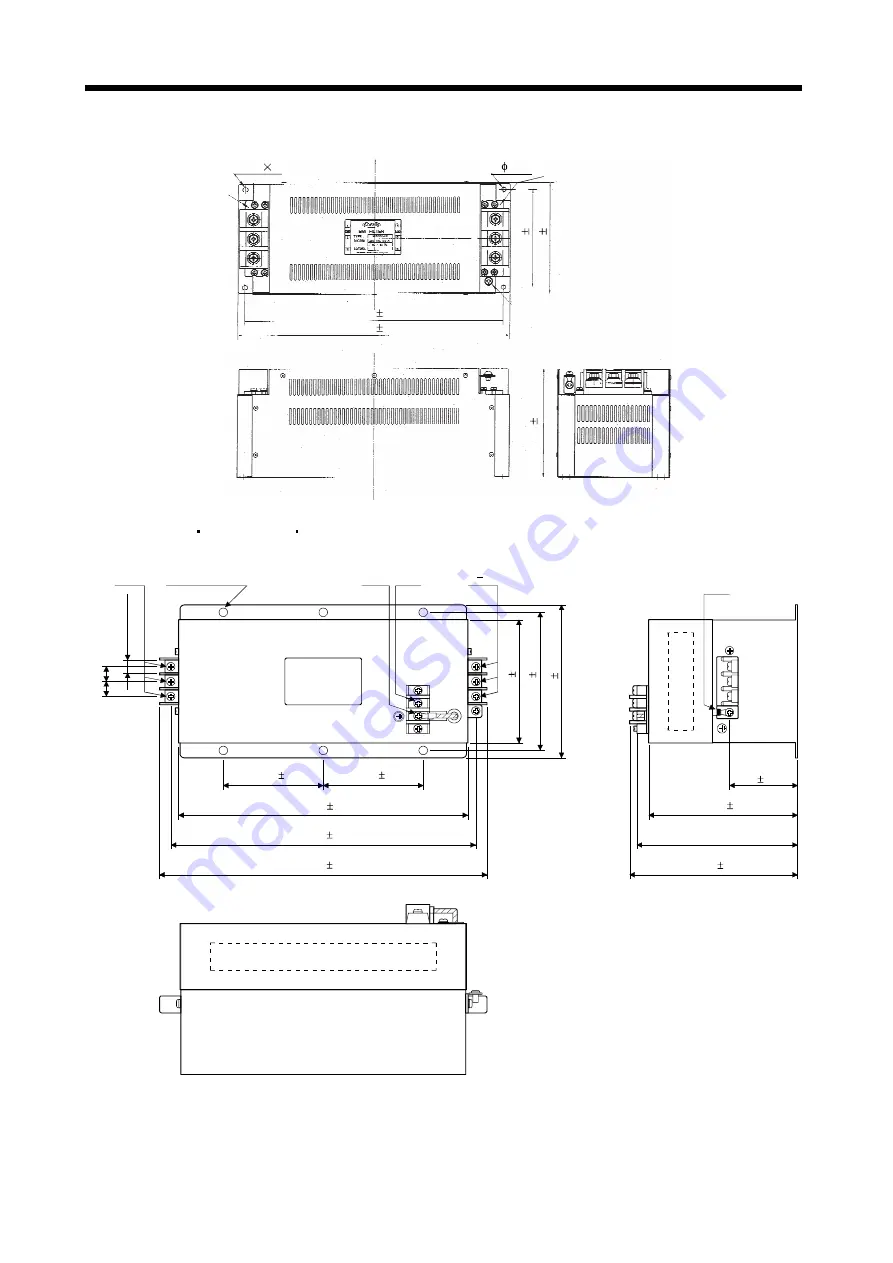
14 - 96
14. OPTIONS AND AUXILIARY EQUIPMENT
HF3100A-UN
2-6.5 8
M8
2- 6.5
14
5
1
16
5
3
M6
380 1
400 5
160
3
M8
TF3005C-TX TX3020C-TX TF3030C-TX
[Unit: mm]
290 2
100 1
308 5
332 5
A
pprox.
12.
2
3-M4
16
1
6
6-R3.25 length8
M4
M4
12
5
2
14
0
1
15
5
2
IN
150 2
Approx.67.5
3
Approx.160
170 5
M4
3 M4
100 1
Summary of Contents for Melservo-J3 Series MR-J3-B
Page 19: ...10 MEMO ...
Page 55: ...1 36 1 FUNCTIONS AND CONFIGURATION MEMO ...
Page 61: ...2 6 2 INSTALLATION MEMO ...
Page 179: ...4 58 4 SIGNALS AND WIRING MEMO ...
Page 241: ...5 62 5 OPERATION MEMO ...
Page 357: ...10 16 10 SPECIAL ADJUSTMENT FUNCTIONS MEMO ...
Page 385: ...11 28 11 TROUBLESHOOTING MEMO ...
Page 397: ...12 12 12 OUTLINE DRAWINGS MEMO ...
Page 755: ...17 70 17 SPEED CONTROL OPERATION MEMO ...
Page 793: ...App 38 APPENDIX MEMO ...
Page 799: ...MEMO ...