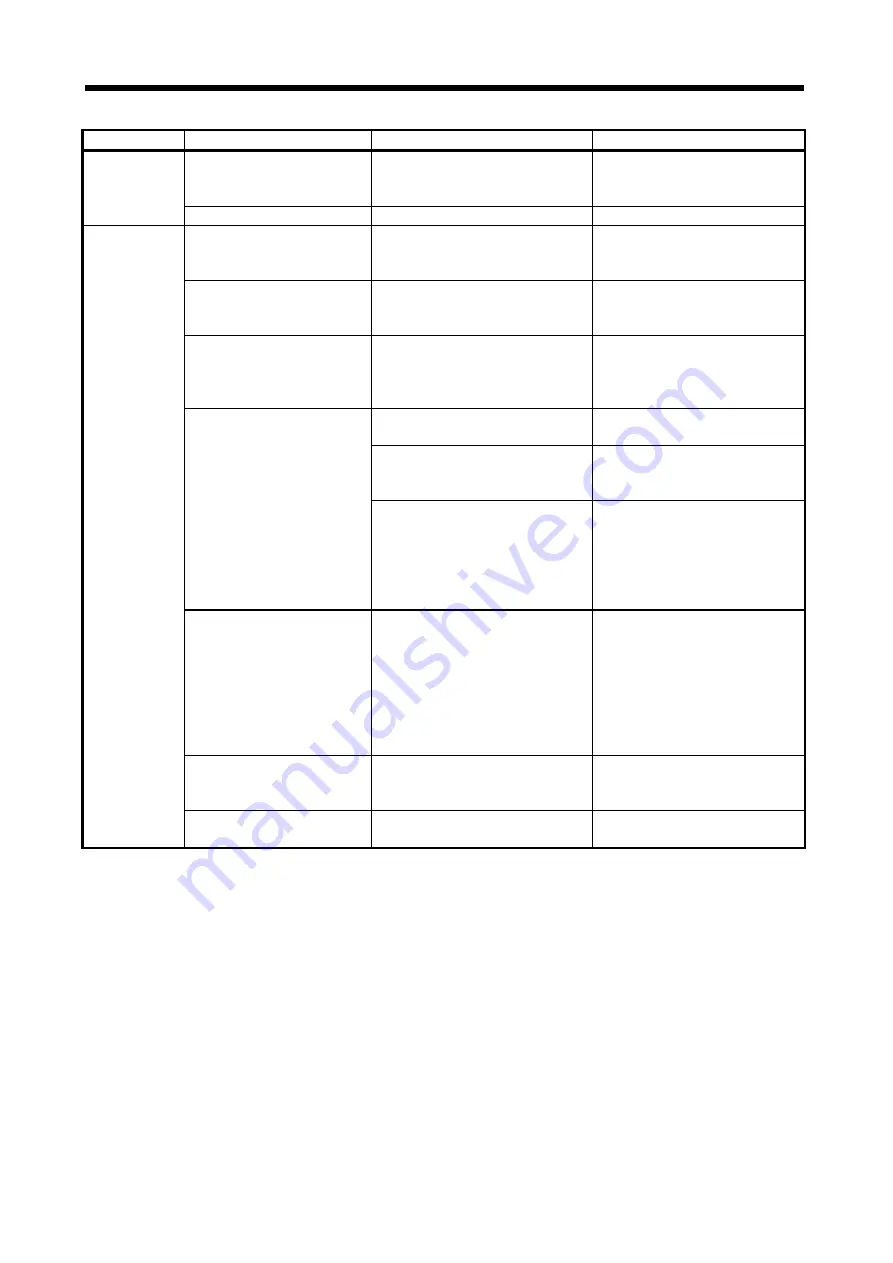
11 - 25
11. TROUBLESHOOTING
Description
Check method
Possible cause
Action
The position
deviates at the
home position
return.
Check the installation of the
proximity dog switch.
The position of the proximity dog is
deviated, or installation of the proximity
dog is faulty.
Adjust the installation of the proximity
dog switch.
Check the controller programs.
The controller programs are incorrect.
Review the controller programs.
The position
deviates during
operation after
the home
position return.
Check the servo alarm or
warning.
1. A servo alarm occurred.
2. The servo motor coasts due to servo
alarm.
Check the alarm content, and remove
its cause.
The command position and urrent
position do not match.
Forward rotation stroke end (LSP) or
reverse rotation stroke end (LSN) was
turned off. (A99 occurred).
Review the wiring of forward rotation
stroke end (LSP) and reverse rotation
stroke end (LSN).
"Cumulative feedback pulses ×
feed length multiplication" does
not match the actual machine
position.
1. A mechanical slip occurred.
2. The backlash of the machine part is
large.
Adjust the machine part.
Cumulative feedback pulses does
not match "Cumulative command
pulses × electronic gear setting"
value.
The power line was disconnected
temporarily.
Review the wiring.
1. The servo gain is low.
2. The auto tuning response is low.
3. Settling time is delayed.
Increase the auto tuning response, and
readjust the gain.
(Refer to chapter 9.)
1.Forward rotation stroke end (LSP) or
reverse rotation stroke end (LSN)
was turned off. (A99 occurred)
2. Clear (CR) and reset (RES) were
turned ON.
1. Review the wiring and sequence of
each signal.
2. Review the controller programs.
3. If a malfunction may occur due to
loud noise, increase the input filter
setting (parameter No.PD19).
1. If the servo motor can be driven
safely, repeat acceleration and
deceleration three times or
more to complete auto tuning.
2. Increase the auto tuning
response (parameter
No.PA09). (Except for the
manual mode)
The auto tuning response is low.
Increase the auto tuning response, and
readjust the gain. (Refer to chapter 9.)
For the geared servo motor,
check the setting of the electronic
gear (parameter No.PA06, PA07).
The reduction ratio is not calculated
correctly.
Review the setting of the reduction
ratio.
Check the point table setting,
selection, start timing, etc.
The setting of point tables and start
timing is incorrect.
1. Review the point table setting.
2. Review the controller programs.
Summary of Contents for Melservo-J3 Series MR-J3-B
Page 19: ...10 MEMO ...
Page 55: ...1 36 1 FUNCTIONS AND CONFIGURATION MEMO ...
Page 61: ...2 6 2 INSTALLATION MEMO ...
Page 179: ...4 58 4 SIGNALS AND WIRING MEMO ...
Page 241: ...5 62 5 OPERATION MEMO ...
Page 357: ...10 16 10 SPECIAL ADJUSTMENT FUNCTIONS MEMO ...
Page 385: ...11 28 11 TROUBLESHOOTING MEMO ...
Page 397: ...12 12 12 OUTLINE DRAWINGS MEMO ...
Page 755: ...17 70 17 SPEED CONTROL OPERATION MEMO ...
Page 793: ...App 38 APPENDIX MEMO ...
Page 799: ...MEMO ...