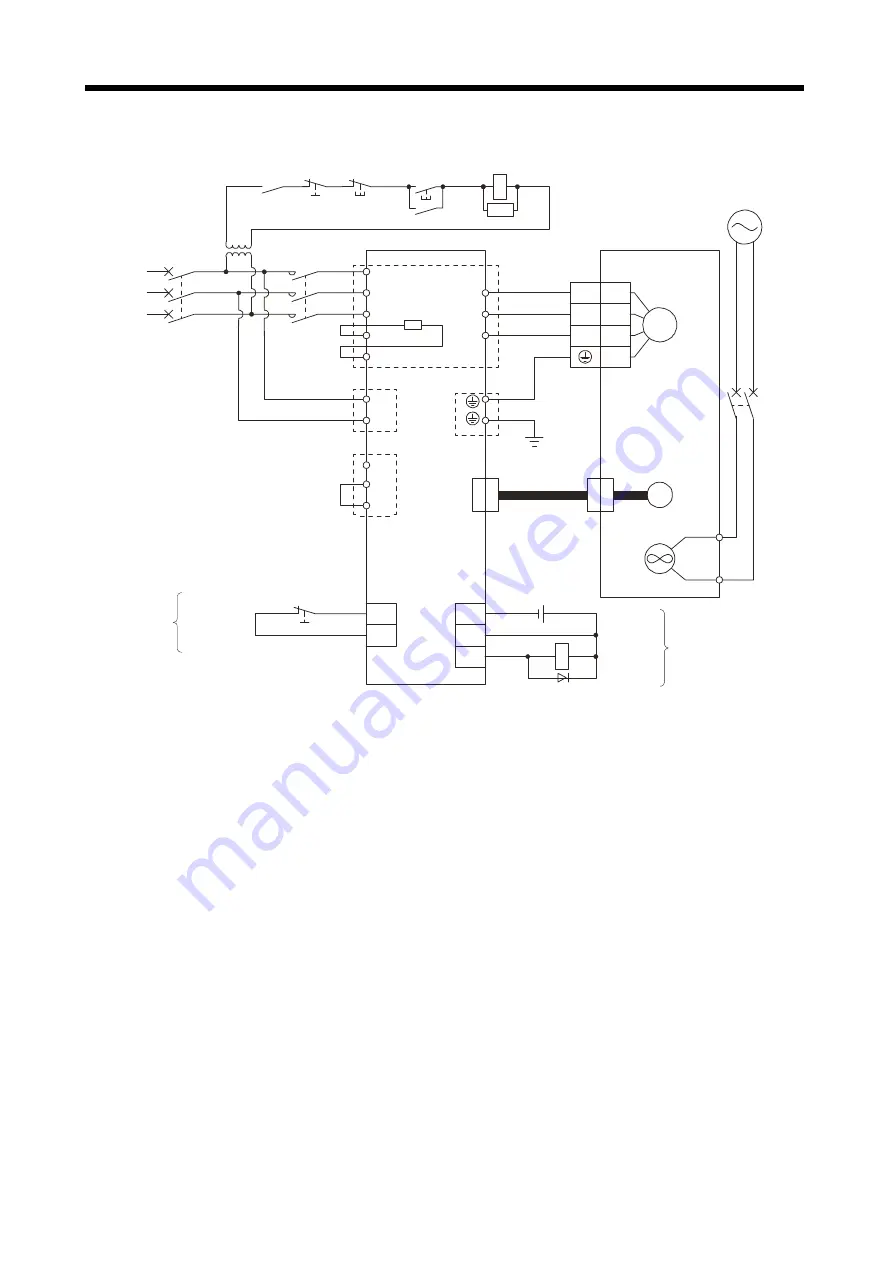
4 - 8
4. SIGNALS AND WIRING
(6) MR-J3-350T4 to MR-J3-700T4
ON
MC
C
P
U
V
W
U
V
W
2
3
4
1
M
24VDC
N
OFF
RA
DOCOM
DOCOM
Malfunction
MCCB
MC
SK
MC (Note 9)
(Note 2)
Servo amplifier
TE1
L
1
L
2
L
3
TE2
L
11
L
21
TE3
P
1
P
2
(Note 1)
(Note 4)
EMG
CN6
ALM
DICOM
CN6
(Note 4)
Cooling fan
BV
BU
Encoder
PE
(Note 5)
Motor
Servo motor
MCCB
3-phase
380 to
480VAC
(Note 6)
Stepdown
transformer
Malfunction
RA
Forced stop
(Note 8)
Built-in
regenerative
resistor
(Note 7)
Power supply
of cooling fan
Forced stop
(Note 8)
(Note 3)
Encode cable
Note 1. Always connect P
1
and P
2
. (Factory-wired.) When using the power factor improving DC reactor, refer to section 14.11.
2. When using the regenerative option, refer to section 14.2.
3. For encoder cable, use of the option cable is recommended. Refer to section 14.1 for selection of the cable.
4. For the sink I/O interface. For the source I/O interface, refer to section 4.8.3.
5. Refer to section 4.10.
6. Stepdown transformer is required for coil voltage of magnetic contactor more than 200V class.
7. A cooling fan is attached to the HA-LP6014 and the HA-LP701M4 servo motors. For power supply specification of the cooling
fan, refer to section 4.10.2 (3) (b).
8. Configure the circuit which shuts off main circuit power with external sequence at forced stop (EMG) off.
9. Use a magnetic contactor with an operation delay time (interval between current being applied to the coil until closure of
contacts) of 80ms or less.
Summary of Contents for Melservo-J3 Series MR-J3-B
Page 19: ...10 MEMO ...
Page 55: ...1 36 1 FUNCTIONS AND CONFIGURATION MEMO ...
Page 61: ...2 6 2 INSTALLATION MEMO ...
Page 179: ...4 58 4 SIGNALS AND WIRING MEMO ...
Page 241: ...5 62 5 OPERATION MEMO ...
Page 357: ...10 16 10 SPECIAL ADJUSTMENT FUNCTIONS MEMO ...
Page 385: ...11 28 11 TROUBLESHOOTING MEMO ...
Page 397: ...12 12 12 OUTLINE DRAWINGS MEMO ...
Page 755: ...17 70 17 SPEED CONTROL OPERATION MEMO ...
Page 793: ...App 38 APPENDIX MEMO ...
Page 799: ...MEMO ...