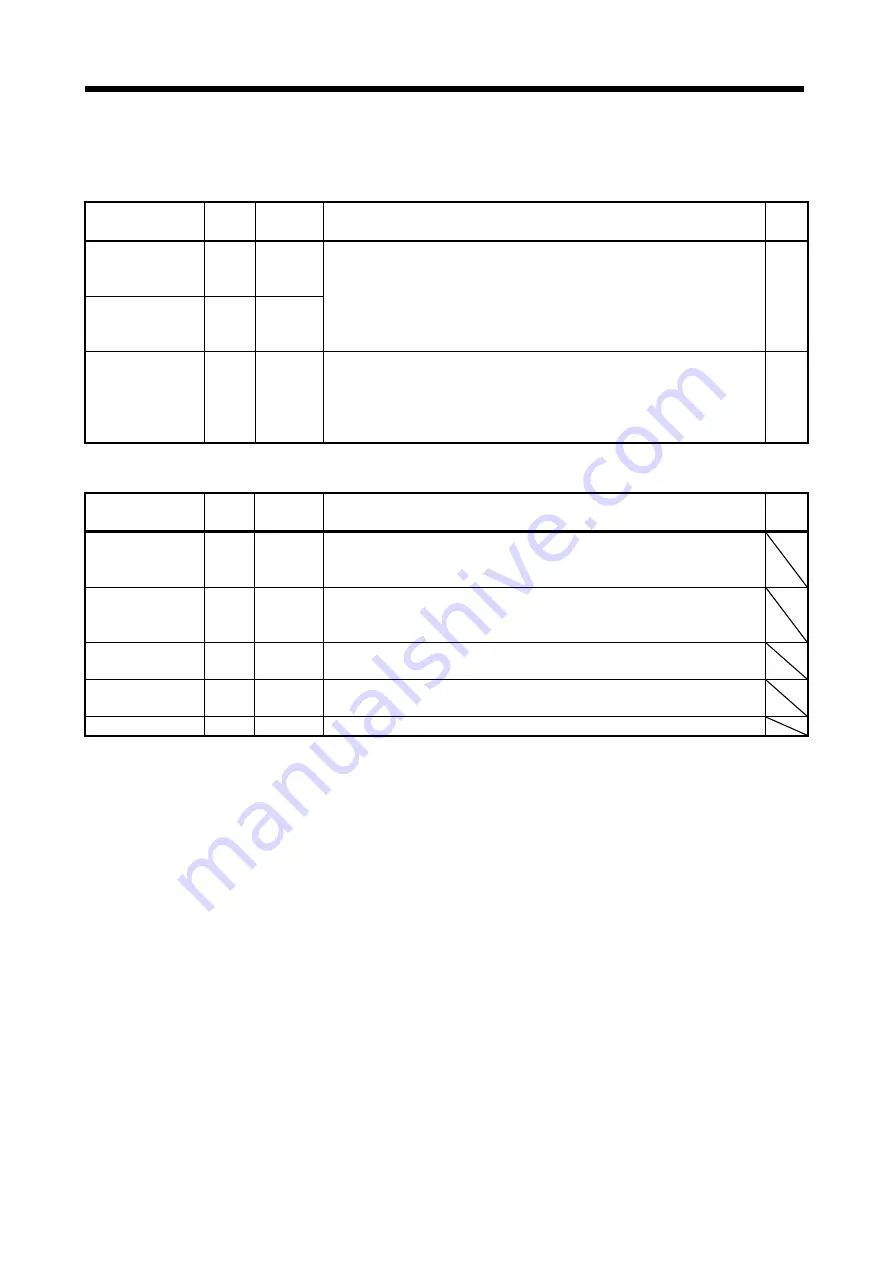
17 - 23
17. SPEED CONTROL OPERATION
(3) Output signal
For the output interface of each connector pin (symbols in I/O division column in the table), refer to section
4.8.2.
Signal name
Symbol
Connector
Pin No.
Functions/Applications
I/O
division
Encoder A-phase
pulse (differential line
driver)
LA
LAR
CN6-11
CN6-24
Outputs pulses per servo motor revolution set in parameter No.PA15 in the
differential line driver type.
In CCW rotation of the servo motor, the encoder B-phase pulse lags the encoder
A-phase pulse by a phase angle of
π
/2.
The relation between rotation direction and phase difference of the A-phase and
B-phase pulses can be changed with parameter No.PC19.
DO-2
Encoder B-phase
pulse (differential line
driver)
LB
LBR
CN6-12
CN6-25
Encoder Z-phase
pulse (differential line
driver)
LZ
LZR
CN6-13
CN6-26
The encoder zero-point signal is outputted in the differential line driver type. One
pulse is outputted per servo motor revolution. The signal turns on when the
zero-point position is reached. (negative logic)
The minimum pulse width is about 400
μ
s. For home position return using this
pulse, set the creep speed to 100 r/min or less.
DO-2
(4) Power supply
Signal name
Symbol
Connector
Pin No.
Functions/Applications
I/O
division
Digital I/F power
supply input
DICOM
CN6-5
Input 24VDC (24VDC±10% 150mA) for the I/O interface. The power supply
capacity varies with the number of I/O interface points to be used.
For the sink interface, c of the 24VDC external power supply.
Digital I/F common
DOCOM CN6-17
Common terminal of input signals such as DOG and EMG of the servo amplifier.
This is separated from LG.
For the source interface, c of the 24VDC external power supply.
MR-HDP01 open
collector power input
OPC
CN6-18
Not used in speed control operation.
Control common
LG
CN6-23
Common terminal for the encoder pulses (differential line driver) (LA, LAR, LB,
LBR, LZ, LZR).
Shield
SD
Plate
Connect the external conductive portion of the shielded cable.
17.3.2 Detailed description of signals (devices)
(1) Forward rotation start and reverse rotation start
(a) Configure a sequence so that the forward rotation start (RYn1) or the reverse rotation start (RYn2) turns
on after the main circuit is established. Each signal is invalid if it turns on before the main circuit is
established. Normally, it is interlocked with the ready signal (RD).
(b) A start in the servo amplifier is made when the forward rotation start (RYn1) or the reverse rotation start
(RYn2) turns on. The delay time of the servo amplifier's internal processing is max. 3ms. The delay time
of other devices is max. 10ms.
(c) When a programmable controller is used, the on time of the forward rotation start (RYn1) or the reverse
rotation start (RYn2) should be 6ms or longer to prevent a malfunction.
(d) During operation, neither the forward rotation start (RYn1) nor reverse rotation start (RYn2) is accepted.
Summary of Contents for Melservo-J3 Series MR-J3-B
Page 19: ...10 MEMO ...
Page 55: ...1 36 1 FUNCTIONS AND CONFIGURATION MEMO ...
Page 61: ...2 6 2 INSTALLATION MEMO ...
Page 179: ...4 58 4 SIGNALS AND WIRING MEMO ...
Page 241: ...5 62 5 OPERATION MEMO ...
Page 357: ...10 16 10 SPECIAL ADJUSTMENT FUNCTIONS MEMO ...
Page 385: ...11 28 11 TROUBLESHOOTING MEMO ...
Page 397: ...12 12 12 OUTLINE DRAWINGS MEMO ...
Page 755: ...17 70 17 SPEED CONTROL OPERATION MEMO ...
Page 793: ...App 38 APPENDIX MEMO ...
Page 799: ...MEMO ...