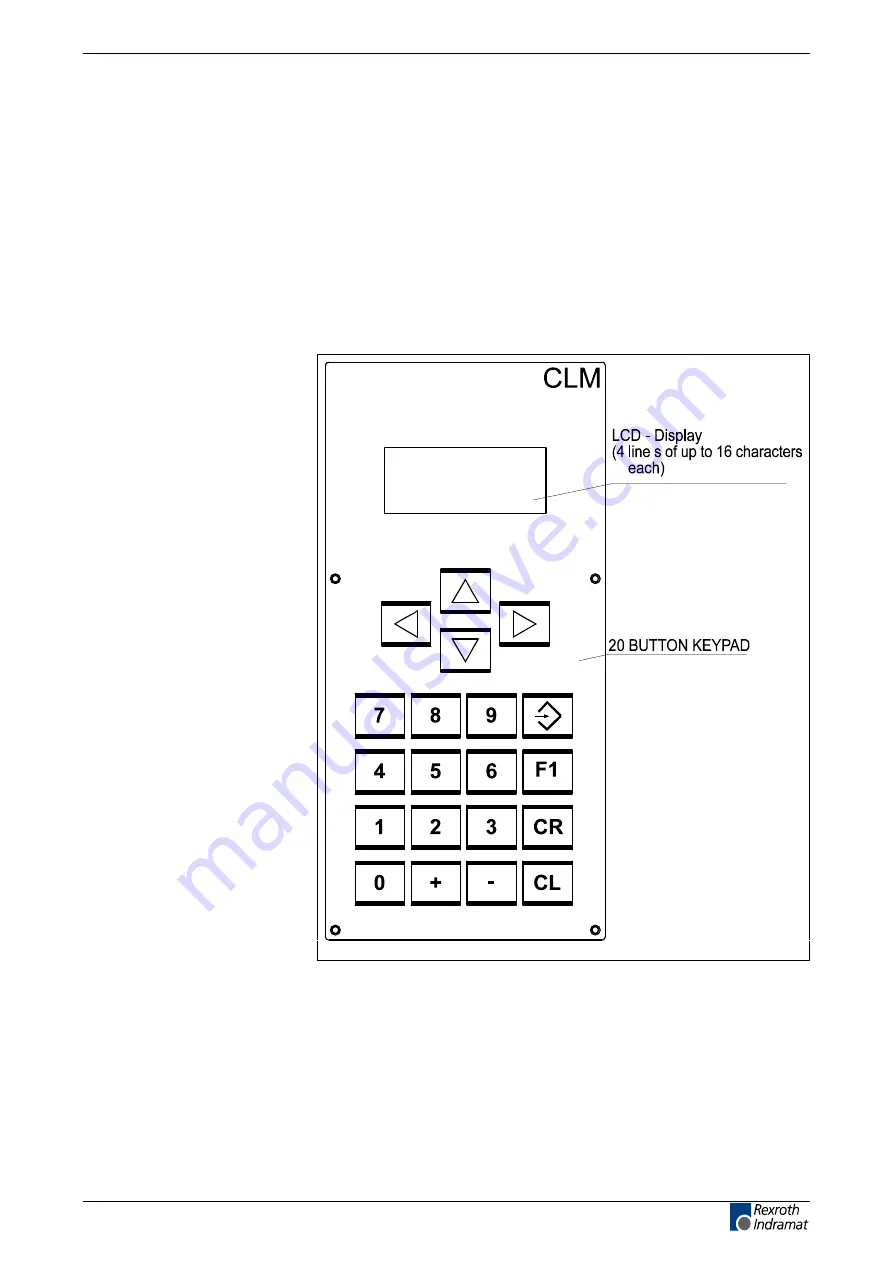
CLM01.4-LAP-01VRS
Display and Operating Devices
4-1
DOK-CONTRL-CLM01.4LAP1-FK01-EN-P
4
Display and Operating Devices
4.1
General Information about the CTA
The CTA, which has a liquid-crystal display (LCD), is located on the front
panel of the CLM.
The display consists of 4 lines of 16 characters each. Below the display is
a keypad with pressure-sensitive keys for data entry and manipulation of
the display options.
A cursor blinks at the location where an input is to be made. The cursor
automatically moves to the next position after a data key is pressed.
42_front_AE.WMF
Fig. 4-1: Display / Keypad Module
Summary of Contents for CLM1.4
Page 117: ...7 20 Functions CLM01 4 LAP 01VRS DOK CONTRL CLM01 4LAP1 FK01 EN P Notes...
Page 205: ...9 42 Interfaces CLM01 4 LAP 01VRS DOK CONTRL CLM01 4LAP1 FK01 EN P Notes...
Page 213: ...10 8 Command Communications CLM01 4 LAP 01VRS DOK CONTRL CLM01 4LAP1 FK01 EN P Notes...
Page 233: ...11 20 Diagnostic Messages CLM01 4 LAP 01VRS DOK CONTRL CLM01 4LAP1 FK01 EN P Notes...
Page 272: ......
Page 273: ...Printed in the U S A Barcode...