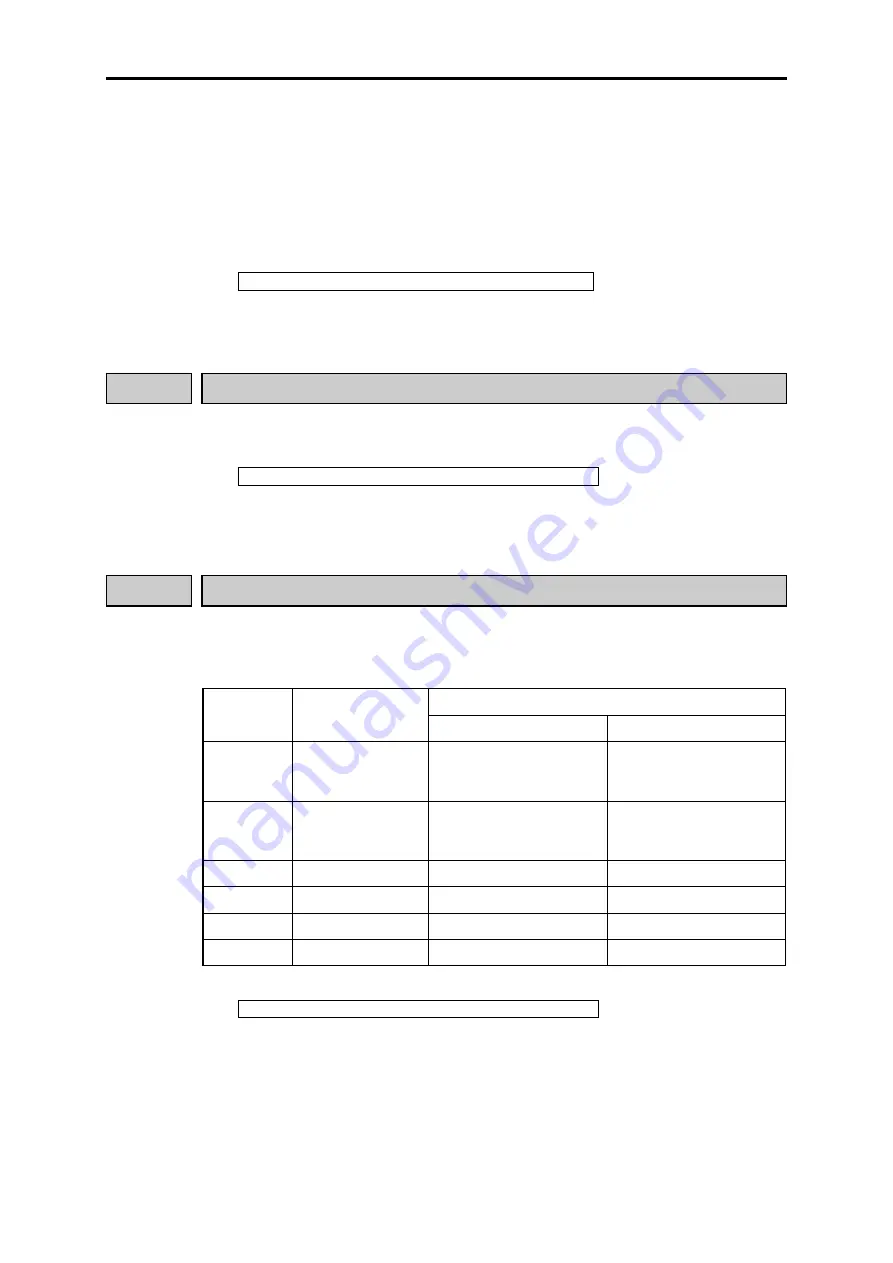
6-348
(Note 6) These items appear when J501 or J504 (External PID control 1)
≠
0.
(Note 7) These items appear when J601 (External PID control 2)
≠
0.
(Note 8) This item appears when J601 (External PID control 1)
≠
0 and
%/EPID2
("Cancel external PID
control 2") is assigned to any digital input terminal.
(Note 9) These items appear when J651 (External PID control 3)
≠
0.
(Note 10) This item appears when J651 (External PID control 3)
≠
0 and
%/EPID3
("Cancel external PID
control 3") is assigned to any digital input terminal.
The monitor items can be selected easily in Programming mode as follows.
PRG > 1(Start-up) > 4(Disp Setting) > 2(Main Monitor)
For detailed setting procedure, refer to Chapter 5, Section 5.6.2.4 "Specifying the
running status item to be monitored."
K11
Main Monitor (Speed monitor item)
(Refer to K10.)
For details about the speed monitor items, refer to the description of K10.
The monitor items can be selected easily in Programming mode as follows.
PRG > 1(Start-up) > 4(Disp Setting) > 3(Speed Monitor)
For detailed setting procedure, refer to Chapter 5, Section 5.6.2.4 "Specifying the
running status item to be monitored."
K12
Main Monitor (Display when stopped)
K12 specifies whether the specified value (data = 0) or the output value (data = 1) to be
displayed on the main monitor when the inverter is stopped. The monitored item depends on
the K11 (Main monitor, Speed monitor item) setting as shown below.
What to be displayed when the inverter stopped
Data for K11
Monitored item
K12 = 0: Specified value
K12 = 1: Output value
1 Output
frequency
1
(before slip
compensation)
Reference frequency
Output frequency 1
(before slip compensation)
2 Output
frequency
2
(after slip
compensation)
Reference frequency
Output frequency 2
(after slip compensation)
3
Reference frequency Reference frequency
Reference frequency
4 Motor
speed Reference
motor speed
Motor speed
5
Load shaft speed
Reference load shaft speed
Load shaft speed
8
Display speed (%)
Reference display speed
Display speed
The monitor items can be selected easily in Programming mode as follows.
PRG > 1(Start-up) > 4(Disp Setting) > 3(Speed Monitor)
For detailed setting procedure, refer to Chapter 5, Section 5.6.2.4 "Specifying the
running status item to be monitored."
Summary of Contents for FRENIC-AQUA series
Page 1: ...MEHT538b...
Page 2: ...User s Manual...
Page 13: ......
Page 15: ......
Page 33: ......
Page 35: ......
Page 61: ...2 26 Figure D Figure E NC No connection Do not make wiring NC NC...
Page 63: ...2 28 Figure J Figure K Charging lamp Charging lamp Viewed from A...
Page 83: ...2 48 Unit mm FRN45 to 55AQ1 4...
Page 84: ...2 9 External Dimensions 2 49 Chap 2 SPECIFICATIONS Unit mm FRN75 to 90AQ1 4...
Page 85: ...2 50 Unit mm FRN110AQ1S 4 FRN132AQ1S 4 FRN160AQ1S 4 FRN200AQ1S 4...
Page 87: ...2 52 Unit mm FRN500AQ1S 4 FRN630AQ1S 4 FRN710AQ1S 4...
Page 88: ...2 9 External Dimensions 2 53 Chap 2 SPECIFICATIONS 2 9 2 Keypad Unit mm Panel cutout...
Page 95: ......
Page 140: ...4 4 Options 4 33 Chap 4 SELECTING PERIPHERAL EQUIPMENT...
Page 279: ......
Page 281: ......
Page 341: ...6 60 Example of Thermal Overload Detection Characteristics...
Page 637: ......
Page 639: ......
Page 651: ...7 12 Figure 7 7 Terminal FM2 Output Selector...
Page 653: ......
Page 663: ......
Page 665: ......
Page 699: ......
Page 717: ......
Page 719: ......
Page 733: ......
Page 749: ......
Page 751: ...MEHT537 Phone 81 3 5435 7058 Fax 81 3 5435 7420 Printed in Japan 2012 08 H12b b12 CM00FOLS...