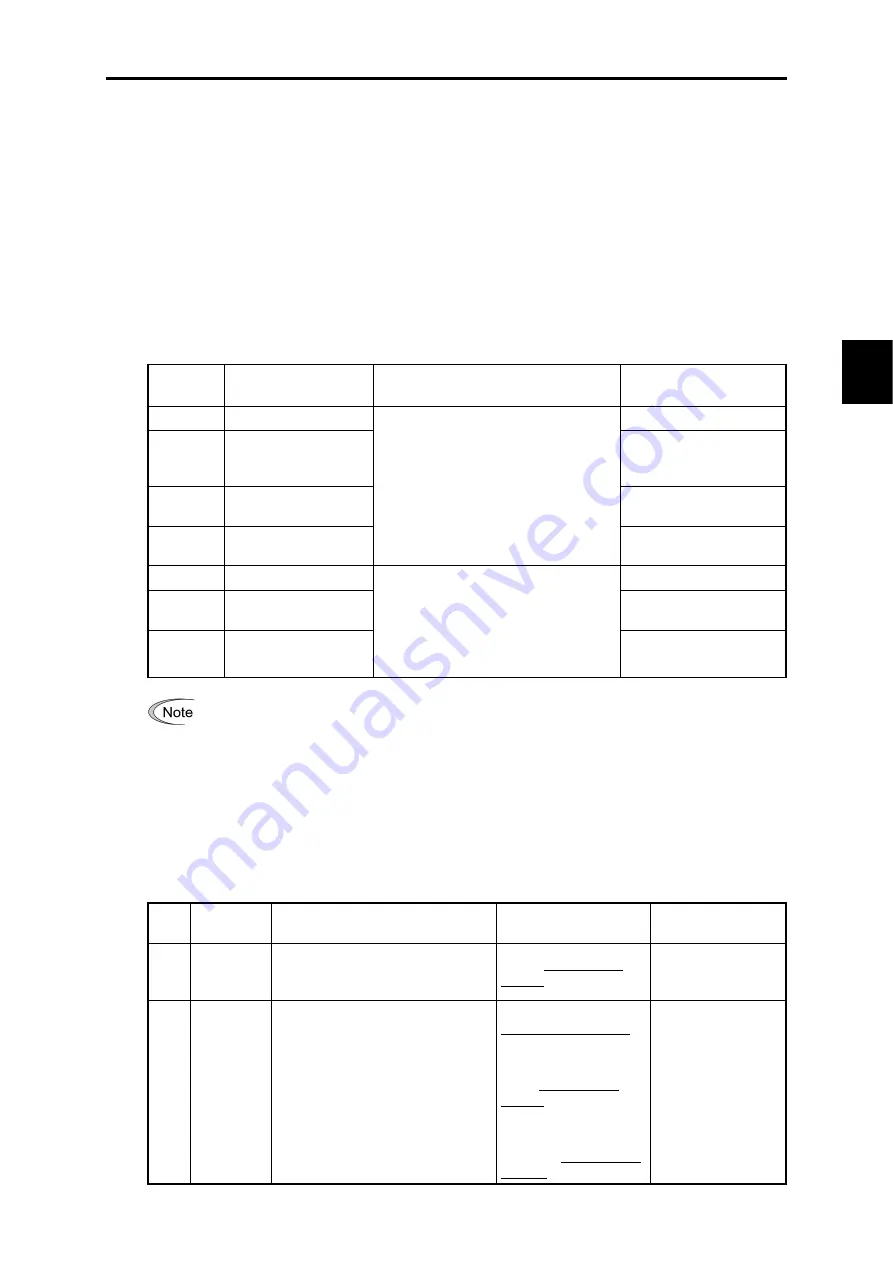
5.7 Alarm Mode
5-95
Chap. 5
PR
EP
AR
A
T
IO
N AND
TEST
RUN
5.7.9
Function code basic settings and tuning < 2 >
Under the V/f control (F42 = 0 or 2) or dynamic torque vector control (F42 = 1), any of the following
cases requires configuring the basic function codes given below and auto-tuning.
- Driving a non-Fuji motor or non-standard motor
- Driving a Fuji general-purpose motor, provided that the wiring distance between the inverter and
motor is long or a reactor is connected
Configure the function codes listed below according to the motor ratings and your machinery design
values. For the motor ratings, check the ratings printed on the motor's nameplate. For your machinery
design values, ask system designers about them.
For details on how to modify the function code data, see Section 5.6.3.1 "Setting up function
codes."
Function
code
Name Function
code
data Factory
default
F04
Base frequency 1
50.0 (Hz)
F05
Rated voltage at base
frequency 1
Asia: 415
(V)
Europe: 400 (V)
China: 380
(V)
P02
Motor 1
(Rated capacity)
Nominal applied motor
capacity
P03
Motor 1
(Rated current)
Motor ratings
(printed on the nameplate of the motor)
Rated current of nominal
applied motor
F03
Maximum frequency 1
50.0 (Hz)
F07
Acceleration time 1
(Note)
20.00 (s)
F08
Deceleration time 1
(Note)
Machinery design values
(Note)
For a test-driving of the motor, increase
values so that they are longer than your
machinery design values. If the specified time is
short, the inverter may not run the motor
properly.
20.00 (s)
When accessing the function code P02, take into account that changing the P02* data
automatically updates the data of the function codes P03, P06 to P08, and H46.
Tuning procedure
(1) Selection of tuning type
Check the situation of the machinery and select "Tuning with the motor stopped (P04 = 1)" or "Tuning
with the motor running (P04 = 2)." For the latter tuning, adjust the acceleration and deceleration times
(F07 and F08) and specify the rotation direction that matches the actual rotation direction of the
machinery.
P04
data
Tuning type
Motor parameters subjected to tuning
Tuning
Select under the
following conditions
1
Tune while
the motor
stops
Primary resistance (%R1) (P07)
Leakage reactance (%X) (P08)
Tuning with the motor
stopped.
Cannot rotate the
motor.
2
Tune while
the motor is
rotating
under V/f
control
No-load current (P06)
Primary resistance (%R1) (P07)
Leakage reactance (%X) (P08)
Tuning the %R1 and %X,
with the motor stopped.
Tuning the no-load current
and magnetic saturation
factor, with the motor
running at 50% of the base
frequency.
Tuning the rated slip
frequency, with the motor
stopped.
Can rotate the motor,
provided that it is safe.
Note that little load
should be applied
during tuning. Tuning
with load applied
decreases the tuning
accuracy.
Summary of Contents for FRENIC-AQUA series
Page 1: ...MEHT538b...
Page 2: ...User s Manual...
Page 13: ......
Page 15: ......
Page 33: ......
Page 35: ......
Page 61: ...2 26 Figure D Figure E NC No connection Do not make wiring NC NC...
Page 63: ...2 28 Figure J Figure K Charging lamp Charging lamp Viewed from A...
Page 83: ...2 48 Unit mm FRN45 to 55AQ1 4...
Page 84: ...2 9 External Dimensions 2 49 Chap 2 SPECIFICATIONS Unit mm FRN75 to 90AQ1 4...
Page 85: ...2 50 Unit mm FRN110AQ1S 4 FRN132AQ1S 4 FRN160AQ1S 4 FRN200AQ1S 4...
Page 87: ...2 52 Unit mm FRN500AQ1S 4 FRN630AQ1S 4 FRN710AQ1S 4...
Page 88: ...2 9 External Dimensions 2 53 Chap 2 SPECIFICATIONS 2 9 2 Keypad Unit mm Panel cutout...
Page 95: ......
Page 140: ...4 4 Options 4 33 Chap 4 SELECTING PERIPHERAL EQUIPMENT...
Page 279: ......
Page 281: ......
Page 341: ...6 60 Example of Thermal Overload Detection Characteristics...
Page 637: ......
Page 639: ......
Page 651: ...7 12 Figure 7 7 Terminal FM2 Output Selector...
Page 653: ......
Page 663: ......
Page 665: ......
Page 699: ......
Page 717: ......
Page 719: ......
Page 733: ......
Page 749: ......
Page 751: ...MEHT537 Phone 81 3 5435 7058 Fax 81 3 5435 7420 Printed in Japan 2012 08 H12b b12 CM00FOLS...