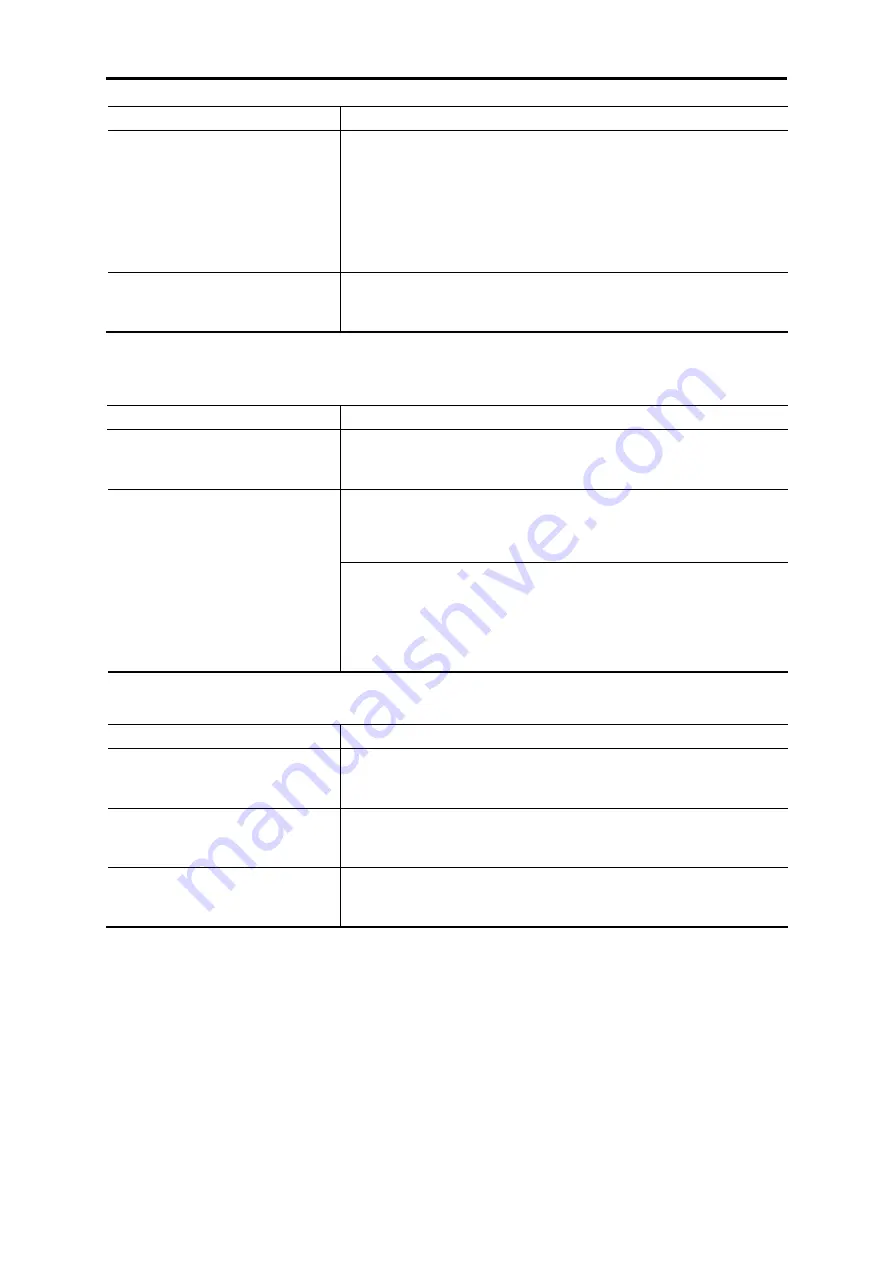
9-28
Possible Causes
What to Check and Suggested Measures
(7) The output frequency is limited
by the torque limiter.
Check whether data of torque limiter related function codes (F40, F41,
E16 and E17) is correctly configured and the
TL2
/
TL1
terminal
command ("Select torque limiter level 2/1") is correct.
Î
Correct the data of F40, F41, E16 and E17 or reset them to the
factory defaults.
Î
Set the
TL2
/
TL1
correctly.
Î
Increase the acceleration/deceleration time (F07, F08, E10 through
E15).
(8) The specified acceleration or
deceleration time was
incorrect.
Check the terminal commands
RT1
and
RT2
for acceleration/
deceleration times.
Î
Correct the
RT1
and
RT2
settings.
[ 7 ] The motor does not restart even after the power recovers from a
momentary power failure.
Possible Causes
What to Check and Suggested Measures
(1) The data of function code F14
is either "0," "1," or "2."
Check if an undervoltage trip (LV
)
occurs.
Î
Change the data of function code F14 (Restart mode after
momentary power failure (Mode selection)) to "3," "4," or "5."
Check the input signal with Menu "I/O Checking" using the keypad.
Î
Check the power recovery sequence with an external circuit. If
necessary, consider the use of a relay that can keep the run
command ON.
(2) The run command remains
OFF even after the power has
been restored.
In 3-wire operation, the power to the control printed circuit board
(control PCB) has been shut down once because of a long momentary
power failure time, or the "Enable 3-wire operation" signal
HOLD
has
been turned OFF once.
Î
Change the design or the setting so that a run command can be
issued again within 2 seconds after the power has been restored.
[ 8 ] The motor abnormally heats up.
Possible Causes
What to Check and Suggested Measures
(1) Excessive torque boost
specified.
Check whether decreasing the torque boost (F09) decreases the output
current but does not stall the motor.
Î
If no stall occurs, decrease the torque boost (F09).
(2) Continuous running in
extremely slow speed.
Check the running speed of the inverter.
Î
Change the speed setting or replace the motor with a motor
exclusively designed for inverters.
(3) Overload.
Measure the inverter output current.
Î
Reduce the load (For fans or pumps, decrease the frequency limiter
value (F15).) (In winter, the load tends to increase.)
Summary of Contents for FRENIC-AQUA series
Page 1: ...MEHT538b...
Page 2: ...User s Manual...
Page 13: ......
Page 15: ......
Page 33: ......
Page 35: ......
Page 61: ...2 26 Figure D Figure E NC No connection Do not make wiring NC NC...
Page 63: ...2 28 Figure J Figure K Charging lamp Charging lamp Viewed from A...
Page 83: ...2 48 Unit mm FRN45 to 55AQ1 4...
Page 84: ...2 9 External Dimensions 2 49 Chap 2 SPECIFICATIONS Unit mm FRN75 to 90AQ1 4...
Page 85: ...2 50 Unit mm FRN110AQ1S 4 FRN132AQ1S 4 FRN160AQ1S 4 FRN200AQ1S 4...
Page 87: ...2 52 Unit mm FRN500AQ1S 4 FRN630AQ1S 4 FRN710AQ1S 4...
Page 88: ...2 9 External Dimensions 2 53 Chap 2 SPECIFICATIONS 2 9 2 Keypad Unit mm Panel cutout...
Page 95: ......
Page 140: ...4 4 Options 4 33 Chap 4 SELECTING PERIPHERAL EQUIPMENT...
Page 279: ......
Page 281: ......
Page 341: ...6 60 Example of Thermal Overload Detection Characteristics...
Page 637: ......
Page 639: ......
Page 651: ...7 12 Figure 7 7 Terminal FM2 Output Selector...
Page 653: ......
Page 663: ......
Page 665: ......
Page 699: ......
Page 717: ......
Page 719: ......
Page 733: ......
Page 749: ......
Page 751: ...MEHT537 Phone 81 3 5435 7058 Fax 81 3 5435 7420 Printed in Japan 2012 08 H12b b12 CM00FOLS...