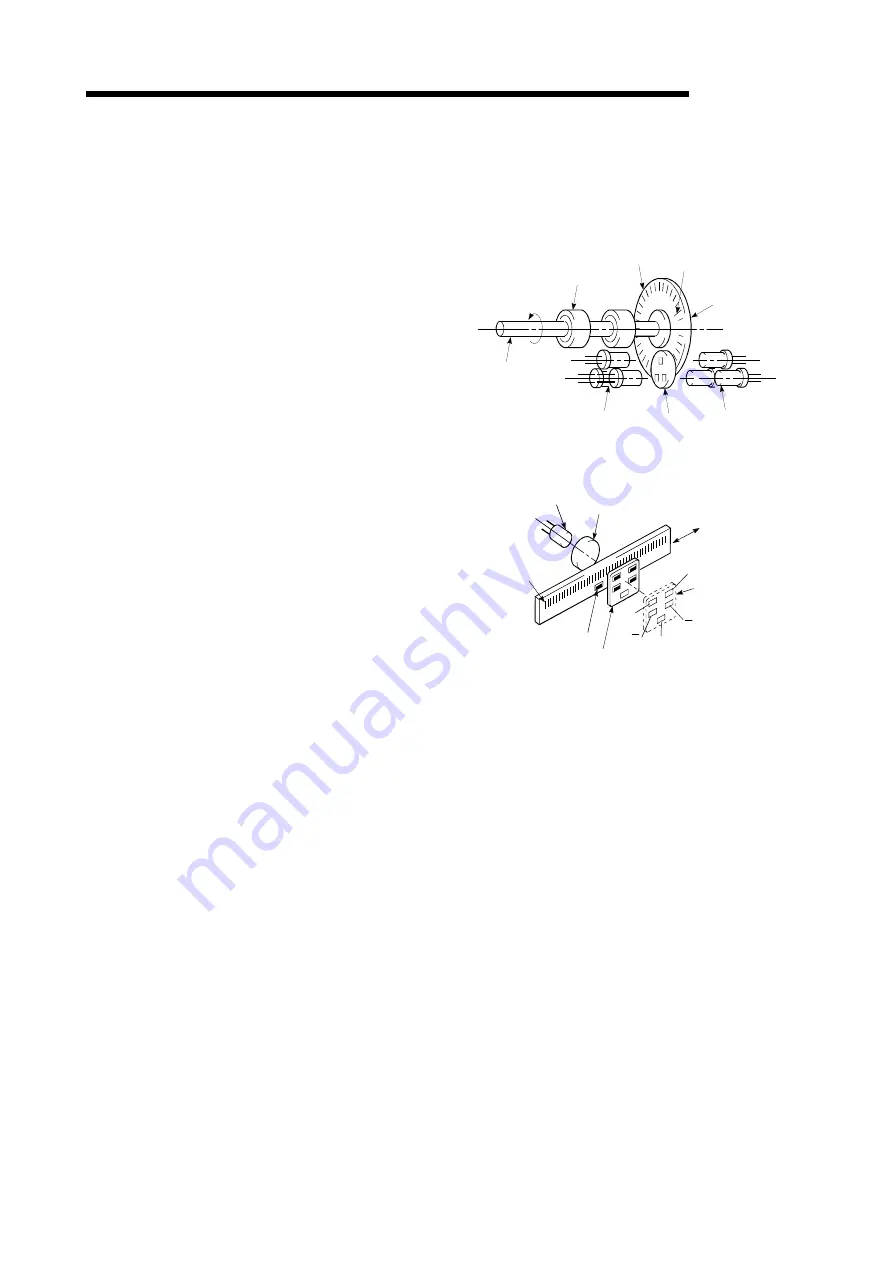
Appendix - 121
MELSEC-Q
APPENDICES
DYNAMIC BRAKE
When protection circuits operate due to power
failures, emergency stops (EMG signal) etc.,
this function is used to short-circuit between
servomotor terminals via a resistor, thermally
consume the rotation energy, and cause a
sudden stop without allowing coasting of the
motor.
Braking power is generated by
electromagnetic brakes only when running
motors with which a large brake torque can be
obtained. Because electromagnetic brakes
have no holding power, they are used in
combination with mechanical brakes to prevent
dropping of the vertical axis.
ELECTROMAGNETIC BRAKE
This function is supplied on motors with
electromagnetic brakes. Electromagnetic
brakes are used to prevent slipping during
power failures and faults when driving a
vertical axis, or as a protective function when
the machine is stopped.
These brakes are activated when not excited.
ELECTRONIC GEAR
This function electrically increases/decreases
the command pulses from the pulse command
module by 1/50 to 50-fold. Thus, the
positioning speed and movement amount can
be controlled by the electronic gear ratio
magnification.
EMERGENCY STOP
Emergency stops cannot be carried out by the
QD75, so a method of shutting OFF the servo
side power supply from outside the
programmable controller, etc., must be
considered.
ENCODER
This device turns the input data into a binary
code of 1 (ON) and 0 (OFF). A type of pulse
generator.
A
B
Z
Ball bearing
For the main
signal
For the zero
point signal
Input axis
Code disk
Photoreceptor
(phototransistor)
Index
scale
Light source
(light-emitting diode)
Rotary encoder
a
a
b
z
b
Light source
(LED)
Collimator lens
Main scale
Photoreceptor
(photodiode)
Reference
zero point Index
scale
Linear encoder
ERROR CORRECTION
If a dimension error occurs in the machine,
and that error is actually smaller or larger than
1m (3.28feet) in spite of a 1m (3.28feet)
command being issued from the QD75, that
error amount will be compensated. For
example, when the error is actually smaller
than 1m (3.28feet), the remaining distance to
1m (3.28feet) is fed, and the correct 1m
(3.28feet) of positioning is carried out.
ERROR RESET
This resets error of axis. Note that if the cause
of the error is not eliminated at that time, the
error will occur again.
Summary of Contents for Melsec-Q QD75D1
Page 1: ......
Page 2: ......
Page 22: ...A 20 MEMO ...
Page 24: ...MEMO ...
Page 41: ...1 17 MELSEC Q 1 PRODUCT OUTLINE MEMO ...
Page 48: ...1 24 MELSEC Q 1 PRODUCT OUTLINE MEMO ...
Page 60: ...2 12 MELSEC Q 2 SYSTEM CONFIGURATION MEMO ...
Page 137: ...5 33 MELSEC Q 5 DATA USED FOR POSITIONING CONTROL MEMO ...
Page 232: ...5 128 MELSEC Q 5 DATA USED FOR POSITIONING CONTROL MEMO ...
Page 252: ...6 20 MELSEC Q 6 SEQUENCE PROGRAM USED FOR POSITIONING CONTROL ...
Page 253: ...6 21 MELSEC Q 6 SEQUENCE PROGRAM USED FOR POSITIONING CONTROL ...
Page 278: ...6 46 MELSEC Q 6 SEQUENCE PROGRAM USED FOR POSITIONING CONTROL MEMO ...
Page 292: ...MEMO ...
Page 436: ...9 120 MELSEC Q 9 MAJOR POSITIONING CONTROL MEMO ...
Page 464: ...10 28 MELSEC Q 10 HIGH LEVEL POSITIONING CONTROL MEMO ...
Page 638: ...14 24 MELSEC Q 14 DEDICATED INSTRUCTIONS MEMO ...
Page 647: ...15 9 MELSEC Q 15 TROUBLESHOOTING MEMO ...
Page 686: ...15 48 MELSEC Q 15 TROUBLESHOOTING MEMO ...
Page 839: ...Appendix 153 MELSEC Q APPENDICES 6 QD75D4N 90 23 27 4 12 98 4 46 Unit mm ...
Page 840: ...Appendix 154 MELSEC Q APPENDICES 7 QD75P1 QD75P2 QD75P4 27 4 23 98 90 4 46 unit mm ...
Page 841: ...Appendix 155 MELSEC Q APPENDICES 8 QD75D1 QD75D2 QD75D4 27 4 23 90 12 98 4 46 unit mm ...
Page 842: ...Appendix 156 MELSEC Q APPENDICES MEMO ...
Page 857: ......
Page 858: ......