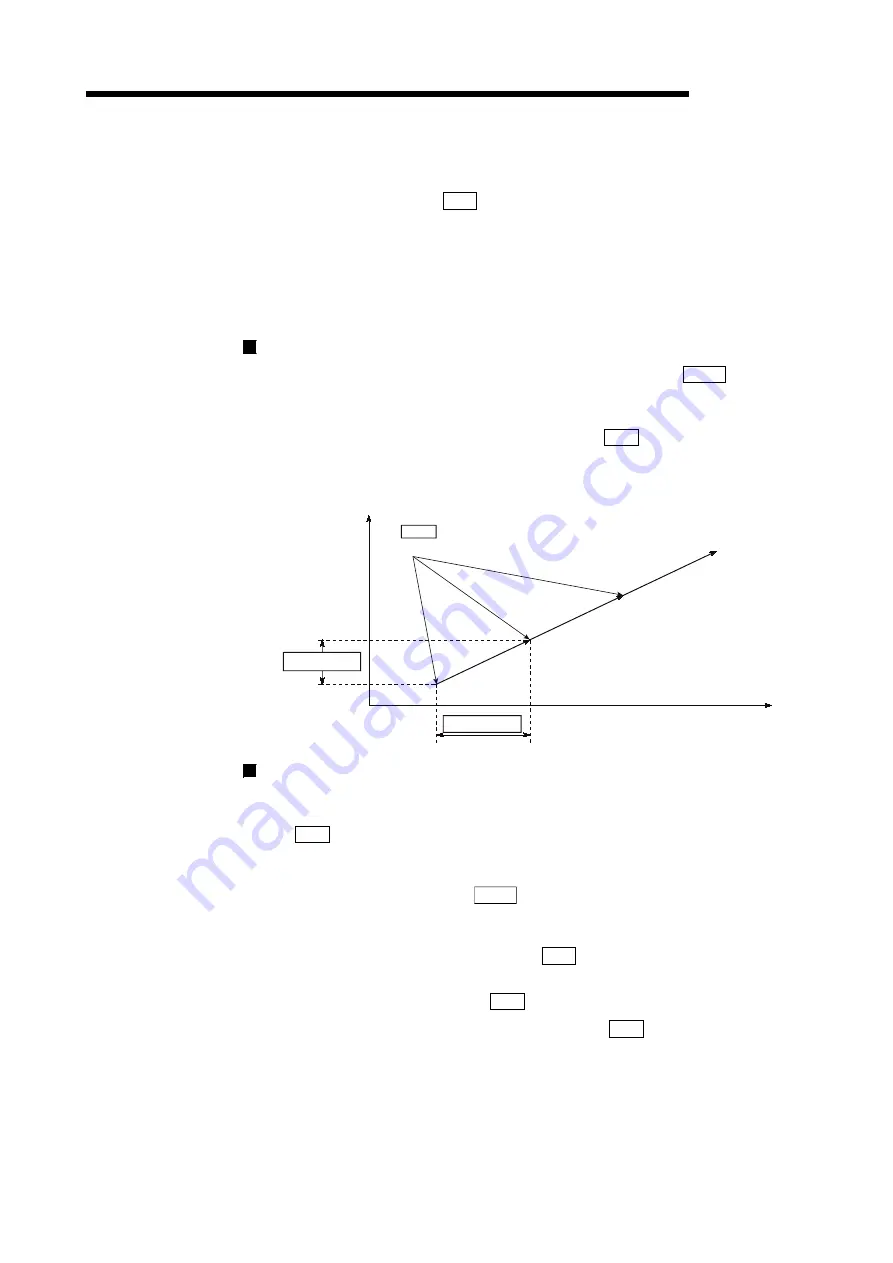
9 - 46
MELSEC-Q
9 MAJOR POSITIONING CONTROL
9.2.7 2-axis fixed-feed control (interpolation)
In "2-axis fixed-feed control" ("
Da.2
Control system" = fixed-feed 2), two motors are
used to carry out fixed-feed control in a linear path while carrying out interpolation for
the axis directions set in each axis.
In fixed-feed control, any remainder of the movement amount designated in the
positioning data is rounded down if less than that required for control accuracy to
output the same amount of pulses.
(Refer to Section 9.1.6 "Interpolation control" for details on interpolation control.)
Operation chart
In incremental system 2-axis fixed-feed control, the addresses (
Md.20
Current
feed value) of the current stop position (start addresses) of both axes are set to
"0". Linear interpolation positioning is then carried out from that position to a
position at the end of the movement amount set in "
Da.6
Positioning
address/movement amount". The movement direction is determined by the sign of
the movement amount.
Designated movement
amount
Designated movement
amount
(0,0)
(0,0)
(0,0)
X axis
Y axis
" Md. 20 Current feed value" of each axis
is set to "0" at the positioning start
Restrictions
(1) An axis error "Continuous path control not possible" (error code: 516) will
occur and the operation cannot start if "continuous path control" is set in
"
Da.1
Operation pattern". ("Continuous path control" cannot be set in fixed-
feed control.)
(2) If the movement amount of each axis exceeds "1073741824 (=2
30
)" when "0:
Composite speed" is set in "
Pr.20 Interpolation speed designation method",
the error "Outside linear movement amount range" (error code: 504) occurs at
a positioning start and positioning cannot be started. (The maximum
movement amount that can be set in "
Da.6
Positioning address/movement
amount" is "1073741824 (= 2
30
)".
(3) "Fixed-feed" cannot be set in "
Da.2
Control system" in the positioning data
when "continuous path control" has been set in "
Da.1
Operation pattern" of
the immediately prior positioning data. (For example, if the operation pattern of
positioning data No. 1 is "continuous path control", fixed-feed control cannot
be set in positioning data No. 2.) An axis error "Continuous path control not
possible" (error code: 516) will occur and the machine will carry out a
deceleration stop if this type of setting is carried out.
Summary of Contents for Melsec-Q QD75D1
Page 1: ......
Page 2: ......
Page 22: ...A 20 MEMO ...
Page 24: ...MEMO ...
Page 41: ...1 17 MELSEC Q 1 PRODUCT OUTLINE MEMO ...
Page 48: ...1 24 MELSEC Q 1 PRODUCT OUTLINE MEMO ...
Page 60: ...2 12 MELSEC Q 2 SYSTEM CONFIGURATION MEMO ...
Page 137: ...5 33 MELSEC Q 5 DATA USED FOR POSITIONING CONTROL MEMO ...
Page 232: ...5 128 MELSEC Q 5 DATA USED FOR POSITIONING CONTROL MEMO ...
Page 252: ...6 20 MELSEC Q 6 SEQUENCE PROGRAM USED FOR POSITIONING CONTROL ...
Page 253: ...6 21 MELSEC Q 6 SEQUENCE PROGRAM USED FOR POSITIONING CONTROL ...
Page 278: ...6 46 MELSEC Q 6 SEQUENCE PROGRAM USED FOR POSITIONING CONTROL MEMO ...
Page 292: ...MEMO ...
Page 436: ...9 120 MELSEC Q 9 MAJOR POSITIONING CONTROL MEMO ...
Page 464: ...10 28 MELSEC Q 10 HIGH LEVEL POSITIONING CONTROL MEMO ...
Page 638: ...14 24 MELSEC Q 14 DEDICATED INSTRUCTIONS MEMO ...
Page 647: ...15 9 MELSEC Q 15 TROUBLESHOOTING MEMO ...
Page 686: ...15 48 MELSEC Q 15 TROUBLESHOOTING MEMO ...
Page 839: ...Appendix 153 MELSEC Q APPENDICES 6 QD75D4N 90 23 27 4 12 98 4 46 Unit mm ...
Page 840: ...Appendix 154 MELSEC Q APPENDICES 7 QD75P1 QD75P2 QD75P4 27 4 23 98 90 4 46 unit mm ...
Page 841: ...Appendix 155 MELSEC Q APPENDICES 8 QD75D1 QD75D2 QD75D4 27 4 23 90 12 98 4 46 unit mm ...
Page 842: ...Appendix 156 MELSEC Q APPENDICES MEMO ...
Page 857: ......
Page 858: ......