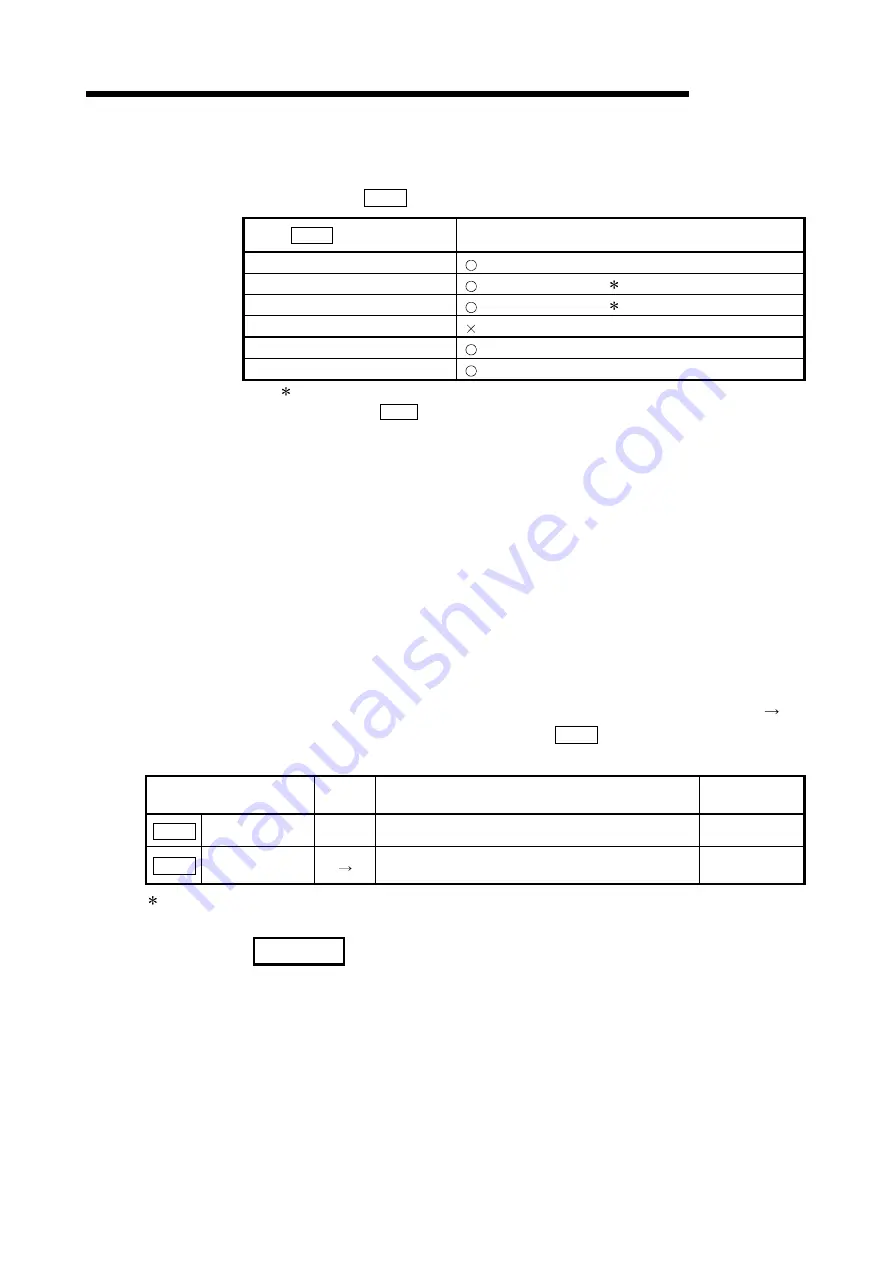
12 - 7
MELSEC-Q
12 CONTROL SUB FUNCTIONS
[2] Control Precautions
(1) The following table shows whether the OPR retry function may be executed
by the "
Pr.43
OPR method".
Pr.43 OPR method
Execution status of OPR retry function
Near-point dog method
: Execution possible
Stopper method 1)
: Execution possible 1
Stopper method 2)
: Execution possible 1
Stopper method 3)
: Execution not possible
Count method 1)
: Execution possible
Count method 2)
: Execution possible
1 Starting can be executed from the position of the limit switch installed in the opposition
direction of "
Pr.44
OPR direction". (The limit signal is OFF.) However, the retry
operation by the limit switch in the OPR direction cannot be executed since a stopper
is installed in the OPR direction.
(2) Always establish upper/lower limit switches at the upper/lower limit positions
of the machine, and connect them to the QD75. If the OPR retry function is
used without hardware stroke limit switches, the motor will continue rotation
until a hardware stroke limit signal is detected.
(3) Do not configure a system so that the drive unit power turns OFF by the
upper/lower limit switches connected to the QD75. If the drive unit power is
turned OFF, the OPR retry cannot be carried out.
[3] Setting method
To use the "OPR retry function", set the required details in the parameters shown
in the following table, and write them to the QD75.
When the parameters are set, the OPR retry function will be added to the
machine OPR control. The set details are validated at the rising edge (OFF
ON) of the PLC READY signal (Y0). (Set "
Pr.57
Dwell time during OPR retry"
according to the user's requirements.)
Setting item
Setting
value
Setting details
Factory-set
initial value
Pr.48 OPR retry
1
Set "1: Carry out OPR retry by limit switch".
0
Pr.57 Dwell time during
OPR retry
Set the deceleration stop time during OPR retry.
(Random value between 0 and 65535 (ms))
0
Refer to Section 5.2 "List of parameters" for setting details.
REMARK
•
Parameters are set for each axis.
•
It is recommended that the parameters be set whenever possible with GX
Configurator-QP. Execution by sequence program uses many sequence programs
and devices. The execution becomes complicated, and the scan times will
increase.
Summary of Contents for Melsec-Q QD75D1
Page 1: ......
Page 2: ......
Page 22: ...A 20 MEMO ...
Page 24: ...MEMO ...
Page 41: ...1 17 MELSEC Q 1 PRODUCT OUTLINE MEMO ...
Page 48: ...1 24 MELSEC Q 1 PRODUCT OUTLINE MEMO ...
Page 60: ...2 12 MELSEC Q 2 SYSTEM CONFIGURATION MEMO ...
Page 137: ...5 33 MELSEC Q 5 DATA USED FOR POSITIONING CONTROL MEMO ...
Page 232: ...5 128 MELSEC Q 5 DATA USED FOR POSITIONING CONTROL MEMO ...
Page 252: ...6 20 MELSEC Q 6 SEQUENCE PROGRAM USED FOR POSITIONING CONTROL ...
Page 253: ...6 21 MELSEC Q 6 SEQUENCE PROGRAM USED FOR POSITIONING CONTROL ...
Page 278: ...6 46 MELSEC Q 6 SEQUENCE PROGRAM USED FOR POSITIONING CONTROL MEMO ...
Page 292: ...MEMO ...
Page 436: ...9 120 MELSEC Q 9 MAJOR POSITIONING CONTROL MEMO ...
Page 464: ...10 28 MELSEC Q 10 HIGH LEVEL POSITIONING CONTROL MEMO ...
Page 638: ...14 24 MELSEC Q 14 DEDICATED INSTRUCTIONS MEMO ...
Page 647: ...15 9 MELSEC Q 15 TROUBLESHOOTING MEMO ...
Page 686: ...15 48 MELSEC Q 15 TROUBLESHOOTING MEMO ...
Page 839: ...Appendix 153 MELSEC Q APPENDICES 6 QD75D4N 90 23 27 4 12 98 4 46 Unit mm ...
Page 840: ...Appendix 154 MELSEC Q APPENDICES 7 QD75P1 QD75P2 QD75P4 27 4 23 98 90 4 46 unit mm ...
Page 841: ...Appendix 155 MELSEC Q APPENDICES 8 QD75D1 QD75D2 QD75D4 27 4 23 90 12 98 4 46 unit mm ...
Page 842: ...Appendix 156 MELSEC Q APPENDICES MEMO ...
Page 857: ......
Page 858: ......