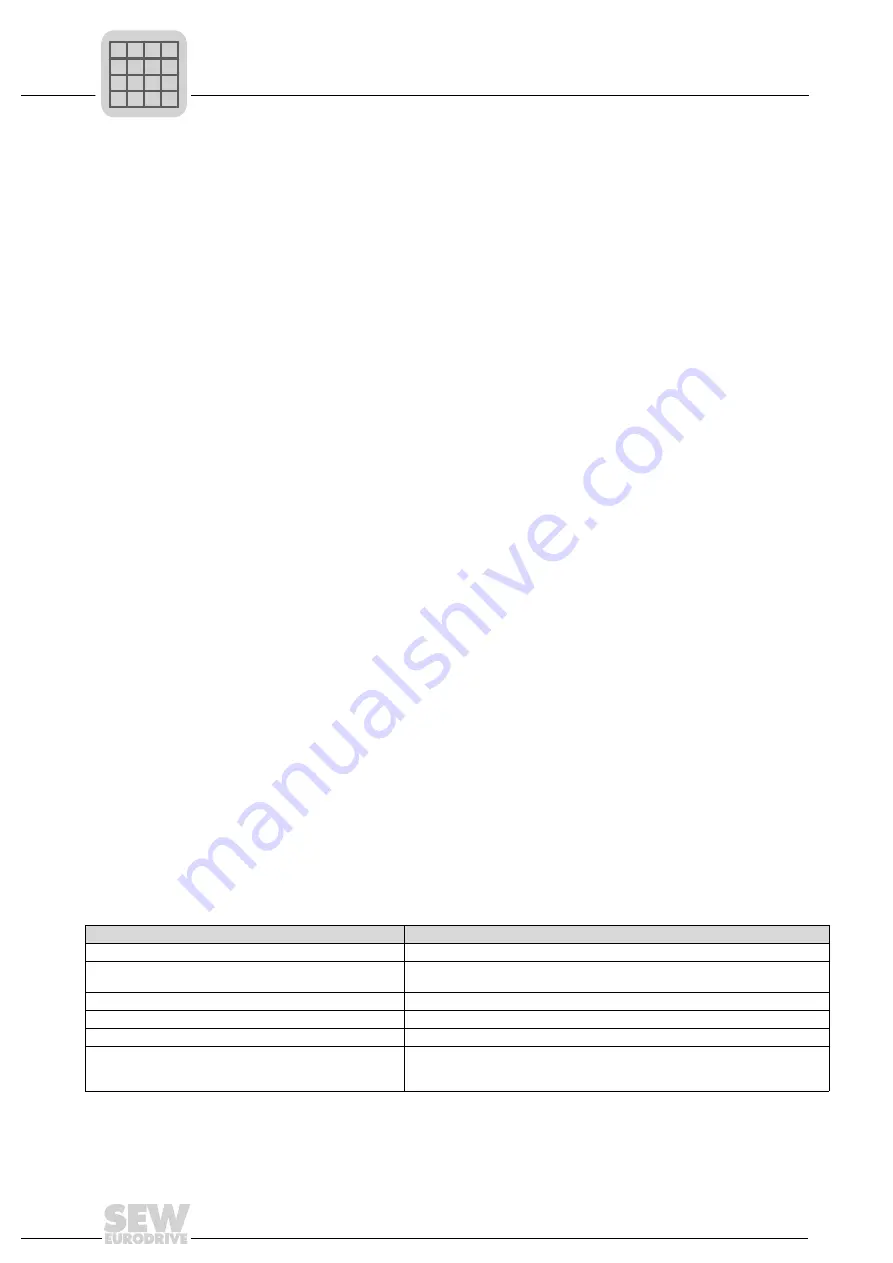
66
System Manual – MOVIDRIVE® compact Drive Inverters
2
IPOSplus®
Technical Data and Dimension Drawings
2.9
IPOS
plus®
Description
IPOS
plus®
positioning and sequence control is integrated into every MOVIDRIVE
®
in-
verter as standard. IPOS
plus®
can be used to execute control functions and positioning
tasks either simultaneously or independently of one another.
IPOS
plus®
sequence control makes it possible to run a user program, regardless of the
encoder feedback or the selected control mode (VFC, CFC, SERVO). In conjunction
with encoder feedback (MCV, MCS, MCH), IPOS
plus®
positioning provides high-perfor-
mance point-to-point positioning. The IPOS
plus®
program is written using the MOVI-
TOOLS
®
software. The operating software or DBG11B keypad (startup in VFC mode
only) can be used to start up the inverter, access parameters and change variables.
Features
•
Program execution independent of encoder feedback and operating mode.
•
The user program is continued even if a unit malfunction occurs (troubleshooting is
possible in the user program).
•
Two user programs can be run in parallel and independently of one another (task 1,
interrupt-capable, and task 2).
•
The user programs programmed in the assembler can contain up to 800 program
lines.
•
User-friendly and comprehensive control options for the inverter.
•
Extensive options for communication via system bus (SBus), RS-485, RS-232 and
fieldbus (direct communication with MOVIMOT
®
is possible).
•
Processing of digital and analog input/output signals.
Only with
MCV/MCS/MCH
•
Positioning with adjustable travel speed and positioning ramps.
•
Feedforward for position, speed and torque control loops with minimized lag error.
•
Two touch probe inputs.
•
Ramp types LINEAR, SINE and SQUARE.
•
Status and monitoring functions: Lag error monitoring, position signal, software and
hardware limit switches.
•
Eight reference travel types.
•
Possibility of changing the target position, travel speed, positioning ramp and torque
when movement is in progress.
•
Possibility of "endless positioning."
•
Override function.
Technical data
Max. program length of tasks 1 and 2
In total about 800 program lines (programmed in assembler)
Command processing time per program line
Task 1: 1.0 ms; Task 2: 0.5 ms
Variables
512, of which 128 (0 ... 127) can be stored to non-volatile memory; range of val-
ues: -2
31
...+(2
31
-1)
Touch probe inputs
2 inputs, processing time < 100
µ
s
Sampling interval of digital and analog inputs
1...5 ms
Digital inputs/outputs
6 inputs / 3 outputs
Analog inputs/outputs
1 input (0...10 V,
±
10 V, 0...20 mA, 4...20 mA)
1)
1 input (0...10 V)
1 output (0...20 mA, 4...20 mA)
1) Not for MCF41A
P
i
f
kVA
Hz
n
Summary of Contents for MOVIDRIVE compact MCH41A
Page 2: ...SEW EURODRIVE Driving the world...
Page 432: ......