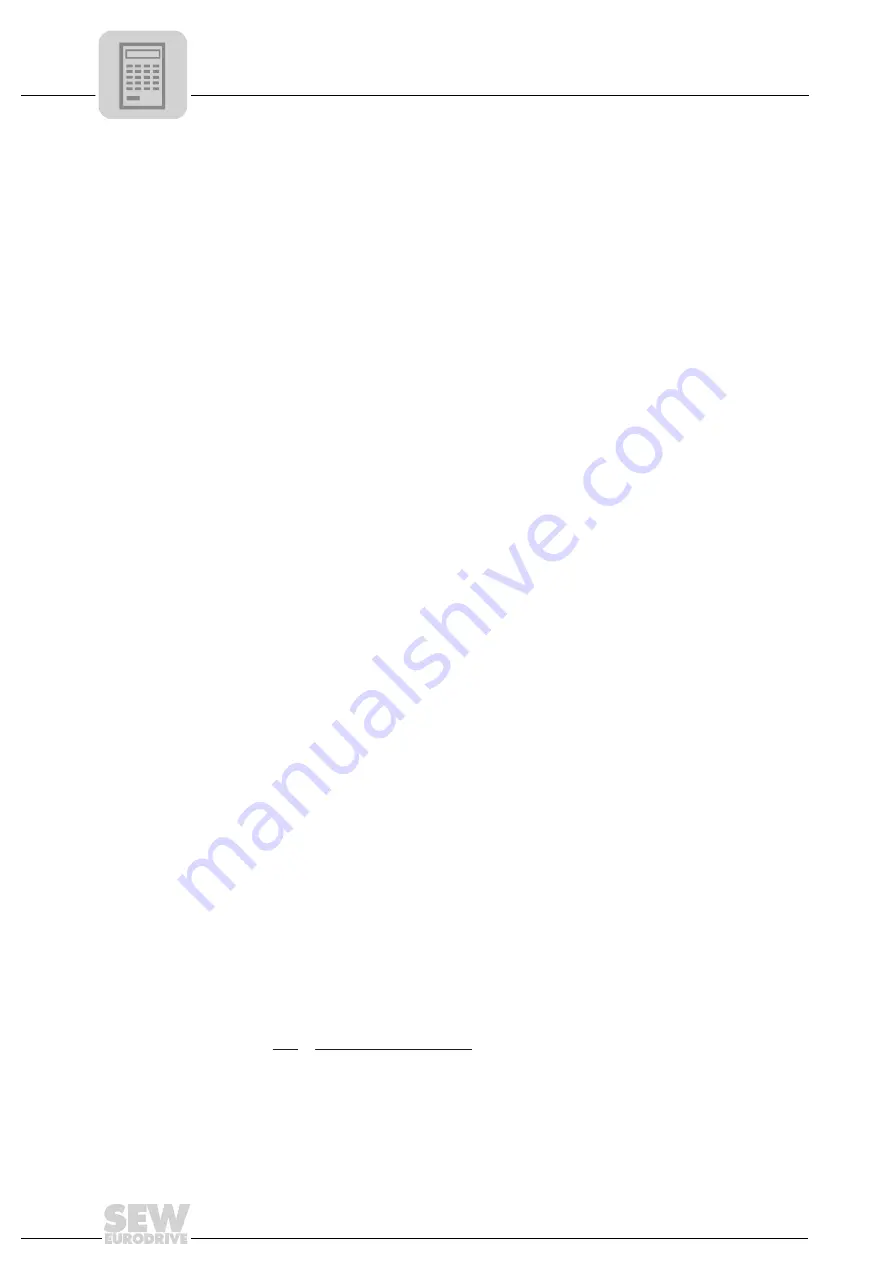
212
System Manual – MOVIDRIVE® compact Drive Inverters
4
Motor Selection for Synchronous Servomotors (SERVO)
Project Planning
Basic recommen-
dations
For the SEW motors, the motor data required for the SERVO operating modes is stored
in MOVIDRIVE
®
.
Speed is the correcting variable in the SERVO operating modes with speed control.
Torque is the correcting variable in the SERVO operating modes with torque control
(SERVO & M-CONTROL).
SERVO mode with
speed control
There is no need to differentiate between the load types quadratic, dynamic and static
when performing project planning for the SERVO operating mode. Project planning for
a synchronous motor is carried out in accordance with the following requirements:
1. Effective torque requirement at average application speed.
M
eff
< M
0
The operating point must lie below the characteristic curve for the continuous torque
(Figure 61, curve 1). If this operating point lies above the characteristic curve for self-
cooling, the continuous torque of the DFY series can be increased by 60% by forced
cooling.
2. Maximum torque needed across the speed curve.
M
max
< M
dyn_Mot
This operating point must lie below the characteristic curve for the maximum torque
of the motor/MOVIDRIVE
®
combination (Figure 61, curve 2).
3. Maximum speed
The maximum speed must not be configured higher than the rated speed of the mo-
tor. Planetary gear units should be used for speeds greater than 3000 1/min due to
the high input speed.
n
max
≤
n
N
SERVO operation
with torque control
(SERVO & M-
CTRL)
This operating mode allows the servomotor to be controlled directly with torque control.
The setpoint sources of the speed-controlled SERVO mode can also be used for torque
control. All speed setpoint sources (except for bus setpoints) are interpreted as current
setpoint sources. The settings for evaluating the analog input (
→
P11_, parameter de-
scription) also remain in effect. The fixed setpoints (P16_, P17_) can be entered in the
units [1/min] or [%I
N_inverter
] as required (
→
MOVITOOLS
®
).
The following relationship exists between the units:
3000 1/min = 150 % rated inverter current
The torque at the output shaft of the servomotor can be calculated using the following
formula:
04976AEN
M
0
Continuous static torque according to the motor table DS/CM
I
0
Continuous static current according to motor table DS/CM
M
M
I
=
x
0
0
150 % x
I
n_inverter
x n
setp
3000 1/min
Summary of Contents for MOVIDRIVE compact MCH41A
Page 2: ...SEW EURODRIVE Driving the world...
Page 432: ......