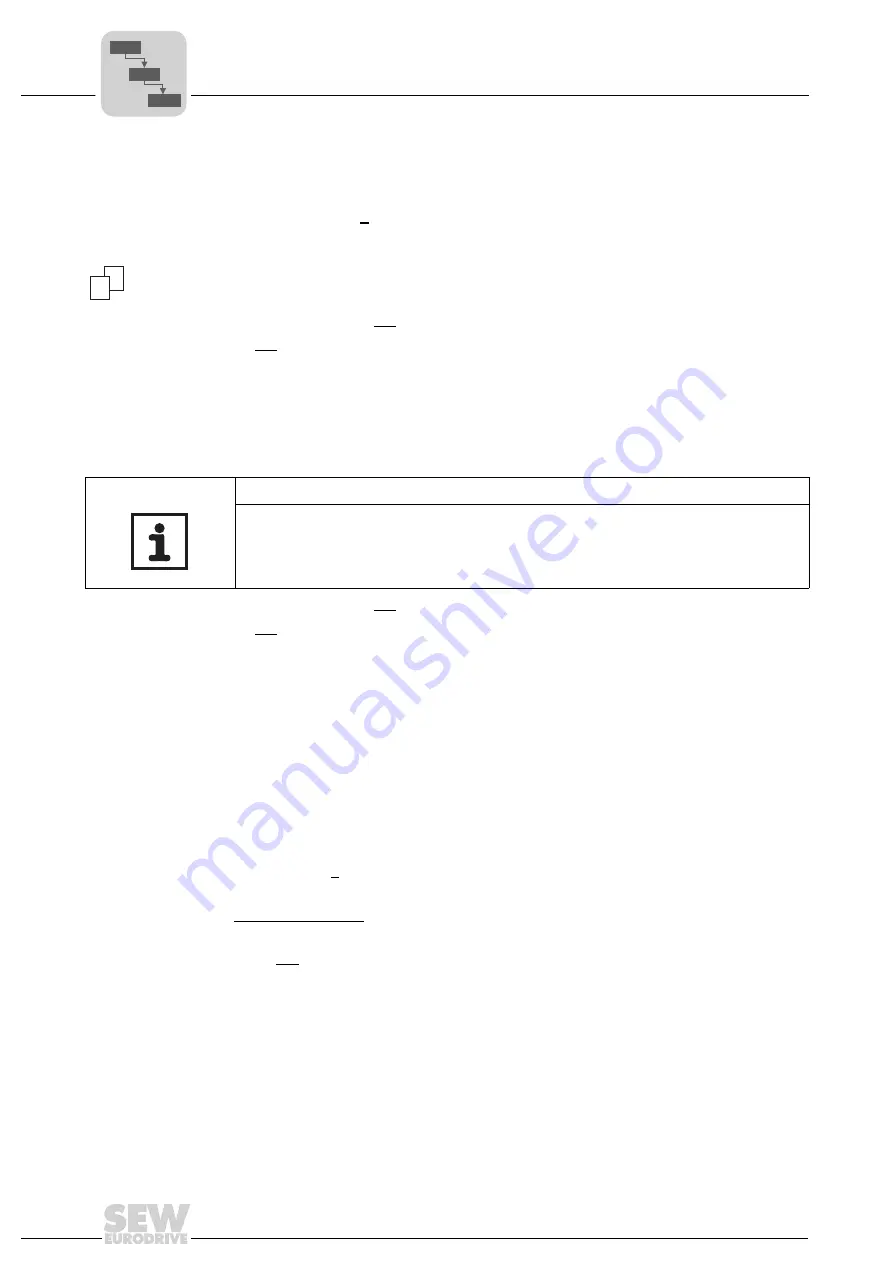
138
System Manual – MOVIDRIVE® compact Drive Inverters
3
Explanation of the parameters
Parameters
Activate the speed monitoring for hoists and set the delay time to a rather small value.
Speed monitoring is not that important for safety since an incorrect movement of the
hoist does not necessarily mean operation in the current limitation.
P501 / P503
Deceleration time
1 / 2
Setting range: 0 ... 1 ... 10 s
The set current limit can be reached briefly during acceleration, deceleration, or load
peaks. You can prevent the speed monitoring from responding too sensitively by setting
the deceleration time accordingly. The current limit must be reached permanently for the
duration of the delay time before monitoring responds.
P504 Encoder
monitoring motor
Setting range: YES / NO
•
NO: An open circuit between frequency inverter and motor encoder is not directly de-
tected. In case of a defective connection, error F08 Speed monitoring will be issued
in enabled state unless it was deactivated.
•
YES: An open circuit between frequency inverter and motor encoder will be directly
detected when using sin/cos encoders and TTL encoders. The error message F14
Encoder error will be issued in case of an error. This error will also be generated in
inhibited state.
P505 Encoder
monitoring
distance
Setting range: YES / NO
•
NO: An open circuit between frequency inverter and synchronous encoder is not di-
rectly detected. In case of a defective connection, error F08 Speed monitoring will be
issued in enabled state unless it was deactivated.
•
YES: An open circuit between frequency inverter and synchronous encoder will be
directly detected when using sin/cos encoders and TTL encoders. The error mes-
sage F14 Encoder error will be issued in case of an error. This error will also be gen-
erated in inhibited state.
P52x Power OFF
monitoring
Setting the parameter P520 Power off response time / P521 Power off response The
setting of P520/P521 is significant when a binary input is programmed to “POWER ON”
and MOVIDRIVE
®
regenerative mode is used (see MOVIDRIVE
®
regenerative power
unit MDR60A system manual).
P520 Power OFF
response time
Setting range: 0 ... 5 s
P521 Power OFF
response
CONTROL.INHIBIT / EMERGENCY STOP
P522 Phase fail-
ure monitoring
OFF / ON
The power supply phases of the MOVIDRIVE
®
unit are monitored for phase failure. If a
phase failure is detected in two phases, then the DC link will be de-energized, which cor-
responds to a power supply (mains) disconnection. Since the power supply phases can-
not be monitored directly, monitoring has to be done indirectly via ripple of the DC link,
which increases drastically in case of a phase failure.
The DC link voltage is monitored at a time interval
∆
t = 1 ms for dropping below a mini-
mum voltage level that depends on the rated supply voltage of the unit.
1
2
NOTE
Encoder monitoring is not a safety function!
If you use a HIPERFACE
®
encoder, encoder monitoring is always active (for the track
too) regardless of the setting in P504.
P6..
P60.
P600
Summary of Contents for MOVIDRIVE compact MCH41A
Page 2: ...SEW EURODRIVE Driving the world...
Page 432: ......