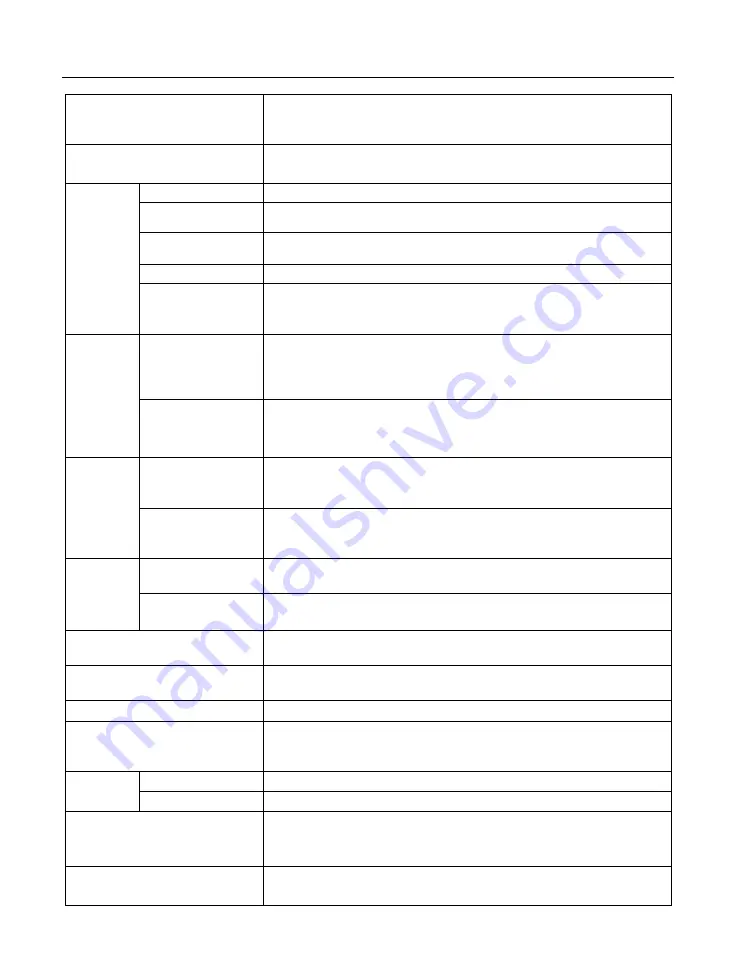
SD20-G Series
14
Control mode
Pt Position pulse mode Pr Internal register position mode _
Sz Analog speed mode Sr Internal register speed mode
Tz Analog torque mode Tr Internal register torque mode
Regenerative braking
Built-in or External (External braking should be selected and purchased)
Control
characteristic
Control mode
PMSM
Frequency response
1.2KHz
Speed fluctuation
±0.01
%
(VC, load fluctuation 0 to 100%)
Speed control range 1
:
10000
Input pulse frequency
1.
500KHz (differential drive); 200KHz (Open collector)
2.
At high-speed pulse circuit, receiving frequency is
4MHZ.(Differential)
Input signal
Control input
Servo on, Alarm reset, Pulse clear, Pulse prohibited, Forward run prohibited,
Reverse run prohibited, Forward torque limit, Reverse torque limit, Internal
speed selection, Internal position triggered, “Home” searching triggered, Zero
speed CLAMP
Speed Feedback
1.
Absolute encoder.
2.
Incremental encoder.
3.
Resolver
Output
signal
Control output
Servo ready, Servo alarm activated, At positioning completed, At speed
reached, Electromagnetic brake control, Rotation Detection, At speed limit,
Homing completed, At torque limit, and so on.
Encoder signal
frequency-division
output
1.
Encoder Z phase open-collector output.
2.
Encoder signal output (A, B Z Line Driver) frequency-division output
3.
Z pulse time extend function.
Position
control
Input mode
1. A phase+B phase 2. Forward pulse+Reverse pulse
3. Pulse+Direction 4. Internal register
Electronic gear
1.
0.01≤ B / A ≤100
2.
Two groups electronic gear can be selected by users.
Analog speed control
-10V
~
+10V analog speed signal input, the voltage scope can be set by
function code.
Analog torque control
-10V
~
+10V analog torque signal input, the voltage scope can be set by
function code.
Acceleration/Deceleration
Accele/decele time is set to 1
~
30000ms(related to 0←→rated speed)
Communication
1.
RS485 communication port is connected with PC, to set control
parameters and to monitor servo.
2.
CANopen or EtherCAT can be selected as option.
Parameters
setting
Keypad
The parameters are set by keypad, which is displayed by 5LEDs.
PC/PLC
RS485 communication can set parameters by some PC/PLC software.
Monitor function
Output current, PN voltage, motor speed, motor feedback pulse, motor
feedback rotation, given pulse, given pulse error, given speed, given torque,
analog speed given and analog torque given.
Protection function
Overvoltage, Undervoltage, Overload, Overcurrent, Encoder error,
Overspeed, Abnormal pulse control command, Emergency stop, Servo
Summary of Contents for SD20-G Series
Page 35: ...SD20 G Series 35 M3 structure Fig 3 1 5 Servo drive structure 3...
Page 36: ...SD20 G Series 36 ML3 structure 118 5 5 7 5 93 297 8 223 118 93 0 5 12 5 7 5 4 M4...
Page 38: ...SD20 G Series 38 M4 structure Approx mass 10 365 kg Fig 3 1 7 Servo drive structure 5...
Page 39: ...SD20 G Series 39 M5 structure Approx msaa 11 1Kg Fig 3 1 8 Servo drive structure 6...
Page 40: ...SD20 G Series 40 M6 structure Approx mass 17 4Kg Fig 3 1 9 Servo drive structure 7...
Page 182: ...SD20 G Series 182 Fig 6 4 44SD20E Cam internal frameworkdiagram...