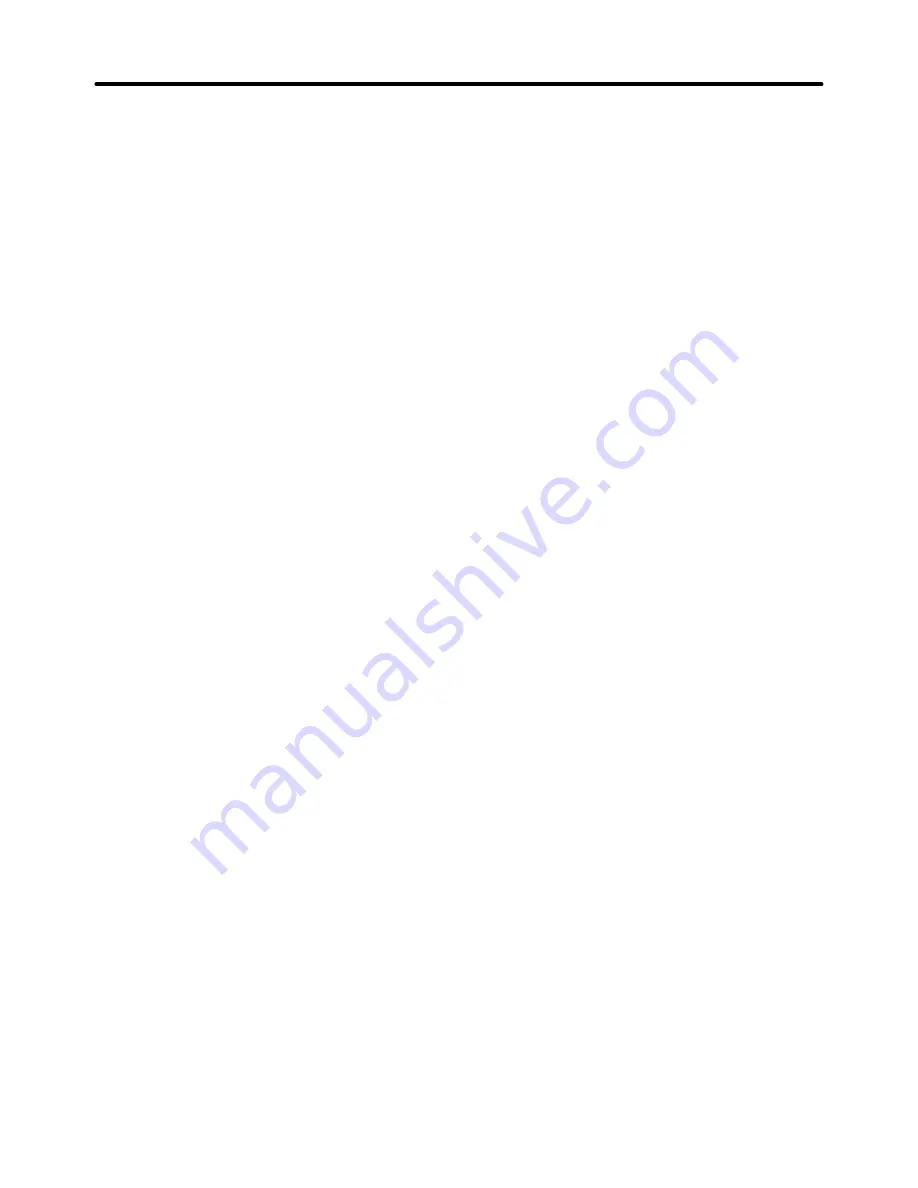
8-20
H
If the Motor Rotates Even When Inverter Output is Stopped
The DC braking is not operating properly. If the motor continues operating at low speed, without com-
pletely stopping, and after a deceleration stop has been executed, it means that the DC braking is not
decelerating enough. Adjust the DC braking as follows:
S
Increase the parameter b2-02 (DC injection braking current) setting.
S
Increase the parameter b2-04 (DC injection braking time at stop) setting.
H
If 0 V is Detected When the Fan is Started, or Fan Stalls
DC braking is insufficient at startup. Generation of 0 V and stalling can occur if the fan is turning when it
is started. This can be prevented by slowing fan rotation by DC braking before starting the fan. In-
crease the parameter b2-03 (DC injection braking time at start) setting.
H
If Output Frequency Does Not Rise to Frequency Reference
•
The frequency reference is within the jump frequency range.
When the jump frequency function is used, the output frequency does not change within the jump fre-
quency range. Check to be sure that the jump frequency (parameters d3-01 to d3-03) and jump fre-
quency width (parameter d3-04) settings are suitable.
•
The frequency reference upper limit has been reached.
The output frequency upper limit is determined by the following formula:
Maximum output frequency (E1-04) x Frequency reference upper limit (d2-01) / 100
Check to be sure that the parameter E1-04 and d2-01 settings are suitable.
H
Inverter Overload “OL2” is Detected
For a 400-V Inverter, if the carrier frequency “C6-01” is set to a value higher than the default setting, the
Inverter overload “OL2” detection value will decrease in consideration of an increase in the heat that will
be generated by the change in the carrier frequency. Since the detection value is set to decrease by
approximately 15% for every increase of 2 kHz from the default setting , the Inverter overload “OL2” may
be detected prior to the motor overload “OL1” depending on the set value. Set the carrier frequency to a
lower level.
H
If Inverter Does Not Operate Due to an EF Error (Forward and Reverse
Commands Input)
D
The sequence is faulty.
The EF error will be detected if the forward command and reverse command are input at the same time
for over 0.5 seconds. Check and correct the sequence.
D
Stray current causes malfunction.
The Inverter input may always remain ON due to stray current from the control section. As shown in the
following illustration, a current may flow in the direction shown by an arrow to turn ON the Inverter input
Maintenance Operations
Chapter 8
Summary of Contents for SYSDRIVE 3G3FV
Page 1: ...USER S MANUAL High function General purpose Inverter SYSDRIVE 3G3FV Cat No I516 E1 4 ...
Page 16: ...Chapter 1 Introduction 1 1 Function 1 2 Nomenclature 1 3 New Functions 1 ...
Page 33: ...Chapter 2 Installation 2 1 Mounting 2 2 Wiring 2 ...
Page 112: ...Chapter 4 Trial Operation 4 1 Procedure 4 2 Operation Example 4 ...
Page 289: ...Chapter 7 Parameter Lists 7 1 Initialize Mode Parameters 7 2 Program Mode Parameter List 7 ...
Page 366: ...Chapter 9 Specifications 9 1 Inverter Specifications 9 2 Option Specifications 9 ...
Page 395: ...Chapter 10 Appendix 10 1 Notes on Using the Inverter for a Motor 10 ...