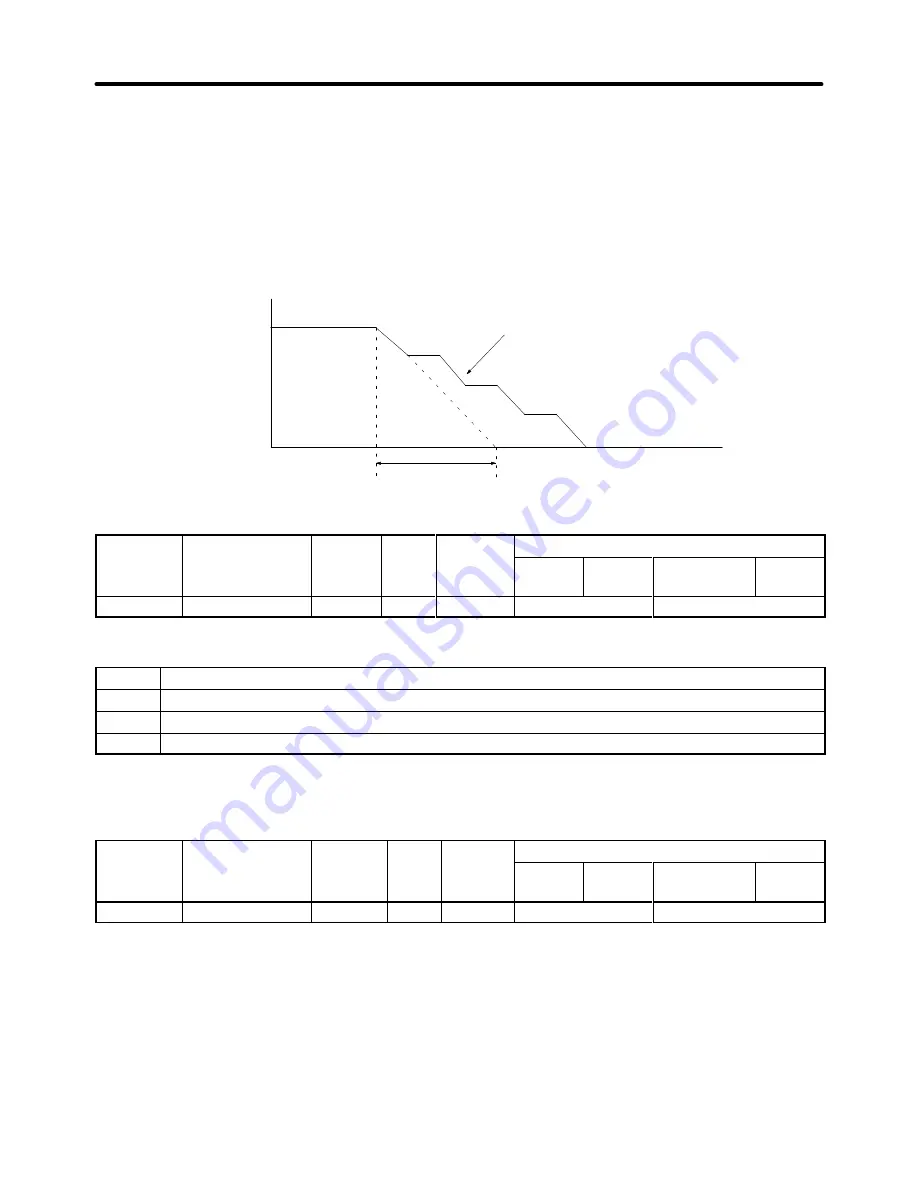
6-103
•
When this parameter is set to 3, in contrast to a setting of 0, the deceleration time is automatically
prolonged with main axis overvoltage (OV) easily detected. Therefore the actual deceleration time
becomes longer than the deceleration time that has been set. This can be adjusted, however, by set-
ting a shorter deceleration time than for the 0 setting, so that the actual deceleration time will also be
shorter.
Note The parameter cannot be set to 3 in flux vector control.
Deceleration Stall Prevention Example: L3-04 = 1
Output frequency
The deceleration time is controlled
to prevent overvoltage.
Time
Deceleration time
(set value)
Parameter
Display name
Setting
Units
Default
Valid access levels
number
p y
g
range
setting
V/f
Control
V/f with
PG
Open Loop
Vector
Flux
Vector
L3-05
StallP Run Sel
0 to 2
---
1
Basic or Advanced Not applicable.
Note This parameter cannot be changed during operation.
Setting
Function
0
Disabled. (Run according to the settings. Stalls may occur with large loads.)
1
Enabled – deceleration time 1. (Use deceleration time in C1-02 for stall prevention function.)
2
Enabled – deceleration time 2. (Use deceleration time in C1-04 for stall prevention function.)
•
When setting 1 or 2 (enabled) is selected, deceleration is started if the run stall prevention level’s cur-
rent continues for more than 100 ms. The motor is accelerated back to the reference frequency again
when the current falls below this level.
Parameter
Display name
Setting
Units
Default
Valid access levels
number
p y
g
range
setting
V/f
Control
V/f with
PG
Open Loop
Vector
Flux
Vector
L3-06
StallP Run Level
30 to 200 %
160
Basic or Advanced Not applicable.
Note This parameter cannot be changed during operation.
•
This setting is valid when L3-05 is set to 1 or 2.
•
Normally it isn’t necessary to change this setting.
•
Decrease this setting when the motor’s capacity is small compared to the Inverter’s capacity or stalling
occurs when the motor is operated with the default setting. The standard target setting is 2 to 3 times
the motor’s rated current. (Set this current value as a percentage of the Inverter’s rated current, i.e.,
100% corresponds to the Inverter’s rated current.)
Advanced Operation
Chapter 6
Summary of Contents for SYSDRIVE 3G3FV
Page 1: ...USER S MANUAL High function General purpose Inverter SYSDRIVE 3G3FV Cat No I516 E1 4 ...
Page 16: ...Chapter 1 Introduction 1 1 Function 1 2 Nomenclature 1 3 New Functions 1 ...
Page 33: ...Chapter 2 Installation 2 1 Mounting 2 2 Wiring 2 ...
Page 112: ...Chapter 4 Trial Operation 4 1 Procedure 4 2 Operation Example 4 ...
Page 289: ...Chapter 7 Parameter Lists 7 1 Initialize Mode Parameters 7 2 Program Mode Parameter List 7 ...
Page 366: ...Chapter 9 Specifications 9 1 Inverter Specifications 9 2 Option Specifications 9 ...
Page 395: ...Chapter 10 Appendix 10 1 Notes on Using the Inverter for a Motor 10 ...