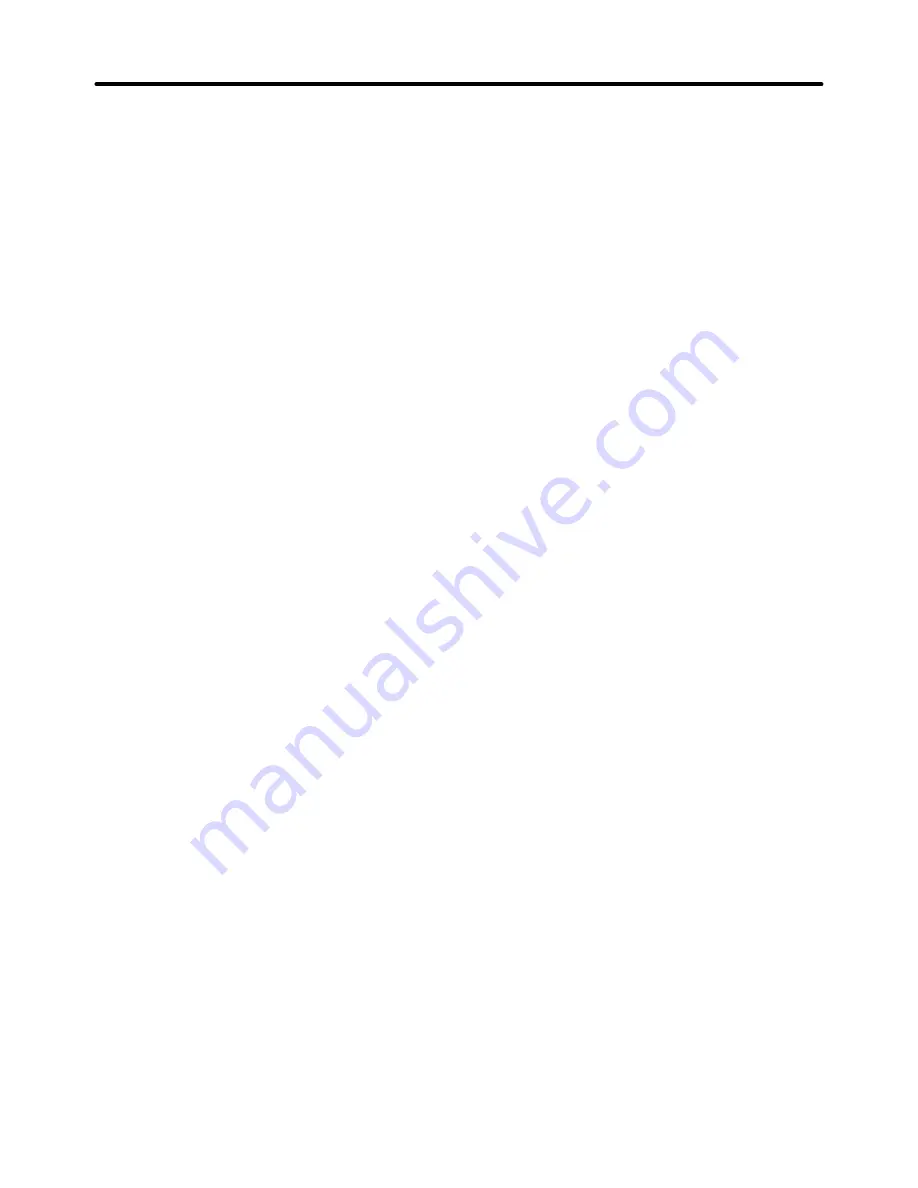
8-19
high leakage detection level (i.e., a sensitivity current of 200 mA or greater per Unit, with an operating
time of 0.1 s or more), or one that incorporates high frequency measures (i.e., one designed for use
with Inverters).
It will also help to some extent to lower the Inverter’s carrier frequency (parameter C6-01). In addition,
remember that the leakage current increases as the cable is lengthened. (In general, approximately
5 mA of leakage current occurs for each meter of cable.)
H
If There is Mechanical Vibration
D
The machinery is making unusual sounds.
•
There may be resonance between the mechanical system’s characteristic frequency and the carrier
frequency. If the motor is running with no problems and the machinery is vibrating with a high-pitched
whine, it may indicate that this is occurring. To prevent this type of resonance, adjust the carrier fre-
quency with parameters C6-01 to C6-03.
•
There may be resonance between a machine’s characteristic frequency and the output frequency of
the Inverter. To prevent this from occurring, either use the jump frequency functions in parameters
d3-01 to d3-04 or install rubber padding on the motor base to reduce vibration.
D
Vibration and hunting are occurring with open-loop vector control.
The gain adjustment may be insufficient. Reset the gain to a more effective level by adjusting parame-
ters C4-02 (torque compensation time constant), C8-08 (AFR gain), and C3-02 (slip compensation
primary delay time) in order. Lower the gain setting and raise the primary delay time setting.
D
Vibration and hunting are occurring with V/f control.
The gain adjustment may be insufficient. Reset the gain to a more effective level by adjusting parame-
ters C4-02 (torque compensation time constant), C7-02 (hunting prevention gain), and C3-02 (slip
compensation primary delay time) in order. Lower the gain setting and raise the primary delay time
setting.
D
Vibration and hunting are occurring with flux vector control.
The gain adjustment may be insufficient. Adjust the various types of speed control loop (ASR) gain.
(For details, refer to
Chapter 5 Basic Operation of this manual.) If the mechanical system’s resonance
point coincides with the Inverter’s operating frequency and the vibration cannot be eliminated in this
way, increase the ASR primary delay time (parameter C5-06) and then try adjusting the gain again.
D
Vibration and hunting are occurring with V/f w/PG control.
The gain adjustment may be insufficient. Adjust the various types of speed control loop (ASR) gain.
(For details, refer to
Chapter
5 Basic Operation of this manual.) If the vibration cannot be eliminated in
this way, set the hunting prevention selection (parameter C7-01) to “0” (disabled) and then try adjust-
ing the gain again.
D
Vibration and hunting are occurring with PID control.
Check the vibration cycle and individually adjust the P, I, and D. (Refer to page 6-55.)
Maintenance Operations
Chapter 8
Summary of Contents for SYSDRIVE 3G3FV
Page 1: ...USER S MANUAL High function General purpose Inverter SYSDRIVE 3G3FV Cat No I516 E1 4 ...
Page 16: ...Chapter 1 Introduction 1 1 Function 1 2 Nomenclature 1 3 New Functions 1 ...
Page 33: ...Chapter 2 Installation 2 1 Mounting 2 2 Wiring 2 ...
Page 112: ...Chapter 4 Trial Operation 4 1 Procedure 4 2 Operation Example 4 ...
Page 289: ...Chapter 7 Parameter Lists 7 1 Initialize Mode Parameters 7 2 Program Mode Parameter List 7 ...
Page 366: ...Chapter 9 Specifications 9 1 Inverter Specifications 9 2 Option Specifications 9 ...
Page 395: ...Chapter 10 Appendix 10 1 Notes on Using the Inverter for a Motor 10 ...