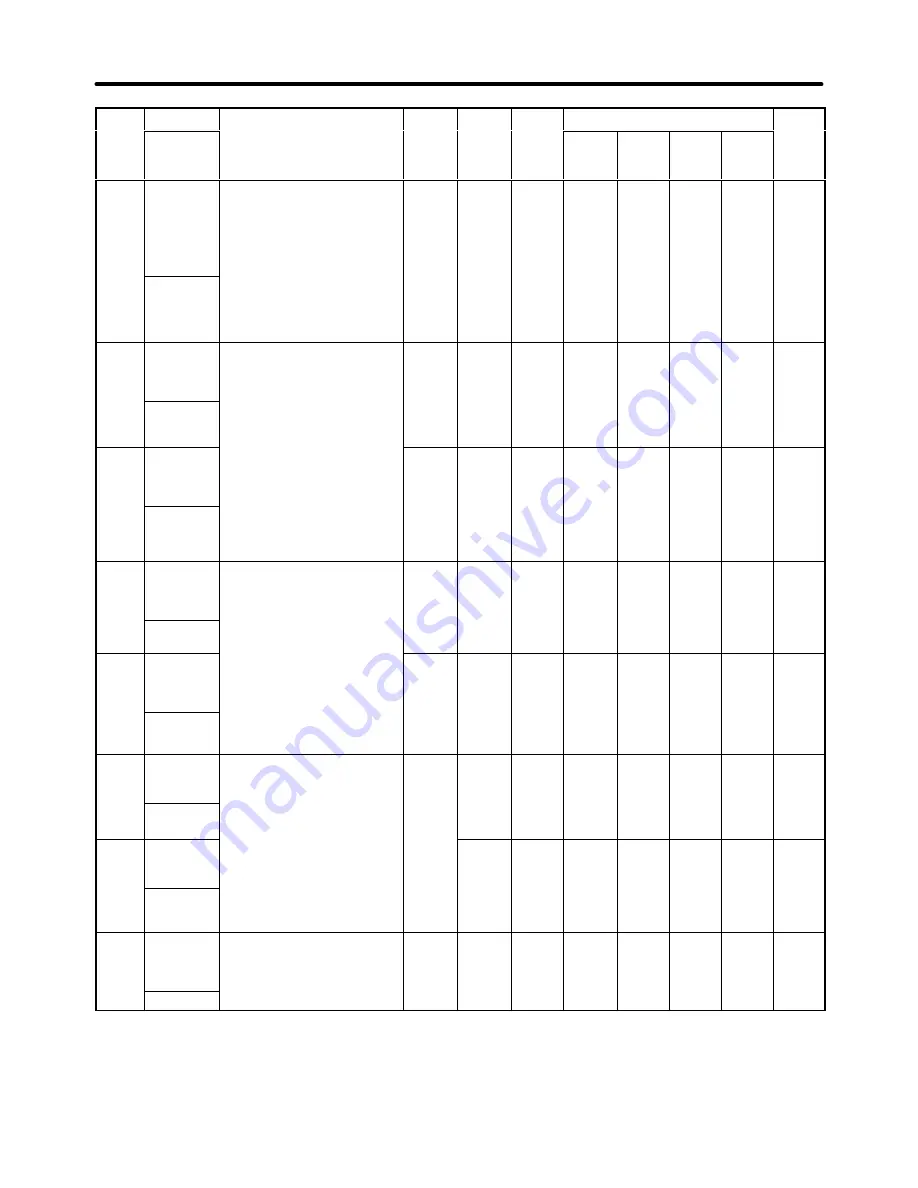
7-31
Para
meter
No.
Page
Control mode
Chan-
ges
during
opera-
tion
Default
setting
Setting
range
Description
Name
Para
meter
No.
Page
Flux
vector
Open
loop
vector
V/f
with
PG
V/f
control
Chan-
ges
during
opera-
tion
Default
setting
Setting
range
Description
Display
name
F1-07
Selecting
integral
control
during
accel/decel.
Sets integral control during
acceleration/deceleration to
either enabled or disabled.
0:
Disabled (The integral
function isn’t used while
accelerating or
decelerating; it is used at
0, 1
0
NO
X
B
X
X
5-47
PG Ramp
PI/I Sel
decelerating it is used at
constant speeds.)
1:
Enabled (The integral
function is used at all
times.)
F1-08
Overspeed
(OS)
detection
level.
Sets the overspeed detection
method. Frequencies above that
set for F1-08 (set as a
percentage of the maximum
f
)
hi h
ti
t
0 to
120
115
NO
X
A
X
A
5-32,
5-48
PG
Overspd
Level
g
frequency), which continue to
exceed this frequency for the
detection time (F1-09), are
detected as overspeed faults
F1-09
Overspeed
(OS)
detection
time
detected as overspeed faults.
0.0 to
2.0
0.0
(See
note.)
NO
X
A
X
A
5-32,
5-48
PG
Overspd
Time
F1-10
PG speed
deviation
detection
level (DEV)
Sets the speed deviation
detection method.
Any speed deviation above the
F1-10 set level (set as a
0 to 50
10
NO
X
A
X
A
5-33,
5-49
PG Deviate
Level
F1-10 set level (set as a
percentage of the maximum
frequency), which continues for
the deviation detection time
F1-11
PG speed
deviation
detection
time (DEV)
the deviation detection time
(F1-11) is detected as a speed
deviation.
Note: Speed deviation is the dif-
ference between actual
0.0 to
10.0
0.5
NO
X
A
X
A
5-33,
5-49
PG Deviate
Time
ference between actual
motor speed and the ref-
erence command speed.
F1-12
Number of
PG gear
teeth 1
Sets the number of teeth on the
gears if there are gears
between the PG and the motor.
0 to
1000
0
NO
X
A
X
X
5-46
PG # Gear
Teeth1
Motor speed (r/min) =
[No. of pulses input from PG x
/N
f PG
l
(F
)]
F1-13
Number of
PG gear
teeth 2
[No. of ulses in ut from PG x
60/No. of PG pulses (F1-01)] x
[(F1-13)/(F1-12)]
Note: A gear ratio of 1 will be
0
NO
X
A
X
X
5-46
PG # Gear
Teeth2
Note: A gear ratio of 1 will be
used if either of these pa-
rameters is set to 0.
F1-14
PG Discon-
nection
Detection
Time
Used to set the PG
disconnection detection time.
PGO will be detected if the
detection time continues beyond
th
t ti
0 to
10.0
2.0
NO
X
A
X
A
---
PG0 Time
y
the set time.
Note The setting range will change when the control mode is changed. (The setting range for Open
loop vector control is given above.)
Parameter Lists
Chapter 7
Summary of Contents for SYSDRIVE 3G3FV
Page 1: ...USER S MANUAL High function General purpose Inverter SYSDRIVE 3G3FV Cat No I516 E1 4 ...
Page 16: ...Chapter 1 Introduction 1 1 Function 1 2 Nomenclature 1 3 New Functions 1 ...
Page 33: ...Chapter 2 Installation 2 1 Mounting 2 2 Wiring 2 ...
Page 112: ...Chapter 4 Trial Operation 4 1 Procedure 4 2 Operation Example 4 ...
Page 289: ...Chapter 7 Parameter Lists 7 1 Initialize Mode Parameters 7 2 Program Mode Parameter List 7 ...
Page 366: ...Chapter 9 Specifications 9 1 Inverter Specifications 9 2 Option Specifications 9 ...
Page 395: ...Chapter 10 Appendix 10 1 Notes on Using the Inverter for a Motor 10 ...