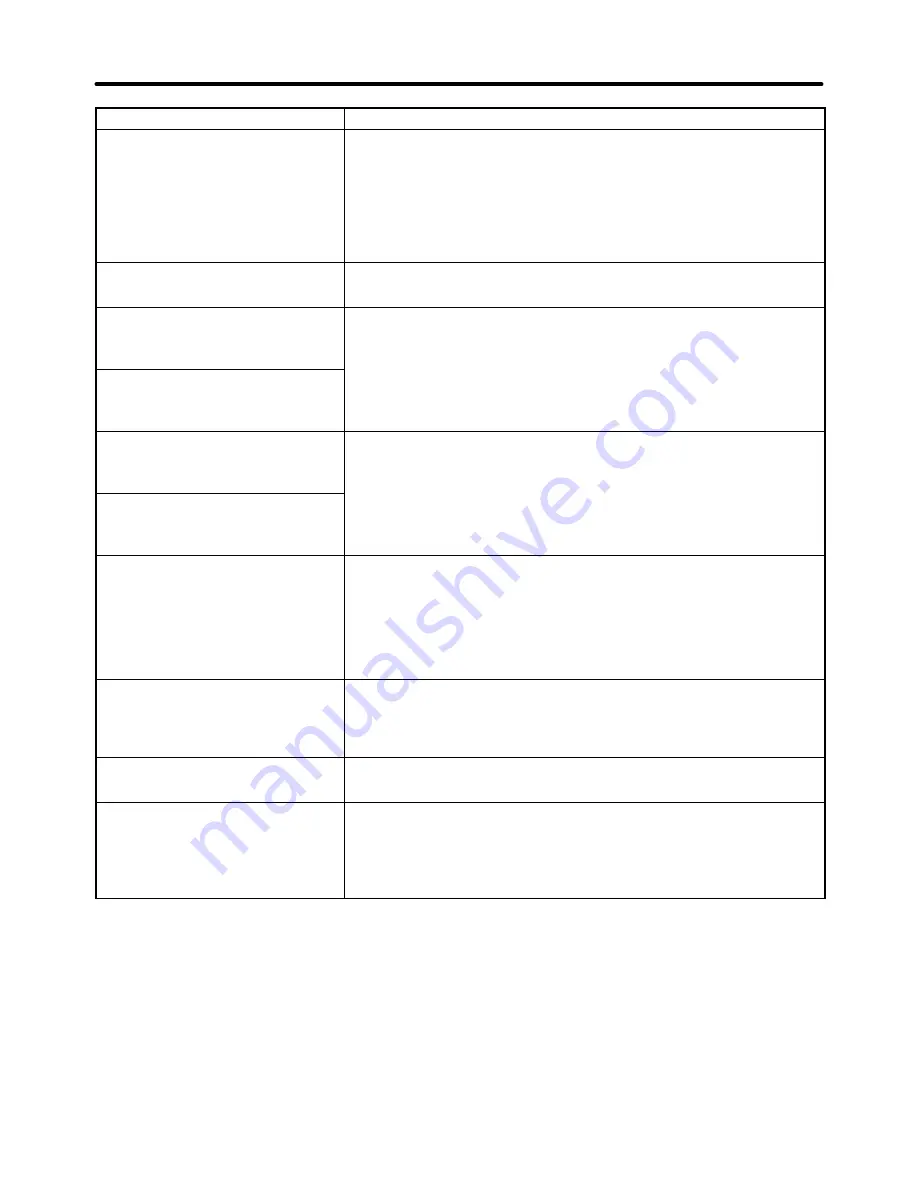
5-38
Fault display
Probable cause and remedy
Accelerate
(Motor acceleration fault)
The motor doesn’t accelerate within the prescribed time.
•
The torque limit function is operating.
→
Initialize the torque limit parameters (H7-01 to H7-04).
•
The acceleration time is too short.
→
Increase acceleration time 1 (C1-01).
•
A load is connected to the motor axis.
→
Remove the load.
Rated Slip
(Rated slip fault)
The rated slip setting can’t be tuned within the prescribed time.
•
A load is connected to the motor axis.
→
Remove the load.
Saturation-1
(Core-saturation coefficient 1 fault)
The core-saturation coefficients can’t be tuned within the prescribed
time.
•
The rated current setting isn’t correct.
Saturation-2
(Core-saturation coefficient 2 fault)
g
→
Check and change the setting if necessary.
•
There is a broken/disconnected motor power wire.
→
Check and replace wiring components if necessary.
Resistance
(Motor wire resistance fault)
The motor terminal resistance or no-load current setting can’t be tuned
within the prescribed time.
•
The rated current setting isn’t correct.
No-load Current
(Motor no-load current fault)
g
→
Check and change the setting if necessary.
•
There is a broken/disconnected motor power wire.
→
Check and replace wiring components if necessary.
PGO, PG Open
(Broken PG cable detection)
Pulses aren’t being input from the PG even though a rotation output is
being sent to the motor.
•
The cable to the PG is broken/disconnected.
→
Check the wiring and correct any problems.
•
The PG’s power supply is broken/disconnected.
→
Check the power supply voltage and correct if necessary.
PG Direction
(Motor direction error)
•
The motor direction and PG direction are different.
→
Motor power lines are wrong. Connect in following order: U, V, W.
→
Encoder wiring is wrong. Wire phase A, phase B, and + correctly.
→
F1-05 is set incorrectly. Set so that the directions agree.
Minor Fault
(Minor fault)
•
A minor fault has occurred in the Inverter (warning or alarm detected).
→
Refer to
Chapter
8 Maintenance Operations for appropriate actions.
V/f Over Setting
(V/f setting too high)
•
The torque reference exceeded 100% and the non-load current ex-
ceeded 70% of the rated motor current during auto-tuning.
→
The settings are incorrect for the rated voltage or rated frequency.
Correct the settings.
→
The motor is connected to a load. Disconnect the load.
Basic Operation
Chapter 5
Summary of Contents for SYSDRIVE 3G3FV
Page 1: ...USER S MANUAL High function General purpose Inverter SYSDRIVE 3G3FV Cat No I516 E1 4 ...
Page 16: ...Chapter 1 Introduction 1 1 Function 1 2 Nomenclature 1 3 New Functions 1 ...
Page 33: ...Chapter 2 Installation 2 1 Mounting 2 2 Wiring 2 ...
Page 112: ...Chapter 4 Trial Operation 4 1 Procedure 4 2 Operation Example 4 ...
Page 289: ...Chapter 7 Parameter Lists 7 1 Initialize Mode Parameters 7 2 Program Mode Parameter List 7 ...
Page 366: ...Chapter 9 Specifications 9 1 Inverter Specifications 9 2 Option Specifications 9 ...
Page 395: ...Chapter 10 Appendix 10 1 Notes on Using the Inverter for a Motor 10 ...