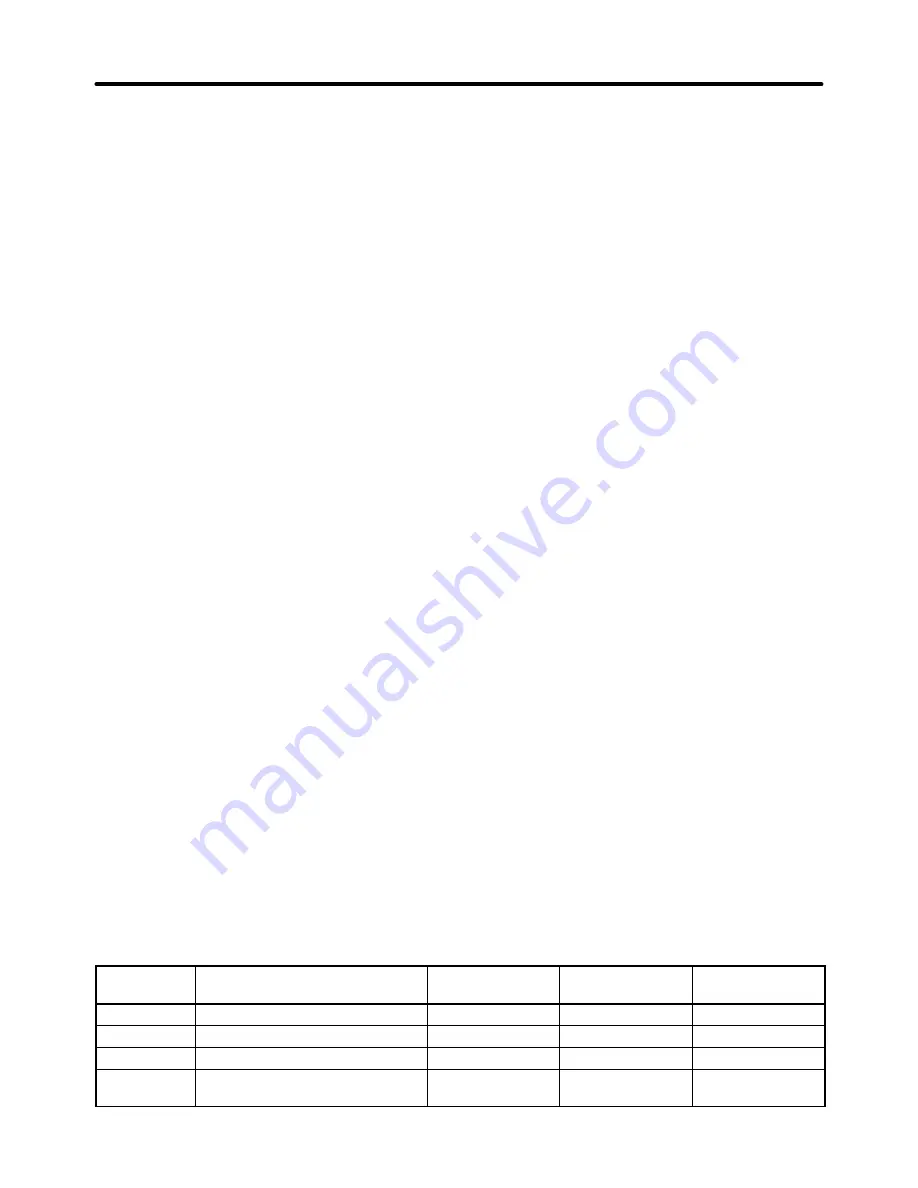
1-16
H
Protection Setting for Motors for Vector Control (Parameter E1-02)
A special protection setting has been provided for vector-control motors, which have high resistance to
overloads even at low speeds.
H
Bias Function for Analog Monitor Cards (Parameters F4-05 and F4-06)
A bias function has been added to the analog output from Analog Monitor Cards to enable adjusting the
offset voltage.
H
NC Contact Emergency Stop Function for Multi-function Inputs
(Parameters d3-01 to d3-04)
An NC contact emergency stop function has been added to the previous NO function.
H
Bias Function for Reverse Motor Control for Multi-function Inputs
(Parameters H3-05 and H3-09)
A function has been added for reverse motor operation by establishing a frequency bias 2 (setting: D)
for the multi-function inputs that causes reverse operation when the sum of the bias values is negative.
H
Run Command Selection Outside of Drive Mode (Parameter b1-08)
A function has been added to enable or disable run command inputs in mode other than Drive Mode,
e.g., Program Mode or Initialize Mode.
Note If this function is used, a run command can be input and Inverter operation stared even when
adjusting parameters in Program Mode. Proper safety measures must be taken to prevent dan-
gerous situations.
H
Motor Core Loss Adjustment for Torque Compensation (Parameter
E2-10)
A motor core loss setting has been added to enable fine adjustment of torque compensation (totally
automatic torque boast) in V/f control without PG and V/f control with PG control modes.
H
Changes in Default Settings and Setting Ranges
The defaults and setting ranges for the following parameters have been changed for applications.
D
Cumulative Operation Time Display Change (Parameter o2-07)
Previously 0 was display when the default value was set for the cumulative operation time, but this has
been changed to display the current cumulative operation time as the default.
D
New Parameter Setting Ranges
Parameter
number
Parameter name
Applicable
Inverters
Previous setting
range
New setting
range
E2-06
Motor leakage inductance
All Inverters
0% to 30%
0% to 40%
E5-06
Motor 2 leakage inductance
All Inverters
0% to 30%
0% to 40%
L2-03
Minimum baseblock time
All Inverters
0.0 to 5.0 s
0.1 to 5.0 s
L8-02
Inverter overheat detection pre-
alarm level
All Inverters
50 to 110
°
C
50 to 130
°
C
Introduction
Chapter 1
Summary of Contents for SYSDRIVE 3G3FV
Page 1: ...USER S MANUAL High function General purpose Inverter SYSDRIVE 3G3FV Cat No I516 E1 4 ...
Page 16: ...Chapter 1 Introduction 1 1 Function 1 2 Nomenclature 1 3 New Functions 1 ...
Page 33: ...Chapter 2 Installation 2 1 Mounting 2 2 Wiring 2 ...
Page 112: ...Chapter 4 Trial Operation 4 1 Procedure 4 2 Operation Example 4 ...
Page 289: ...Chapter 7 Parameter Lists 7 1 Initialize Mode Parameters 7 2 Program Mode Parameter List 7 ...
Page 366: ...Chapter 9 Specifications 9 1 Inverter Specifications 9 2 Option Specifications 9 ...
Page 395: ...Chapter 10 Appendix 10 1 Notes on Using the Inverter for a Motor 10 ...