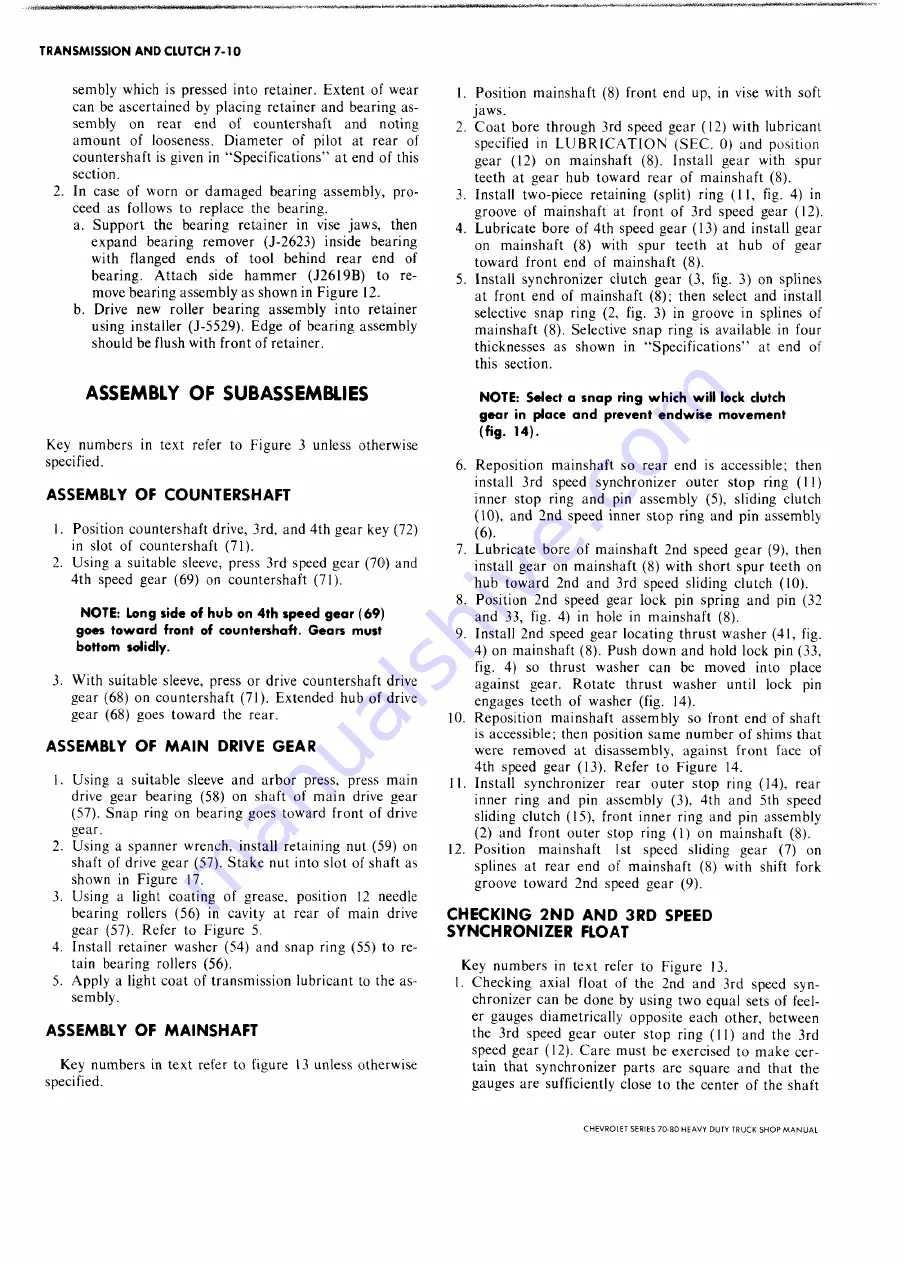
TRANSMISSION AND CLUTCH 7-10
sembly which is pressed into retainer. Extent of wear
can be ascertained by placing retainer and bearing as
sembly on rear end of countershaft and noting
am ount of looseness. Diameter of pilot at rear of
countershaft is given in “ Specifications” at end of this
section.
2. In case of worn or damaged bearing assembly, pro
ceed as follows to replace the bearing.
a. Support the bearing retainer in vise jaws, then
expand bearing remover (J-2623) inside bearing
with flanged ends of tool behind rear end of
bearing. Attach side ham m er (J2619B) to re
move bearing assembly as shown in Figure 12.
b. Drive new roller bearing assembly into retainer
using installer (J-5529). Edge of bearing assembly
should be flush with front of retainer.
ASSEMBLY OF SUBASSEMBLIES
Key numbers in text refer to Figure 3 unless otherwise
specified.
ASSEMBLY OF COUNTERSHAFT
1. Position countershaft drive, 3rd, and 4th gear key (72)
in slot of countershaft (71).
2. Using a suitable sleeve, press 3rd speed gear (70) and
4th speed gear (69) on countershaft (71).
NOTE: Long side of hub on 4th speed gear (69)
goes toward front of countershaft. Gears must
bottom solidly.
3. With suitable sleeve, press or drive countershaft drive
gear (68) on countershaft (71). Extended hub of drive
gear (68) goes toward the rear.
ASSEMBLY OF MAIN DRIVE GEAR
1. Using a suitable sleeve and arbor press, press main
drive gear bearing (58) on shaft of main drive gear
(57). Snap ring on bearing goes toward front of drive
gear.
2. Using a spanner wrench, install retaining nut (59) on
shaft of drive gear (57). Stake nut into slot of shaft as
shown in Figure 17.
3. Using a light coating of grease, position 12 needle
bearing rollers (56) in cavity at rear of main drive
gear (57). Refer to Figure 5.
4. Install retainer washer (54) and snap ring (55) to re
tain bearing rollers (56).
5. Apply a light coat of transmission lubricant to the as
sembly.
ASSEMBLY OF MAINSHAFT
Key numbers in text refer to figure 13 unless otherwise
specified.
1. Position mainshaft (8) front end up, in vise with soft
jaws.
2. Coat bore through 3rd speed gear (12) with lubricant
specified in L U B R IC A T IO N (SEC. 0) and position
gear (12) on mainshaft (8). Install gear with spur
teeth at gear hub toward rear of mainshaft (8).
3. Install two-piece retaining (split) ring (11, fig. 4) in
groove of mainshaft at front of 3rd speed gear (12).
4. Lubricate bore of 4th speed gear (13) and install gear
on mainshaft (8) with spur teeth at hub of gear
toward front end of mainshaft (8).
5. Install synchronizer clutch gear (3, fig. 3) on splines
at front end of mainshaft (8); then select and install
selective snap ring (2, fig. 3) in groove in splines of
mainshaft (8). Selective snap ring is available in four
thicknesses as shown in “ Specifications” at end of
this section.
NOTE: Select a snap ring which will lock clutch
gear in place and prevent endwise movement
(fig. 14).
6. Reposition mainshaft so rear end is accessible; then
install 3rd speed synchronizer outer stop ring (11)
inner stop ring and pin assembly (5), sliding clutch
(10), and 2nd speed inner stop ring and pin assembly
(
6
).
7.
Lubricate bore of mainshaft 2nd speed gear
(9),
then
install gear on mainshaft (8) with short spur teeth on
hub toward 2nd and 3rd speed sliding clutch (10).
8. Position 2nd speed gear lock pin spring and pin (32
and 33, fig. 4) in hole in mainshaft (8).
9.
Install 2nd speed gear locating thrust washer (41, fig.
4) on mainshaft (8). Push down and hold lock pin (33,
fig. 4) so thrust washer can be moved into place
against gear. Rotate thrust washer until lock pin
engages teeth of washer (fig. 14).
10. Reposition mainshaft assembly so front end of shaft
is accessible; then position same number of shims that
were removed at disassembly, against front face of
4th speed gear (13). Refer to Figure 14.
11. Install synchronizer rear outer stop ring (14), rear
inner ring and pin assembly (3), 4th and 5th speed
sliding clutch (15), front inner ring and pin assembly
(2) and front outer stop ring (1) on mainshaft (8).
12. Position mainshaft 1st speed sliding gear
(7)
on
splines at rear end of mainshaft (8) with shift fork
groove toward 2nd speed gear
(9).
CHECKIN G 2ND AND 3RD SPEED
SYNCHRONIZER FLOAT
Key numbers in text refer to Figure 13.
1. Checking axial float of the 2nd and 3rd speed syn
chronizer can be done by using two equal sets of feel
er gauges diametrically opposite each other, between
the 3rd speed gear outer stop ring (11) and the 3rd
speed gear (12). Care must be exercised to make cer
tain that synchronizer parts are square and that the
gauges are sufficiently close to the center of the shaft
CHEVROLET SERIES 70-80 HEAVY DUTY TRUCK S H O P M A N U A L
Summary of Contents for 70 1969 Series
Page 1: ...CHEVROLET HEAVY DUTY TRUCK SHOP MANUAL...
Page 3: ......
Page 11: ...LUBRICATION 0 4 CHEVROLET SERIES 70 80 HEAVY DUTY TRUCK SHOP MANUAL...
Page 27: ......
Page 119: ......
Page 361: ......
Page 371: ......
Page 427: ......
Page 443: ......
Page 451: ......
Page 493: ......
Page 499: ......
Page 549: ......
Page 555: ......
Page 609: ......
Page 715: ...am...
Page 745: ......
Page 910: ......
Page 913: ......