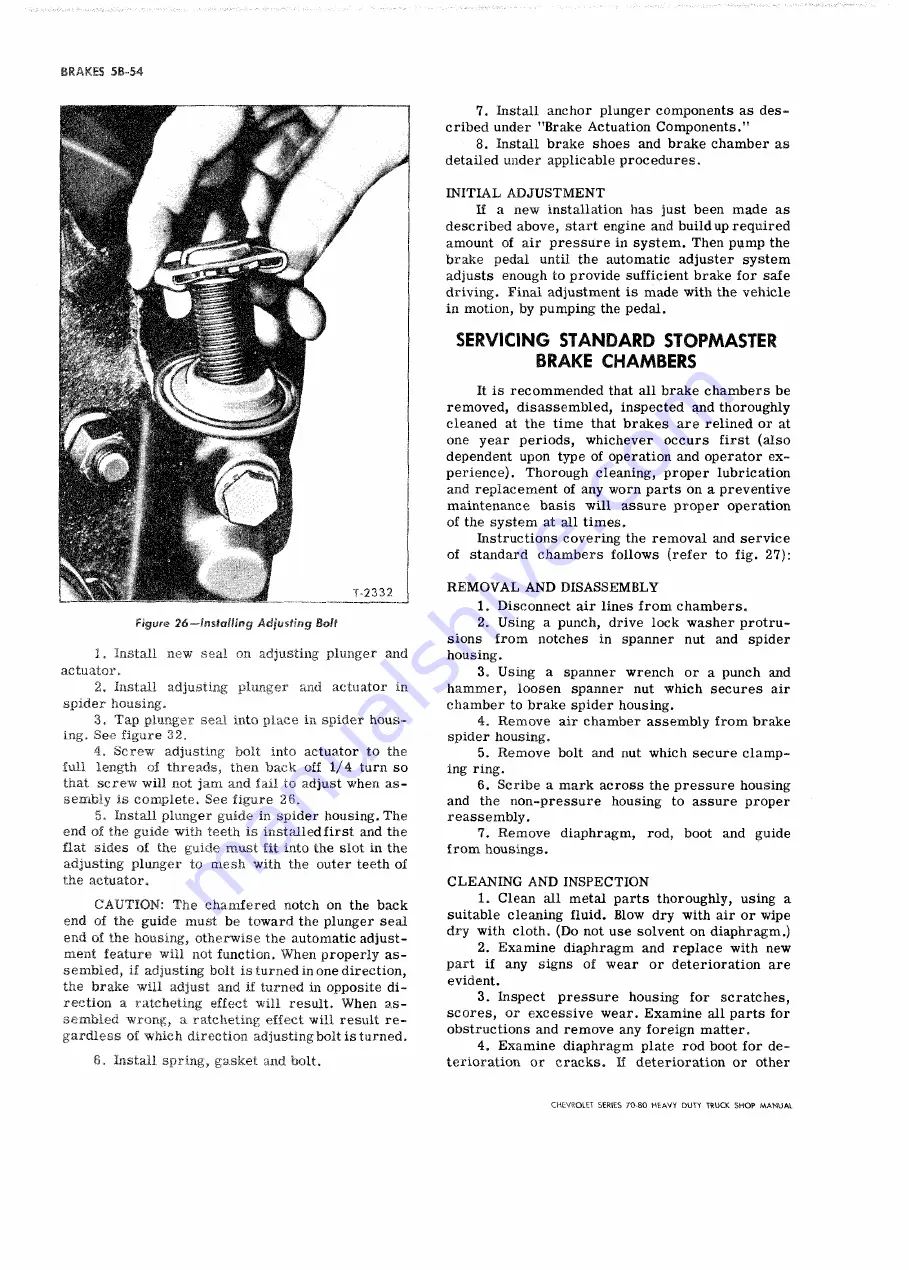
BRAKES
5 B -5 4
Figure 26—Installing Adjusting Bolt
1. Install new seal on adjusting plunger and
actuator,
2. Install adjusting plunger and actuator in
spider housing.
3. Tap plunger seal into place in spider hous
ing. See figure 32.
4, Screw adjusting bolt into actuator to the
full length of threads, then back off 1/4 turn so
that screw will not jam and fail to adjust when as
sembly is complete. See figure 26.
5, Install plunger guide in spider housing. The
end of the guide with teeth is installed first and the
flat sides of the guide must fit into the slot in the
adjusting plunger to mesh with the outer teeth of
the actuator.
C A U T IO N : The chamfered notch on the back
end of the guide must be toward the plunger seal
end of the housing, otherwise the automatic adjust
ment feature will not function. When properly as
sembled, if adjusting bolt is turned in one direction,
the brake will adjust and if turned in opposite di
rection a ratcheting effect will result. When as
sembled wrong, a ratcheting effect will result re
gardless of which direction adjusting bolt is turned.
6, Install spring, gasket and bolt.
7. Install anchor plunger components as des
cribed under "Brake Actuation Components."
8. Install brake shoes and brake chamber as
detailed under applicable procedures.
INITIAL A D J U S T M E N T
If a new installation has just been made as
described above, start engine and build up required
amount of air pressure in system. Then pijmp the
brake pedal until the automatic adjuster system
adjusts enough to provide sufficient brake for safe
driving. Final adjustment is made with the vehicle
in motion, by pumping the pedal.
SERVICING STANDARD STOPMASTER
BRAKE CHAMBERS
It is recommended that all brake chambers be
removed, disassembled, inspected and thoroughly
cleaned at the time that brakes are relined or at
one year periods, whichever occurs first (also
dependent upon type of operation and operator ex
perience). Thorough cleaning, proper lubrication
and replacement of any worn parts on a preventive
maintenance basis will assure proper operation
of the system at all times.
Instructions covering the removal and service
of standard chambers follows (refer to fig. 27):
R E M O V A L A N D DISASSEM BLY
1. Disconnect air lines from chambers.
2. Using a punch, drive lock washer protru
sions from notches in spanner nut and spider
housing.
3. Using a spanner wrench or a punch and
hammer, loosen spanner nut which secures air
chamber to brake spider housing.
4. Remove air chamber assembly from brake
spider housing.
5. Remove bolt and nut which secure clamp
ing ring.
6. Scribe a mark across the pressure housing
and the non-pressure housing to assure proper
reassembly.
7. Remove diaphragm, rod, boot and guide
from housings.
C L E A N IN G A N D INSPECTION
1. Clean all metal parts thoroughly, using a
suitable cleaning fluid. Blow dry with air or wipe
dry with cloth. (Do not use solvent on diaphragm.)
2. Examine diaphragm and replace with new
part if any signs of wear or deterioration are
evident.
3. Inspect pressure housing for scratches,
scores, or excessive wear. Examine all parts for
obstructions and remove any foreign matter.
4. Examine diaphragm plate rod boot for de
terioration or cracks. If deterioration or other
CHEVROLET SERIES 70-80 H EAVY DUTY TRUCK SH O P M A N U A L
Summary of Contents for 70 1969 Series
Page 1: ...CHEVROLET HEAVY DUTY TRUCK SHOP MANUAL...
Page 3: ......
Page 11: ...LUBRICATION 0 4 CHEVROLET SERIES 70 80 HEAVY DUTY TRUCK SHOP MANUAL...
Page 27: ......
Page 119: ......
Page 361: ......
Page 371: ......
Page 427: ......
Page 443: ......
Page 451: ......
Page 493: ......
Page 499: ......
Page 549: ......
Page 555: ......
Page 609: ......
Page 715: ...am...
Page 745: ......
Page 910: ......
Page 913: ......